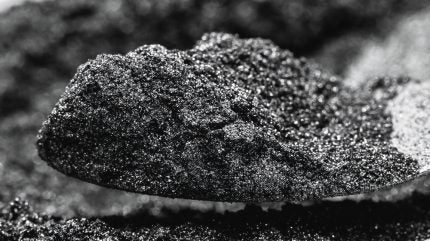
Downtime is a significant challenge throughout the manufacturing industry, causing delays and increasing costs. This is just as true in graphite milling, where reducing downtime is crucial for efficient and consistent production in an industry that is seeing rapid growth.
The goal is to reduce maintenance, improve equipment reliability, and ensure full containment to minimise cleaning and potential worker health issues. However, there are other factors that can contribute to downtime in milling, including supply chain bottlenecks for raw materials.
The majority of graphite processing is currently concentrated in China and this dependency creates a risk of supply-chain disruption and delay in the supply of raw graphite. Additionally, many North American processors of graphite rely on Chinese manufacturers for their key processing equipment. This reliance can lead to delays in equipment procurement and maintenance, which can contribute to downtime in processing operations.
Here, we examine the necessity for graphite, the difficulties associated with milling, and ways to minimise downtime by using the most reliable equipment and containment facilities.
An increasing need of graphite
Lithium-ion batteries are crucial components within the power sector and especially for electric vehicles (EVs). According to the most recent data available from GlobalDatai, in 2023 the total sales volume of all types of EVs (including hybrids) was approximately 24.7 million, expected to account for more than 50% of light vehicle production by 2035.
Lithium-ion batteries (LIBs) have a high performance based on their charge and discharge capacity, cycle life, and rate performance. Graphite is commonly used as anode material due to its stable electrochemical performance and capacity.
To provide for this market, global graphite production is projected to rise to 1,567.2kt in 2025, with China as the largest producer. This dependence on China for graphite has led some economic regions – like the US and EU – to invest heavily in diversifying supply, with the EU investing EUR10 million in the sustainable processing and refining of battery grade graphiteii. By fostering local supply chains, the industry can reduce dependence and potential downtime caused by transportation and logistical challenges.
Challenges with milling graphite
Milling bulk graphite material to ultra-fine micron size increases the amount of space available for storing lithium ions and enhances performance.
However, worker safety is an issue, as graphite dust poses a significant health risk. Its small particles can harm lungs if breathed in and can also irritate eyes and skin. To prevent irritation and sickness, measures must be taken to protect workers.
Effective containment in graphite milling reduces downtime by minimising the release of graphite dust and particles into the surrounding environment. This helps to maintain a clean and safe working environment, prevents contamination of machinery and equipment, and reduces the risk of respiratory issues for workers.
Additionally, by implementing proper containment measures, such as using dust collection systems and ensuring sealed milling equipment, the amount of downtime needed for cleaning and maintenance can be significantly reduced.
Crushing downtimes using reliable equipment
Frewitt is a premium mill and turn-key solution manufacturer at the forefront in the development of anode and cathode processes, as well as the manufacturing of customised premium quality mills and production handling systems. Based in Switzerland, Frewitt has been creating and producing high-end milling and handling solutions since 1946 by adhering to the country’s well-known quality standards.
Frewitt prioritises providing optimal process solutions and cutting-edge milling solutions, focusing on customer needs and anticipating future battery industry trends. Frewitt provides complete, adaptable solutions, designed for long term operation, with reliable, Swiss-made equipment.
Frewitt equipment is also modular, allowing full scaleup and many processes can be automated, both to boost efficiency and to protect workers’ health.
Frewitt has rapidly gained recognition within the graphite milling industry thanks to its PowerMill PMV-320, which, following extensive trials, was found to provide high performance and fine milling efficiency of graphite while ensuring complete operator safety.
The Power Mill PMV-320 is a patented system by Frewitt that combines containment and micronisation processes., with the mill operating in a partial vacuum environment. The mill is controlled by pressure sensors and features a temperature sensor for redundancy. This system also shuts down milling machinery automatically in the unlikely event of overheating.
Complimenting milling solutions, Frewitt offers full turnkey solutions, covering not only milling, but every process through the graphite process cycle, from transport and handling of raw bulk materials, to monitoring milling, and subsequent transport downstream for any supplementary processes that may be required. Partnering with an expert turnkey provider can streamline development processes without the burden of costs associated with in-house process design and manufacturing.
To find out more and discuss your milling and handling requirement needs in person, join Frewitt at Europe’s largest advanced battery and electric vehicle tech conference The Battery Show Europe 18-20 June 2024, in Stuttgart, Germany.
For further information on Frewitt’s milling equipment, please download the whitepaper below.
[i] GlobalData: Global Light Vehicle Hybrid and EV database.
[ii] https://www.horizon-europe.gouv.fr/sustainable-processing-and-refining-battery-grade-graphite-batteries-partnership-26438