Dana says it has developed a ‘long heat exchanger’ designed to extend battery life in hybrid and electric vehicles.
The technology, it says, is the first of its kind and recently debuted on Tesla Motors’ 2010 all-electric Roadster Sport.
Lithium-ion battery life is dependent on maintaining optimum operating temperature. Dana’s heat-exchange technology cools the Roadster’s battery by transferring heat generated within the battery to the vehicle’s climate-control system.
In addition, a temperature sensor mount provides continuous feedback to the climate-control system. This interface helps to maintain the battery’s ideal temperature during operation, thus helping to extend battery life, Dana says.
“Dana is committed to providing our best-in-class engineering and manufacturing expertise to electric-vehicle manufacturers such as Tesla Motors,” Dana President and CEO Jim Sweetnam said.
How well do you really know your competitors?
Access the most comprehensive Company Profiles on the market, powered by GlobalData. Save hours of research. Gain competitive edge.
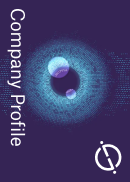
Thank you!
Your download email will arrive shortly
Not ready to buy yet? Download a free sample
We are confident about the unique quality of our Company Profiles. However, we want you to make the most beneficial decision for your business, so we offer a free sample that you can download by submitting the below form
By GlobalData“Our advanced battery technology solutions will help drive our growth in this exciting market segment.”
Dana engineers constructed the heat exchanger using a patented aluminium brazing process, which it says ensures cleanliness of both the climate control and battery coolant fluids. The use of high-strength aluminium alloys provides greater material strength and contributes to weight savings. Additionally, the chiller’s compact design also provides significant space savings – critical for helping engineers accommodate the Roadster’s 6,800-cell battery pack.
“Advanced manufacturing capabilities such as our unique brazing process, combined with our research commitment to the hybrid and electric segment, position Dana as a valued contributor to hybrid-vehicle battery technology,” said Ted Zielinski, director of engineering, Dana Thermal Products Group.
Dana developed and is manufacturing the heat exchanger at its advanced engineering centre in Oakville, Ontario, Canada.
See also: RESEARCH ANALYSIS: Review of advanced battery technologies