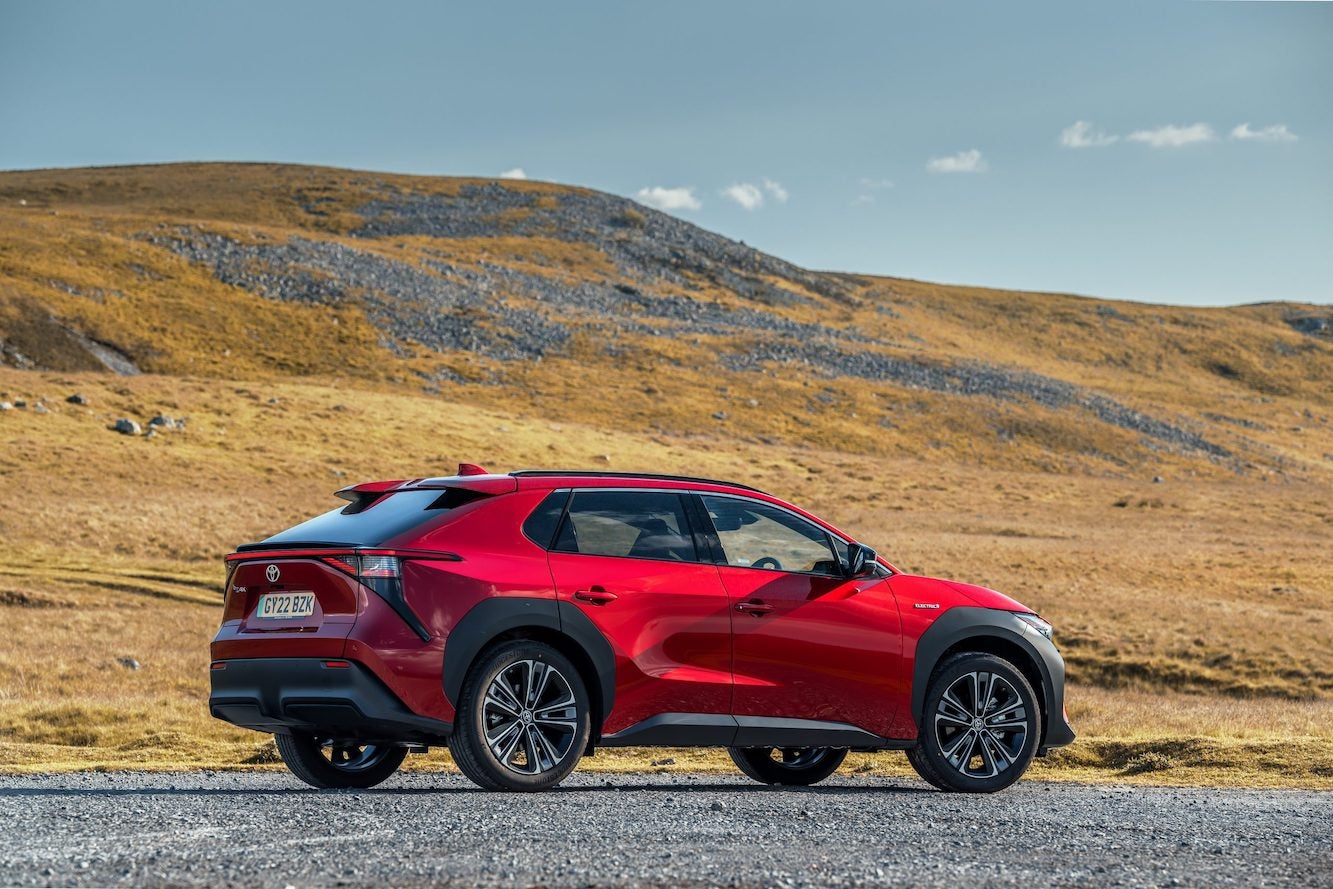
Under the tagline “let’s change the future of cars,” Toyota announced new technology to “support its transformation into a mobility company” which includes new EV battery types and vehicle construction methods.
According to media reports, the announcement came ahead of a crucial board meeting at which some green-focused shareholders were expected speedier progress towards a fully electric model range.
At the technical briefing in Japan, chief technology officer Hiroki Nakajima talked about specific and diverse technology, including concepts currently under development, which would will help Toyota “achieve the vision and policies it has communicated”.
He was joined by Takero Kato, president of the company’s new BEV production centre, and Mitsumasa Yamagata, who was scheduled to become president of the company’s hydrogen factory, to be launched in July. They provided more details of their respective strategies for the battery EV and hydrogen businesses.
Three approaches
Toyota had earlier said its three focuses were electrification, intelligence and diversification.
How well do you really know your competitors?
Access the most comprehensive Company Profiles on the market, powered by GlobalData. Save hours of research. Gain competitive edge.
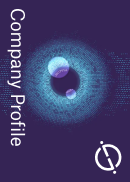
Thank you!
Your download email will arrive shortly
Not ready to buy yet? Download a free sample
We are confident about the unique quality of our Company Profiles. However, we want you to make the most beneficial decision for your business, so we offer a free sample that you can download by submitting the below form
By GlobalDataIn electrification, it would take a “multi-pathway approach,” including the introduction of optimal powertrains for each region.
In intelligence, in addition to vehicles and services, it would also promote initiatives to “expand its connection with society, such as Woven City”.
It would also continue to diversify its business by expanding scope from ‘cars’ to ‘society’ to “include freedom of mobility and diverse energy options for all”.
Consequently, it has been moving resources to advanced development and investing in future oriented areas since 2016.
By March 2023, half of R&D staff and R&D expenses had been transferred to advanced development fields, while increasing the total amount.
Localisation will be boosted.
“As the needs of our customers in each region will differ further in the future, we will accelerate ‘development near our customers’ at our R&D bases around the world,” the automaker said.
Despite criticism from some quarters it is laggin in EV development, Toyota countered: “We have overcome what were considered to be difficult challenges with [our] technological capabilities and developed numerous vehicles that are ahead of the times and paving the way for the future, such as Prius – now synonymous with hybrid vehicles – and the Mirai fuel cell car.”
Next generation strategy
Kato, the BEV factory president, said, through technology such as the integration of next generation batteries and sonics, Toyota would “achieve a vehicle cruising range of 1,000km (600 miles).
To produce “more stylish designs”, AI would be used to support aerodynamic performance. The Arene OS and full OTA (over the air) application would “infinitely expand the possibilities for how cars can be enjoyed”.
“Like the EV with a manual transmission, we will deliver exciting surprises and fun to our customers, with technology which can only be achieved by a carmaker, Kato claimed.
Vehicle build
On the manufacturing side, car bodies would be constructed from three main components in a new modular structure. Adopting giga casting would allow significant component introduction which in turn would contribute to the reduction of vehicle development costs and factory investment. Self propelling production technology would halve process and plant investment.
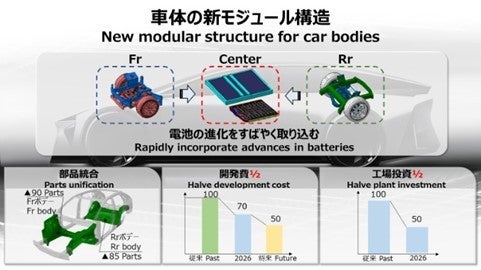
The BEV Factory was an “all in one team” under a single manager, unifying functions and regions beyond the framework of a carmaker, including Woven and external suppliers.
“This one team will revolutionise the way we work, with everyone on the same site and with the same awareness of the issues, achieving quick initial response and decision making,” Kato added.
“We will roll out next generation BEVs globally and as a full line-up to be launched in 2026.
“By 2030, 1.7m of 3.5m units overall will be provided by the BEV Factory.
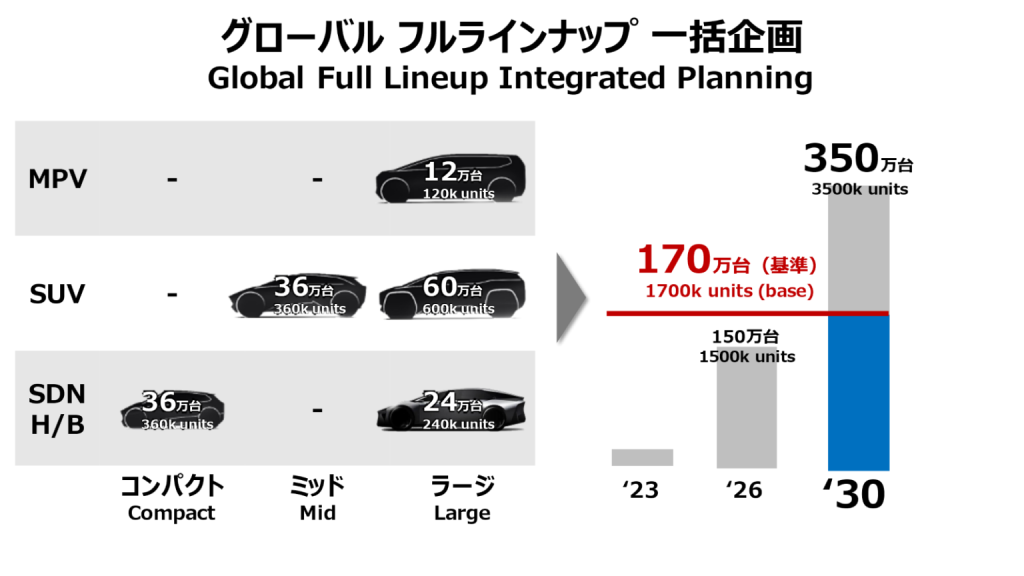
“These next generation BEVs will adopt new batteries, with which we are determined to become a world leader in energy consumption. With the resources we earn, we will improve the appeal of our products to exceed customer expectations and secure earnings.”
Hydrogen
Yamagata, the hydrogen factory president-designate said hydrogen markets in Europe, China and North America would be the world’s largest by 2030 and the fuel cell market was expected to expand rapidly towards that point, reaching JPY5 trillion (GBP5.7bn) a year.
He said: “We are promoting external sales of fuel cells, using the Mirai’s hydrogen units; we have received offers for 100,000 unit sales by 2030, most of them for commercial vehicles.
“To respond to the rapid changes in the market, we will establish a new organisation, the Hydrogen Factory, in July. This will be able to make immediate decisions under one manager, from sales to development and production, all at once.
The Hydrogen Factory would promote localisation of R&D and production in countries within the major world markets and boost establishing local bases, mainly in Europe and China.
Alliances with suppliers would be extended.
“We will do our best to deliver affordable fuel cells to our customers by consolidating sufficient quantities through alliances,” Yamagata said.
Toyota would work on the “innovative evolution of competitive next generation FC technologies,” such as cell technology and FC systems.
“We will work towards full-scale commercialisation as we move forward with these initiatives.
“The next generation system will achieve 37% cost reduction through technological progress, volume efficiency and localisation. In collaboration with partners, if we receive and offer for 200,000 units in 2030, we will be able to [halve the cost] and generate a solid profit.”
But he cautioned “the price of hydrogen remains very high” and Toyota would continue to contribute to the production, transport and use of hydrogen.
“We will take the relationships we have built with strong partners as opportunities to commercialise hydrogen by establishing customer-oriented bases in major markets and by offering affordable products in sufficient quantities.”
Battery technology
Liquid lithium-ion batteries, which are currently the mainstream, would gain performance through improvement of energy density in square batteries, an area where Toyota has long expertise. By adopting the bipolar structure developed for hybrid electric vehicles (HEVs) for BEVs, the automaker would expand its range and offer options from low cost to batteries “designed for higher performance”.
“Highly anticipated” all solid state batteries were “entering the practical application phase for use in BEVs. Toyota’s full line-up of competitive batteries will support the future evolution of the company’s BEVs”.
The performance version of the next generation battery is being developed with Prime Planet Energy and Solutions Corporation; the ‘popular’ and high performance versions and the solid state BEV battery are being developed with Toyota Industries.
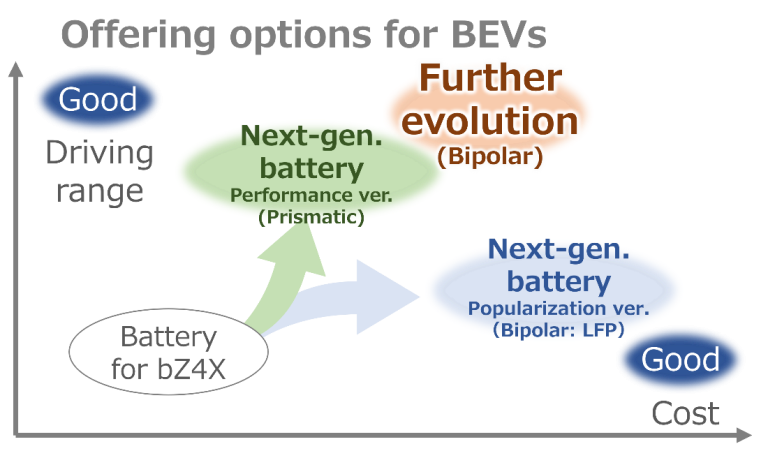
Performance version
The next generation BEV, to be introduced in 2026, would have a cruising range of 1,000km and Toyota was developing a square battery with a focus on performance for installation in such cars.
While the battery’s energy density would be increased, cruising range wou;d be increased through higher efficiency in areas such as aerodynamics and weight reduction. Costs would be reduced 20% compared to the current bZ4X, and quick charging (10%-80%) will take 20 minutes or less.
Popular version
Toyota was also developing low-cost batteries to encourage spread and expansion of BEVs. The bipolar structure battery, which has been used in the (Japan domestic market) Aqua and Crown hybrid vehicles, was now being applied to BEVs. This uses inexpensive lithium iron phosphate (LFP) and was expected in BEVs in 2026-2027.
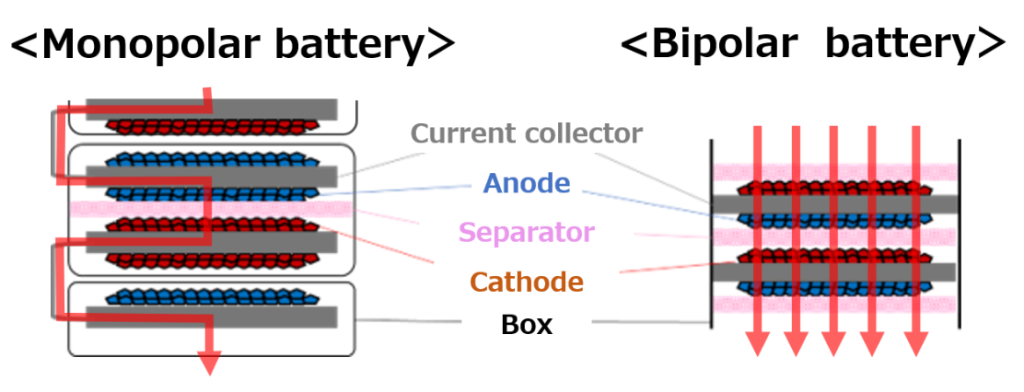
Toyota was aiming for a 20% cruising range boost, 40% cost reduction and quick 10%-80% recharging in under 30 minutes compared to the current bZ4X. It was considering installing the battery in BEVs in the popular market price range.
Bipolar lithium-ion battery aka high performance version
A high performance battery combining bipolar structure with high nickel cathode would “be put to practical use in 2027-2028”. It would achieve greater performance than the ‘performance’ version of the square battery with a claimed 10% increase in cruising range, 10% cost reduction and quick charge time of 20 minutes.
BEV solid state batteries
“Having discovered a technological breakthrough that overcomes the longstanding challenge of battery durability”, Toyota was reviewing introduction of all solid state batteries for conventional HEVs and accelerating development as a battery for BEVs, “for which expectations are rising”.
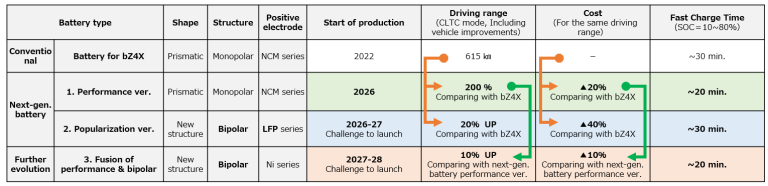
It was developing a method for mass production, aiming for commercialisation in 2027-2028.
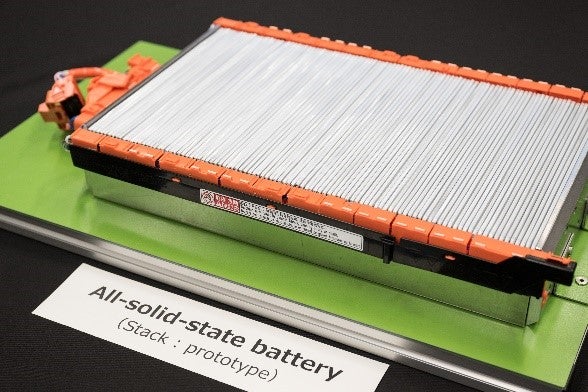
Toyota was looking for a 20% cruising range boost compared to the performance version of the square battery. Costs were “under scrutiny” and the aim was for a quick charging time of 10 minutes or less. A higher level specification was being researched and developed at the same time with the aim of a 50% improvement in cruising range.
Aerodynamics
Toyota using hypersonic technology for rockets for BEVs. It was collaborating with Mitsubishi Heavy Industries on a new technology to reduce aerodynamic drag in any shape. Minimising aerodynamic drag would improve BEV performance “beyond customer expectations”. By being able to reduce aerodynamic drag without being restricted by the shape of the car, it was expected to combine attractive design and packaging with aerodynamic performance (Cd0.1 level in view).
“Technology development is under way in different speed ranges, applying knowledge of boundary layer control in the ultra-high-speed range obtained from aerospace technology,” the automaker said.
Production processes
To ensure BEV profitability, Toyota would work on both vehicle technology and manufacturing methods. First, the vehicle body will have a simple and slim structure, moulded using giga casting, for significant parts integration. Highly flexible production plants without conveyors would introduce concepts such as a self-propelling assembly line.
Digital technology would be used in the design of the BEV plant, to increase the accuracy of process verification. This would reduce production preparation lead time, production process and factor in investment for mass production.
Giga casting
This achieves high productivity, with integrated moulding of optimum shapes. Toyota was also developing technology for integrated moulding with aluminium die casting for what previously was made with dozens of sheet metal parts.
After analysing car manufacturing casting technology that has achieved a high degree of precision, the automaker had reviewed the structural design to make it simpler and slimmer.
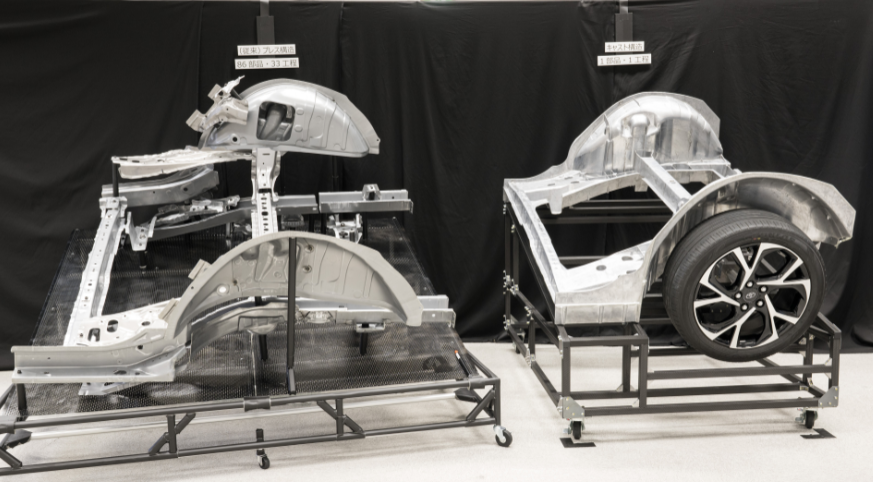
As well as reducing the number of parts and processes, this also reflects the Toyota Production System (TPS) philosophy of eliminating waste in each process.
Self-propelling assembly line
Toyota said it would “take on the challenge of designing a next generation production plant that dispenses with the concept of a conveyor”. This was being developed so mass-produced cars under assembly could move from one process to the next on their own.
Factory sensors and control systems communicate with wireless terminals on the vehicles to control them externally, integrating car and assembly plant.

Eliminating conveyors would make factory layouts more flexible and significantly factory investment, lead times and people required to prepare for mass production – activities which used to take years.
Next generation plant design
Toyota would look at digital technology for manufacturing in its next generation BEV plant. Technologies such as giga casting and self-driving assembly lines are compatible with digitisation; digital technology would be actively employed, including for process study and improvement. Lead time preparation for mass production would be reduced through reproduction accuracy to 1mm error level.
Toyota would shift to more efficient production lines with unmanned transport, using methods such as connected technology, autonomous inspections and others.
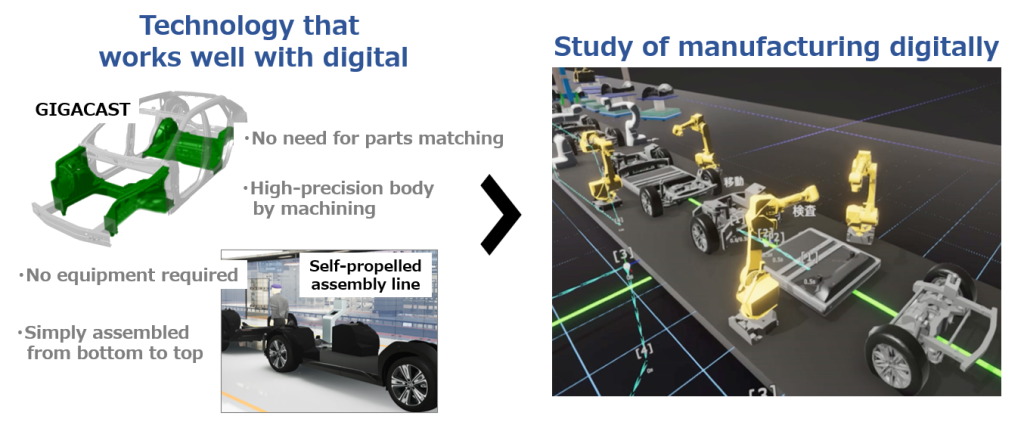
It will take up the challenge to “drastically change manufacturing”, by adopting TPS concepts and other measures.
Technology to improve BEV appeal
Toyota said it was further developing “fundamental” technology, most of which were developed through manufacturing. The Toyota Group as a whole would take advantage of small eAxle and future semiconductors to improve the commercial potential of the BEVs under development.
Small eAxle
It was developing a small eAxle, downsizing key components such as the motor, geartrain and inverter plus making full use of BlueE Nexus, Aisin, Denso and in-house technology, developed for HEVs.
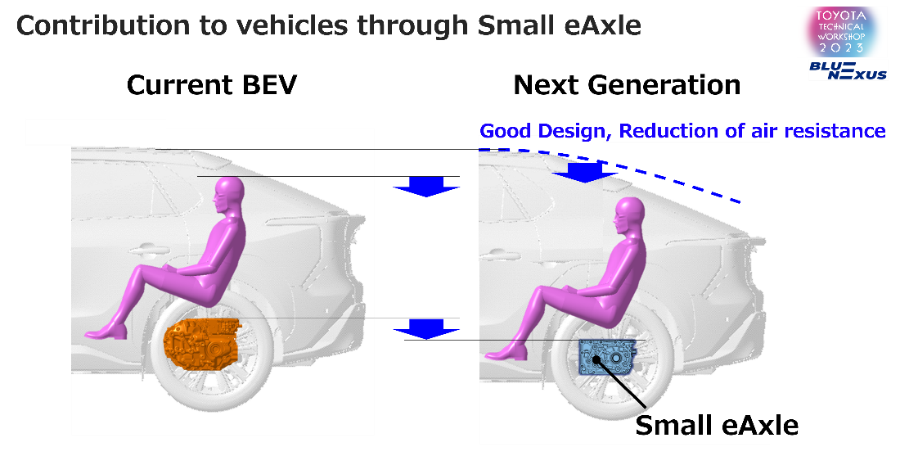
A longer cruising range has been achieved by downsizing the eAxle while the smaller unit also increases load space and reduces aerodynamic drag.
SiC wafers for BEV inverters
Next generation semiconductors would have 50% less power loss while development of semiconductor materials from crystal growth would contribute to reduced energy consumption.
In addition to the gas method, which has the advantage of 10 times faster crystal growth than the industry standard, Toyota was developing the industry’s claimed largest eight inch wafer. This would “promote the internalisation of technology within the group”.
‘Multi-pathway’ platform
Toyota said it would will develop a platform which would enable it to offer a variety of electrified vehicles and has converted the powertrain of the (Japanese market) Crown model into a BEV.
Hydrogen
The automaker saw hydrogen as an important fuel to reduce CO2 emissions and reach carbon neutrality and was working with others on hydrogen production, transportat and use.
It was also developing and demonstrating fuel cell electric vehicles (FCEVs), including passenger cars, commercial trucks and buses, FC stationary generators and vehicles using hydrogen combustion engines.
Next generation fuel cell
It was also developing new fuel cells to deliver claimed industry leading performance for commercial use, with long life, low cost and low fuel consumption. It aims for these to be commercialised in 2026.
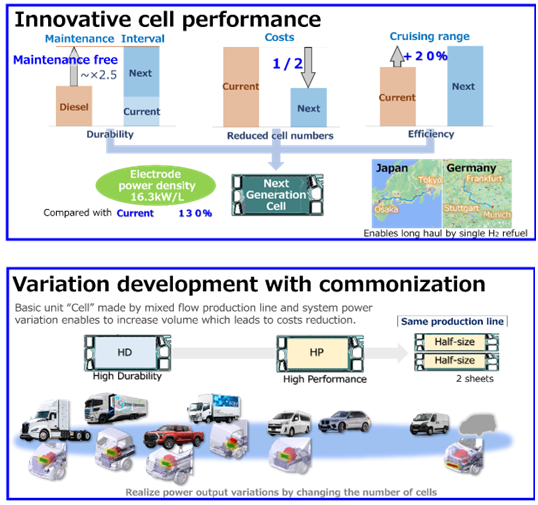
It was aiming for easier maintenance compared to diesel vehicles and to halve the cost of a fuel cell stack versus current models. It also expected to improve cruising range by 20%.
Large commercial tanks
Toyota was working on the issue of standardising tanks for large commercial vehicles which were expected to consume a large volume of hydrogen. This would help accelerate hydrogen demand and the aim was to reduce manufacturing costs 25% by unifying tank standards for Europe, America and Japan and consolidating total quantity. It was also developing liquid hydrogen tanks for large commercial vehicles.
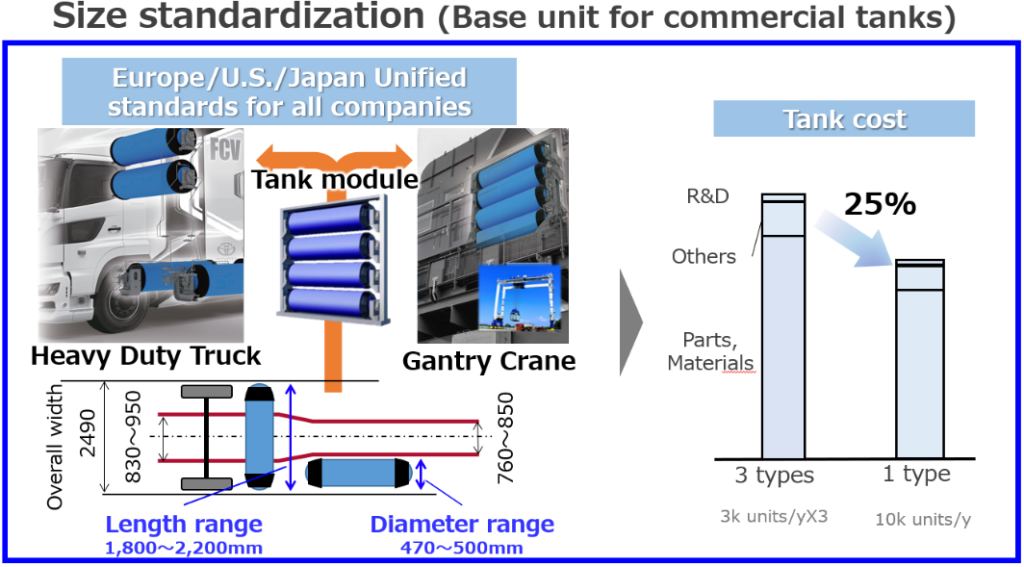
Multi hydrogen tank concept
Toyota also said it was developing hydrogen tanks easy to install and compatible with different vehicle types and sizes. It would be possible to convert existing vehicles to use hydrogen fuel cells and hydrogen combustion engines.
Hydrogen production
Toyota said it had produced a new water electrolyser to produce hydrogen, applying fuel cell stack and cell technology developed for the Mirai FCEV. Public trials had started at Denso’s Fukushima plant.
It has launched a project to produce hydrogen from biogas derived from local chicken manure and food waste in Thailand by the end of 2023, working with Mitsubishi Kakoki and Toyota Tsusho.
Hydrogen engine vehicle
As previously announced, Toyota had developed a trial hydrogen-engine vehicle, licensed to be driven on public roads in Japan. This would speed the development of such vehicles for commercialisation as a new option to achieve carbon neutrality.
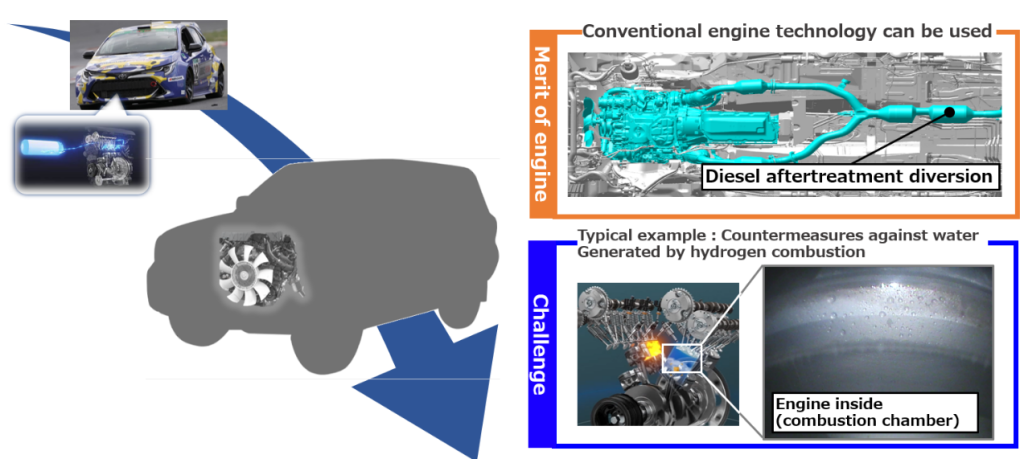
It would also consider the entire vehicle, for example incorporating an exhaust purification system which uses established diesel engine technology.
Carbon neutral fuel
Toyota said it would work with parties to promote biofuel use which would lead to publicly available CN fuel. To achieve carbon neutrality, it was important to promote the spread of electrified vehicles, especially vianew car sales, but also to reduce CO2 emissions from daily use cars already on the road. To meet requirements of diverse vehicle types, regions and customers, a variety of energy options must be offered, the automaker said. It was working with various groups, across industry boundaries, to reduce CO2 emissions and run public trials of hydrogen and synthetic and bioethanol fuels, based on electricity from renewable energy sources.
e-fuel
In regions where hydrogen was inexpensive, it was produced and consumed locally as-is in fuel cell systems. In areas where hydrogen was expensive, Toyota would look at the potential for cost reduction by producing and transporting e-fuel.
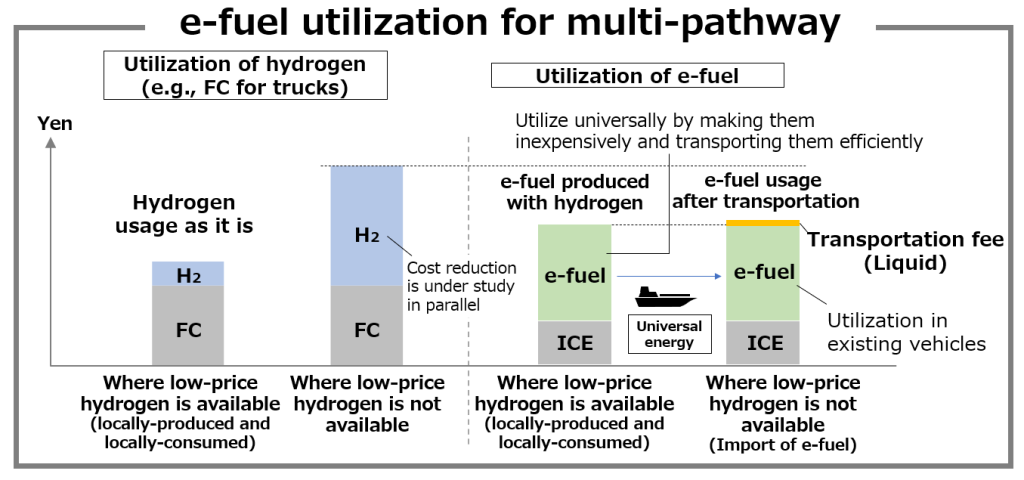
Biofuel
In July 2022, seven private companies, including Toyota, established the Research Association of Biomass Innovation for Next Generation Automobile Fuels to promote research into production of second generation bioethanol fuel. Toyota was expanding bioethanol use in emerging countries by promoting deployment of “the right vehicle, in the right place, at the right time” and this included the introduction of biofuel/ethanol-compatible models. Ten percent biofuel can be used in all vehicle types; in Brazil, Toyota HEVs are 100% biofuel-compatible; and in India HEVs that can be adapted to use biofuel were to be launched according to a November 2022 announcement.
In car intelligence
Toyota said it would expand updating of safety technology, multimedia and other functions to all vehicles. With a new voice recognition system, the Arene OS would accelerate the shift to car intelligence, with quick response and flexible suggestions that would make the driver feel as though they were talking to a human being. Alongside the evolution of the car’s operating system, the next generation BEV would also enable customisation of the driving feel, focusing on acceleration, turning and stopping.
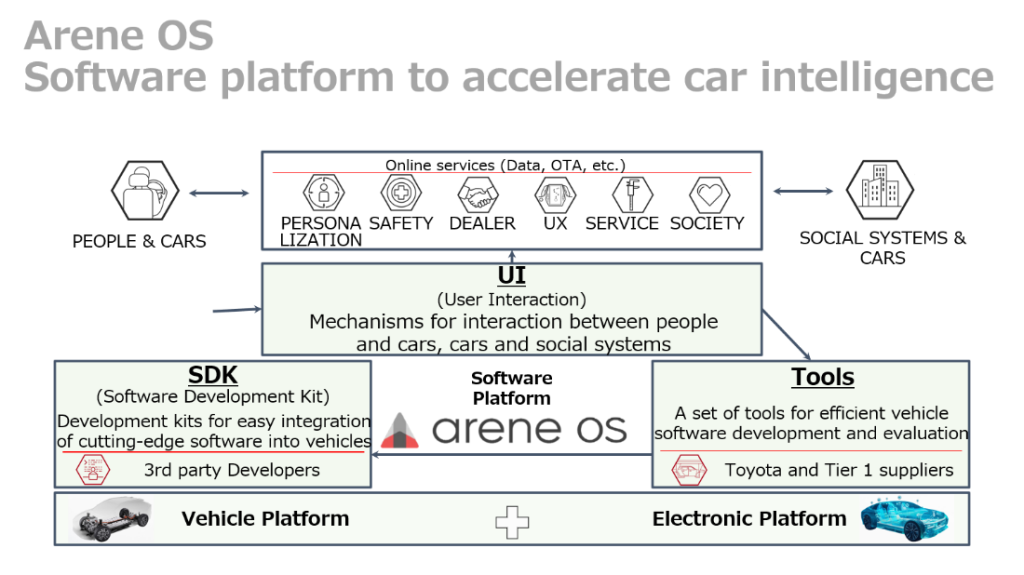