Detroit’s Big Three vehicle makers closed the gap with their Japanese competitors in North American factory efficiency during 2002, a key measure of cost controls, according to an annual report released on Wednesday, Reuters said.
Ron Harbour, whose namesake consulting firm conducts the benchmark survey, said despite the improvement, efficient plants still gave Toyota, Honda and Nissan a $US300 to $US400 cost advantage per vehicle over General Motors, Ford and Chrysler.
“The Japanese still have a significant lead here,” Harbour reportedly said in a presentation to the Automotive Press Association. “Nonetheless, the other three are catching up rapidly.”
According to Reuters, the report measures how many labour hours it takes each car maker to build a complete vehicle. Once again, Nissan led all car makers, taking an average of just under 17 hours to assemble a vehicle in 2002, a 6% improvement from a year earlier.
Toyota’s average of 21.8 hours was down slightly, while Honda’s 22.3 hours was worse than last year due to new vehicle launches at most of its factories.
How well do you really know your competitors?
Access the most comprehensive Company Profiles on the market, powered by GlobalData. Save hours of research. Gain competitive edge.
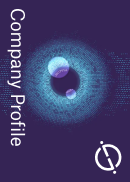
Thank you!
Your download email will arrive shortly
Not ready to buy yet? Download a free sample
We are confident about the unique quality of our Company Profiles. However, we want you to make the most beneficial decision for your business, so we offer a free sample that you can download by submitting the below form
By GlobalDataReuters said GM averaged 24.4 hours, a 6.4% improvement, while Ford averaged 26.1 hours and Chrysler took 28 hours – a 9% improvement, the largest in the study.
Harbour reportedly said the Japanese car makers withheld data for some of their plants, but that had the missing plants been included, the results would be similar.
According to Reuters, the Harbour report has become one of Detroit’s key measures of a vehicle maker’s management skill. With prices of new vehicles falling, incentives rising and profits under ever-present pressure, cost cutting has become a way of life for the car makers.
In addition to the efficiency penalty, the Big Three must also cope with pension and health-care costs for their workers that run $US700 to $800 more per vehicle than the Japanese, Reuters noted.
Offsetting those costs has driven the Big Three to copy many methods – and hire many executives – from Japanese car makers, especially Toyota, to learn how to squeeze the most from their plants.
“The same thing that makes your plants better applies to everything else in your business,” Harbour reportedly said.
According to Reuters, he also said Chrysler’s improvement was notable because all its plants improved, and attributed it to basic “blocking and tackling.”
Reuters said Chrysler manufacturing chief Tom LaSorda vowed that Chrysler would continue to improve by designing its vehicles to be easier to build.
“We expect further improvement this year,” LaSorda told Reuters. “Obviously 5 to 6% is where we need to be, if not more.”