Mazda Motor has developed a claimed world-first recycling system which enhances the process it uses to recycle used bumpers into raw plastic resin for use in new vehicle bumpers.
It said the new technology is the first to enable recycling of used bumpers from different manufacturers at the same time. By automating processes to remove metal attachments, it also significantly increases recycling efficiency.
The automaker has recycled bumpers since the early 1990s, initially turning them into underbody trays. The latest recycling technology can recycle all types and makes of bumper, removing the need for separate collection systems for each automaker’s products. It also combines all the recycling stages involved in crushing used bumpers through to reproducing raw materials, into a single automated process.
“These innovations represent a significant step forward for the industry,” Mazda said.
Until now, unwanted materials such as metal attachments had to be removed by hand before the bumpers were visually inspected. Mazda overcame this by developing technologies to automate the processes in collaboration with Satake Corporation, a company in Hiroshima Prefecture, western Japan. Once used bumpers are crushed into pellets, a machine similar to those used to separate contaminants from cereal grains, removes unwanted metal pieces by shaking the pellets and directing airflow over them. This enables higher efficiencies to be achieved.
How well do you really know your competitors?
Access the most comprehensive Company Profiles on the market, powered by GlobalData. Save hours of research. Gain competitive edge.
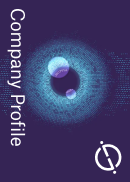
Thank you!
Your download email will arrive shortly
Not ready to buy yet? Download a free sample
We are confident about the unique quality of our Company Profiles. However, we want you to make the most beneficial decision for your business, so we offer a free sample that you can download by submitting the below form
By GlobalDataThe new technology also resolves another limitation of previous methods. Depending on the vehicle manufacturer and age of the vehicle, used bumpers vary considerably in terms of the composition of polypropylene plastic and paint adhesive properties. While this has forced previous systems to treat different bumpers separately, the new technology successfully enables all bumpers to be recycled together. The new process employs a kneading machine which is similar to those used for processing foodstuffs and chemicals such as rubber and plastics. The machine applies a powerful shear force to the crushed bumper pellets, effectively stripping off the paint regardless of the plastic composition or paint properties, and without having to heat the plastic.