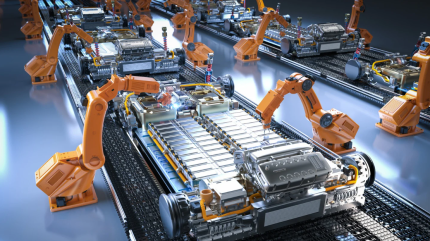
The electric vehicle (EV) industry is continuing its rapid acceleration towards widespread adoption. Recent analysis by the AA, a UK-based motoring association has found that recharging an EV at home is now 60% cheaper than the petrol equivalent in the UK as of July 2024. Supply is rising to meet demand: GlobalData research suggests EV production will reach over 17 million units by 2025, making up 18.4% of total light vehicle production. This will rise to 28.3 million units, nearly 30% of all production, by 2028. Sales are set to soar.
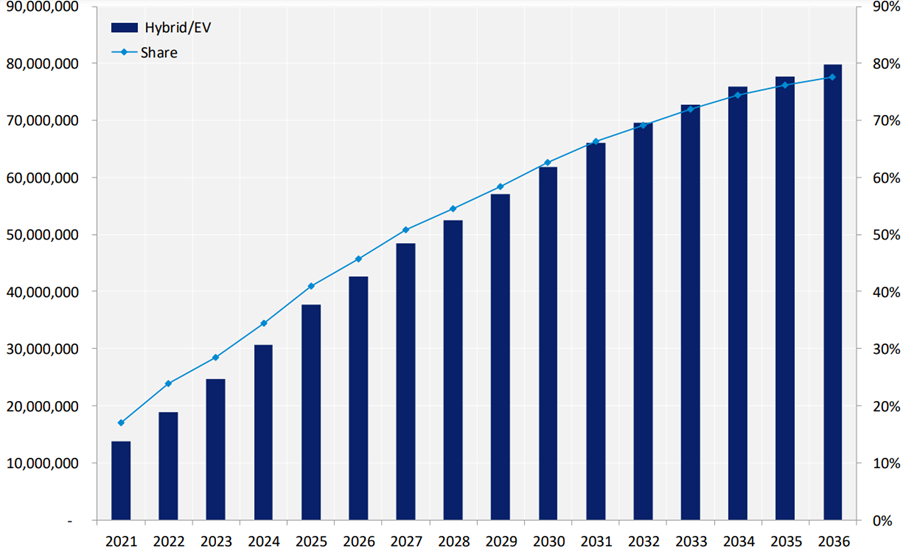
Balancing EV safety and efficiency will be critical as the sector continues to expand. One of the most significant challenges in EV design is the management of battery thermal conditions. Thermal management is at the core of battery longevity, performance and safety; all three will suffer if an EV battery system is poorly maintained.
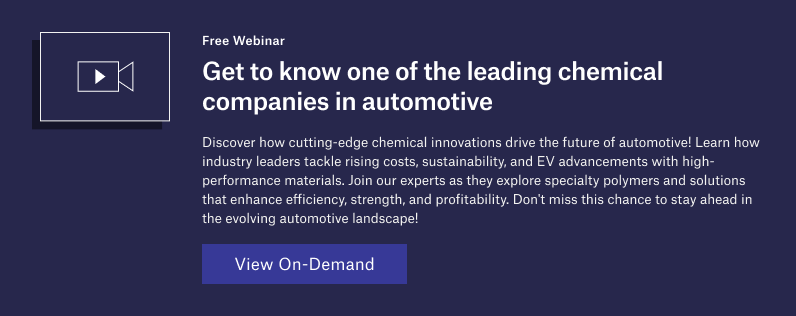
Thermal spacers, which sit between battery cells to regulate heat flow between them, play a crucial role. They are the primary safeguard keeping battery heat within the boundaries necessary to maintain top performance – and are central to insulating passengers against potentially catastrophic thermal runaway events.
Changes on the horizon
From 2010 to June 2023, there were 488 reported light-duty EV fires globally. Although substantially lower than internal combustion engine vehicles, these figures will climb as more EV vehicles hit the road – and regulators are taking notice. China’s GB38031-2020 for electric vehicle battery safety currently requires that no fire or explosion occurs for at least 5 minutes after a thermal event, providing time for evacuation. A proposed revision, due for implementation in 2026, will tighten these conditions – and set a new global standard in EV fire safety. The five-minute window will expand to 2 hours, with an additional requirement that battery temperatures must cool below 60°C within that period. It also includes tests to assess the effects of high-speed charging and external short circuits, as repeated fast charging can pose safety risks.
It is a significant shift, underscoring the increased focus on safety in the EV industry. With the Chinese market a bellwether for global automotive standards, these regulations are expected to influence safety protocols worldwide.
This is where thermal spacers come in. Strategically placed between battery cells to manage propagation of heat from one cell to the next, they can maintain battery efficiency while mitigating risks of thermal runaway. Crucially, they regulate both the normal operational needs of the battery—where efficient heat dissipation is crucial—and the extreme conditions where the priority shifts to containment and isolation of heat to prevent it from spreading.
The problem is that existing thermal spacer solutions risk falling foul of looming legal shifts. In addition to their insulating properties, the exceptionally light weight of aerogels has made them the go-to material for thermal spacers among EV manufacturers up to now. But their adherence to the two hour thermal event and cooling window is not clear from industry-standard burner tests. Manufacturers need to consider new solutions – and fast.
What should they look for in an effective thermal spacer? A clear starting point is high-temperature resistance, with spacers exhibiting resilience against degradation during thermal runaway to prevent heat spread. Thermal spacer materials should also conduct heat away from the cells during normal operation. This helps to maintain a uniform temperature across the battery pack, essential for the battery’s longevity and performance. And this resistance and conductivity need to act in tandem; a material capable of thermal switching, or shifting from conductor to insulator at high temperatures, helps to manage heat more effectively across a range of operating conditions. Mechanical durability is vital, ensuring the spacer maintains structural integrity under the mechanical stresses occurring within battery packs. Like their aerogel forerunners, any new spacer materials will need to deal with the compression and expansion phases present during charge and discharge cycles. Most of all, they must be futureproof – as regulatory scrutiny intensified, spacers need to withstand industry-standard burner tests to prove they can withstand intense heat, unscathed, over an extended period of time.
The leaders in thermal spacing
Incorporating the efficiency of previous spacing solutions with the fire safety stipulations of the future requires innovation. And, turning to the industry experts, there are promising signs.
Mitsubishi Chemical Group, for example, has developed a range of thermal spacers that are pushing boundaries in harmonising efficiency and safety. They boast thermal switching features that mean they can prevent heat spread amid thermal runaways while conducting heat at low temperatures to maintain even performance. Crucially, utilising a spacer thickness of just two millimetres between cells has been shown to pass burner tests, preventing propagation and meeting the requirements of novel regulations. Cycle simulations have also found that the lifespan of a Mitsubishi thermal spacer is substantially longer than conventional aerogel solutions – with 8% capacity loss at 1,700 cycles in the former case and 800 in the latter.
According to Tomohiro Kawai, senior chief scientist and product design leader at Mitsubishi Chemical Group, and one of the new thermal spacer’s developers: “The main thermal spacer candidates up to now have dealt with extreme heat, but this is an abnormal situation. Our solution contributes not only to these abnormal situations but also creating better conditions during the normal running of the vehicle. Existing materials stop energy release altogether; our material manages it.”
Efforts to refine and improve thermal spacer technology is ongoing. Mitsubishi Chemical Group’s THERMINSYNX™ spacers promise next-generation thermo-mechanical control. Once completed, they will offer even greater heat resistance and even longer lifespans than the market-beating materials already on offer.
As the electric vehicle market continues to grow, so too will the importance of effective thermal management. Manufacturers must carefully consider whether their existing thermal spacer solutions are fit for purpose in a changing industry – and whether their existing supply lines can deliver the stability they need. With Mitsubishi Chemical Group, EV trailblazers can rest assured that they have a partner equipped to meet the safety demands of the future. Download the whitepaper on this page to learn more.