Lear Corporation (NYSE: LEA) is the creative force behind thousands of automotive innovations that have earned the company numerous awards and expanded Lear’s backlog of new business to more than $3 billion. By designing from the inside out, Lear can ensure that all components — from overhead storage systems to self-aligning seat head restraints and sophisticated cabin communication systems — work together. The resulting harmonious design is a hallmark of Lear innovation and technology.
Lear is showcasing some of its latest technology innovations at the company’s exhibit at the 2000 Automotive Engineering Exhibition, sponsored by the Society of Automotive Engineers of Japan. These innovations include both products and processes, tapping the creative talents of Lear’s worldwide employees and the tools that help bring those creations to fruition.
The focus of the Lear exhibit is modularity and the benefits that modules offer to automakers and consumers. Lear also is unveiling an impressive range of its new Intertronics(TM) products, Lear’s products and technologies for the global automotive market such as smart junction boxes, advanced electronic products and mechatronic switches, as well as remote keyless entry systems and full electronic and electrical distribution systems.
OASys(TM) Overhead Audio System — Lear’s OASys overhead audio system is revolutionizing automotive audio. OASys uses a network of sound zones in place of large, heavy traditional cone and coil speakers currently positioned in door and instrument panels. This technology transforms the entire headliner into a speaker with excellent ambiance and enveloping sound qualities, logically focusing the sound at occupants’ ears rather than their knees. OASys has multi-channel capability and adaptability, and uses typical audio signal processing. Ducts for heating, air conditioning and ventilation also can be incorporated. OASys provides automotive manufacturers an opportunity to reclaim valuable packaging space in the door and instrument panels, eliminate the noise paths into the vehicle interior and achieve total vehicle weight savings. Lear can deliver OASys fully assembled and pretested, resulting in a reduction in vehicle complexity as well as warranty issues.
Integrated Seat Adjuster Module (ISAM) — This mechatronic product combines the consumer interface control and the multiplexed electronic control for seat adjustment, power lumbar support, memory function and heated seat into one package. ISAM combines several functions into one product to save space and cost, has the design flexibility to include additional features and styles, and reduces time and complexity of assembly into the seat.
Two-Tone, Single-Step Injection Molding — This low-pressure Lear process innovation has the capability to produce a two-tone door in a single step. It provides excellent interfacial bonding without the use of adhesive and can accommodate post-formable flanges and trim edges. The process has the flexibility to produce a door trim panel with a single cover, a split cover combining a soft upper cover with hard lower trim or no covering material at all. Integral molded core features include cages, locators and retainers.
How well do you really know your competitors?
Access the most comprehensive Company Profiles on the market, powered by GlobalData. Save hours of research. Gain competitive edge.
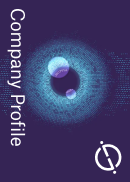
Thank you!
Your download email will arrive shortly
Not ready to buy yet? Download a free sample
We are confident about the unique quality of our Company Profiles. However, we want you to make the most beneficial decision for your business, so we offer a free sample that you can download by submitting the below form
By GlobalDataFabricFoam(TM) Seat Trim — Lear is continually exploring materials innovations in seating systems. Seating is the third largest cost in the production of a vehicle and the largest portion of the seat cost is the seating materials. Lear’s proprietary FabricFoam seat trim eliminates the need for seat covers, which reduces materials, labor and lamination cost. The one-step, low-cost manufacturing process for FabricFoam uses polyurethane foam and durable polyurethane skin to produce a flexible surface finish with dynamic colors, texture and gloss that also meets automakers’ materials specifications and comfort requirements. It can be easily recycled and is both water resistant and washable.
Dual Voltage Smart Power Junction Box — Lear’s Dual Voltage Smart Junction Box is a multifunctional and centralized unit that combines the signal and power for the upcoming dual voltage architecture. The increasing consumer demand for new power functions is driving the need for efficient, high voltage distribution systems in vehicles. The dual voltage architecture maintains the current 12-volt power needed for loads such as the vehicle’s incandescent lamps and small power motors and actuators, while deploying the 42-volt power bus for the new, high power demanding loads such as electro-magnetic valves and electrically heated catalytic converters. The introduction of the two voltage systems increases the efficiency of the whole electronic and electronic distribution system, and optimizes size, weight and cost. The Dual Voltage Smart Junction Box also provides new technical solutions using higher voltages, such as the use of semiconductors optimized for 42 volts that replace conventional electromechanical relays and the integration of the DC/DC converted into the Smart Junction Box.
Integrated Airbag Canister — This Lear innovation integrates the airbag canister with the instrument panel retainer, providing improved fit and finish of the canister and airbag to the instrument panel. The design eliminates the canister end caps, contributing to the reduction in parts, cost and weight. The integrated canister also provides enhanced structural support to the instrument panel.
Integrated Head Impact Countermeasures — Lear’s Pro-tec(TM) Advanced Restraints line of safety products include materials innovations in head impact countermeasures that provide enhanced safety to vehicle occupants. Among the materials on display is an egg-crate-like plastic that provides improved energy absorption.
Sono-tec(TM) AT Dash Insulator and Floor Underpad — Sono-tec AT Dash Insulator and Floor Underpad is part of Lear’s Sono-tec Acoustic Absorbers, Lear’s line of acoustic products. This very lightweight, multi-layer dash insulator and floor underpad was developed and optimized through Lear’s proprietary acoustic modeling capabilities. It provides optimum sound abatement performance by using both absorptive and barrier technology. In addition to being manufactured from recyclable materials, it offers a weight savings of up to 60 percent compared to traditional designs.
Integrated Door Controls — This family of mechatronic products consolidates the controls for window lift, door lock, power mirror, heated seat and electronic control modules into a single, integrated package that operates either direct or via multiplexing to interface with vehicle systems outside the doors. Lear’s integrated door controls lower system cost by reducing wires and assembly of different controls and the modular design allows adaptability to vehicle requirements with minimal changes.
Pro-tec(TM) Self-Aligning Head Restraint System — Lear’s exclusive Pro-tec Self-Aligning Head Restraint System (SAHR) significantly reduces the occupant’s risk of neck injury during a low-speed rear impact. SAHR is part of Pro-tec Occupant Protection Systems, Lear’s line of innovated safety products. It uses a balancing system that allows the acceleration and velocity between the head and the upper torso to be as low as possible. During the early stage of the rear impact, the force of the impact presses the occupant against the seat back, then the head restraint moves up and forward to support the head and minimize the potential for whiplash. SAHR reduces the risk of injury by 80 percent compared to standard seat frames.
Custom Key Fobs — This new generation of remote keyless entry key fob designs uses decorative molding technology to offer a wide variety of options in fob design patterns or colors including textures, logos, text, and translucent and glow-in-the-dark colors. The custom key fobs provide unique styling without changing mold or injection material, offer the proven styling success found in cell phones and pagers to key fobs, and use technology that is adaptable to existing molds with only minimal change.
Electrically Integrated Door Trim System — This Lear innovation integrates the wire harness and electrical components, such as door switches, into the door trim panel, as well as mounting the sound system speaker on the panel. By incorporating all these items into the door trim panel and then installing the electrically integrated door trim system on the vehicle door along with other components reduces complexity at the vehicle assembly plant and provides improved ergonomics during assembly.
People-Vehicle-Interface(TM) Methodology (PVI Method(TM)) — Lear’s exclusive People-Vehicle-Interface Methodology — or PVI Method for short — is the innovation development discipline Lear employs to turn a market opportunity into stylish and functional products that consumers want and need in their vehicles.
Lear’s six pillars of PVI begin with Consumer Research to define consumer preferences based on extensive testing, focus group studies and physical measurements. The second pillar, Industrial Design, interprets consumer data to conceptualize and create unique solutions to meet the demands of tomorrow’s automotive interior components and systems. That is followed by Engineering, where Lear engineers develop new products that meet the needs of both Lear’s customers (automakers) and consumers, focusing on safety, modularity, low mass, comfort and convenience.
The fourth pillar is Technical Analysis in which specialists provide analytical and developmental expertise to assess the performance, longevity and function of each component or system.
The PVI Method’s final two pillars are Manufacturing Process Development and Validation. The former focuses on the evolving manufacturing processes to produce superior components as well as to bring products to market faster. Increased recyclability, while reducing cycle time and costs, also is important. Validation is conducted at Lear’s recently expanded, state-of-the-art testing facility that is part of the Lear Corporation World Headquarters and Technology Center in Southfield, Michigan (USA). There, products are tested and certified to meet the government specifications and the individualized needs and requirements of Lear’s customers.
Lear Corporation, a Fortune 150 company headquartered in Southfield, Michigan (USA), is one of the world’s largest automotive suppliers, with 1999 sales of $12.4 billion. The company’s world-class products are designed, engineered and manufactured by more than 120,000 employees in over 300 facilities located in 33 countries. Information about Lear and its products is available on the Internet at www.lear.com .