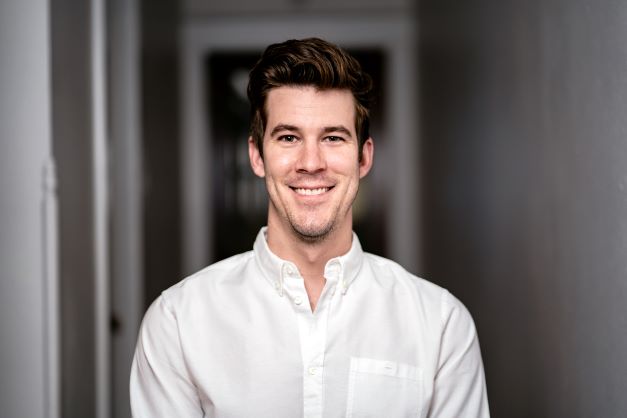
Solid-State Battery Revolution: Powering the Future of Electric Vehicles
Could you tell us a little about the science behind your solid-state battery cells and the disruptive aspect of it?
Solid Power replaces the flammable liquid electrolyte in a conventional lithium-ion battery with a proprietary sulfide-based solid electrolyte. As a result, Solid Power’s all-solid-state battery cells are expected to be safer and more stable across a broad temperature range and provide an increase in energy density compared to the best available rechargeable battery cells. Solid Power also anticipates our all-solid-state battery cells will enable less expensive battery pack designs due to the removal of expensive and extensively engineered battery pack cooling schemes. Solid Power’s battery technology is compatible with traditional lithium-ion manufacturing processes, which we anticipate will speed our path to market and keep our cell prices competitive with today’s and tomorrow’s industry-standard lithium-ion battery cells.
What are your thoughts on the current battery technology landscape and the future of solid-state technology?
Today’s liquid electrolyte-based lithium-ion battery cell technology helped introduce the possibility of broad adoption of electric vehicles. However, this first-generation technology is reaching a practical limit where further investments into development provide diminishing returns due to concerns about safety, energy density, and stability. Without further improvements to electric vehicle battery pack performance, consumer demand for electric vehicles may plateau over time. Specifically, we believe that today’s liquid electrolyte-based lithium-ion battery cells suffer from four key problems that discourage the widespread acceptance of electric vehicles:
- Limited drive range. Current lithium-ion battery cell technology does not provide enough energy density to support extended drives before requiring recharging.
- Short calendar life. We estimate that today’s electric vehicle battery cells typically will have a calendar life (i.e., before seeing significant degradation) that is shorter than the average age of the average passenger vehicle in operation, which IHS Markit estimated was 11.9 years in 2020. This disparity must be addressed so owners of electric vehicles can keep their vehicles, without having to replace battery packs, for at least as long as they would typically keep their comparable traditional internal combustion vehicles.
- Abuse tolerance. The liquid electrolyte-based lithium-ion battery cell used in current electric vehicle battery packs contains highly flammable and volatile components that create safety risks when exposed to abuse conditions.
- Expensive materials and pack systems. Today’s battery packs are complex and, due to temperature sensitivity and the highly flammable and volatile components, require cooling systems to maintain stability and considerable engineering to mitigate risk. This increases the cost of battery pack production.
Solid Power’s all-solid-state battery cell technology addresses these roadblocks. By simplifying the design of solid-state versus lithium-ion batteries, Solid Power can increase vehicle range, improve interior space and cargo volume, deliver lower costs and better value for customers and more efficiently integrate this kind of solid-state battery cell technology into existing lithium-ion cell production processes – a key barrier for the current battery market.
Could you add a little more colour around your relationship with Ford and BMW?
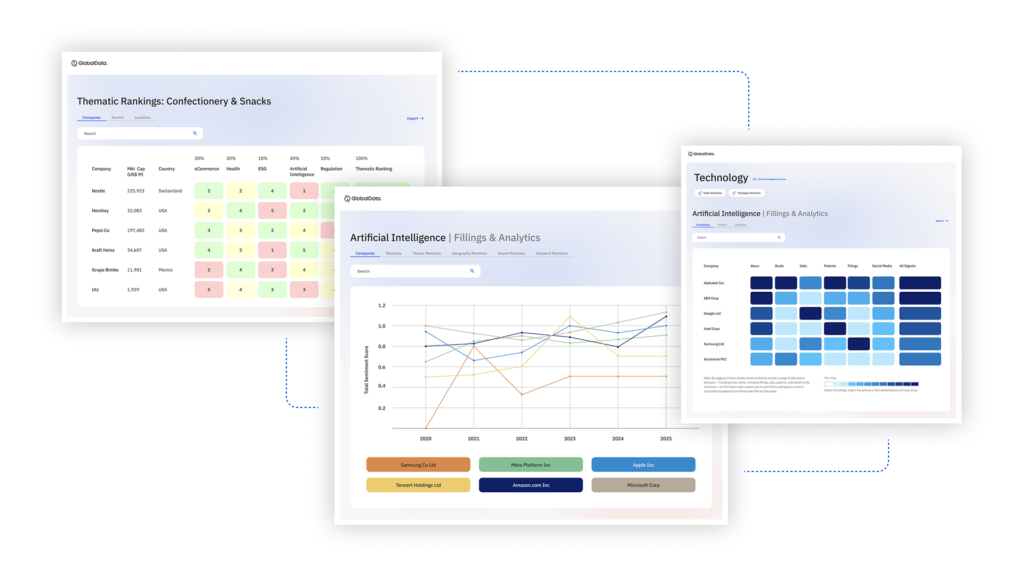
US Tariffs are shifting - will you react or anticipate?
Don’t let policy changes catch you off guard. Stay proactive with real-time data and expert analysis.
By GlobalDataSolid Power began its relationship with BMW in 2017 announcing a joint development agreement to develop all-solid-state batteries for electric vehicles. In 2018, Solid Power raised its Series A, which Ford participated in. We also announced a JDA to develop all-solid-state batteries for electric vehicles. In May 2021, BMW and Ford both participated in Solid Power’s Series B and expanded their existing joint development agreements in order to secure Solid Power’s batteries for forthcoming electric vehicles. Solid Power anticipates delivering full-scale “A Sample” all-solid-state cells in 2022, officially entering into the automotive qualification process. Solid Power anticipates to be the first next-gen battery to enter into auto qualification in 2022.
In terms of production, we understand that Solid Power is close to reaching full autonomy. Could you update us on the stage reached?
Today, Solid Power operates a Colorado-based pilot production line that is capable of building prototype all-solid-state cells for testing purposes. In 2022, Solid Power anticipates the completion of its “EV Cell Line” that will be capable of building full-scale automotive cells specifically for the automotive qualification process.
In October 2021, Solid Power announced a partnership with South Korean lithium-ion battery producer, SK Innovation. The partnership is intended to allow SK Innovation to produce Solid Power’s cells for the later stages of automotive qualification. Long term, Solid Power anticipates licensing its cell business to a third-party cell manufacturer while producing and selling in the core solid electrolyte material. In addition to this, Solid Power announced a second Colorado-based facility in October where it anticipates increasing electrolyte production by 25x.
What opportunities does this partnership with SK Innovation bring?
With the battery market poised to grow by $82.89 billion between 2021-2025, companies must achieve battery production processes that are scalable and compatible with existing lithium-ion production technology to remain successful in an increasingly crowded field. Solid Power intends to utilize this by licensing its proprietary cell technology, manufacturing know-how and practices to SK Innovation to enable full integration of the company’s sulfide-based solid electrolyte material into SK Innovation’s existing cell production environment. This could allow Solid Power a quicker path to market that is much more capital efficient as we don’t intend to raise and deploy billions to build our own giga factories.
Solid Power has a special purpose acquisition company (SPAC) merger finalizing soon with Riverstone Holdings’ Decarbonisation Plus Acquisition Corporation III (DCRC). How will you use the capital and how do you see the company by late 2023?
Solid Power is laser-focused on our commitments to our two automotive partners, BMW and Ford. We anticipate building our EV Cell Line in 2022 to produce full-scale automotive batteries for automotive qualification testing while expanding the production of our solid electrolyte material. In 2023, Solid Power anticipates moving to the second stage of automotive qualification testing, which would end with a cell design that meets all automotive requirements and is design frozen.
We understand that some carmakers (VW, Tesla and even Apple) are taking a greater interest in LFP (lithium-iron-phosphate) cathode material chemistries. Why such interest in material chemistry now? Does this signal a shift across the EV industry?
LFP is coming back “into style” mainly for cost reasons.
Solid Power’s cells are anticipated to be $85/kWh when produced at scale, which is lower than today’s NMC-based cell design costs. We believe it will be in line with NMC cell costs in 2025-2026. Solid Power see’s further cost savings with its all-solid-state cell, specifically at the pack level due to the removal of costly battery pack cooling, which accounts for roughly 10 per cent of the pack cost.
Solid Power and SK Innovation collaborating on EV cells
BMW/Solid Power to develop solid-state batteries for EV applications