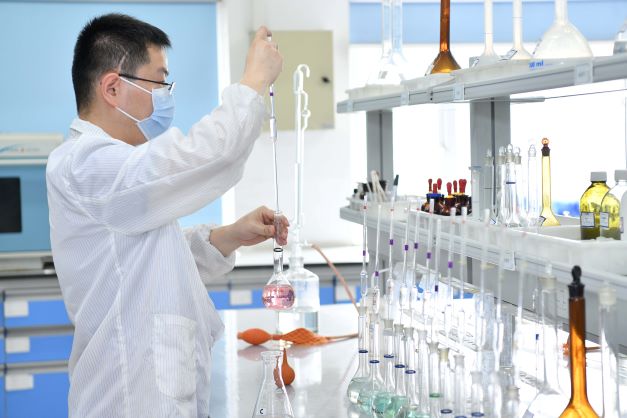
BASF has provided plastics materials and technology to RML Group to develop and produce an “innovative, immersion cooled battery” for an unnamed “high performance hybrid hypercar” claimed to have set new performance and safety standards using the next generation materials.
The 800V battery has capacity of 4.2 kWh and a discharge rate of >100C, and weighs less than 75kg.
The extremely high power output, especially during rapid acceleration and regeneration, required a cooling system capable of rejecting the heat generated by the cells. To prevent extreme temperatures and ensure a more even temperature distribution throughout the pack, immersion cooling was used, which greatly improves the entire battery system’s efficiency and service life.
Two BASF plastics are used in RML’s battery unit.
Ultramid is used for the housing material for the battery unit itself and in the housing of the high voltage electrical components of the battery control system.
BASF claimed its plastic was noted for its “robustness and high resistance to mechanical stressing, which is particularly important for the battery housing”.
How well do you really know your competitors?
Access the most comprehensive Company Profiles on the market, powered by GlobalData. Save hours of research. Gain competitive edge.
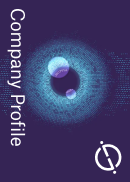
Thank you!
Your download email will arrive shortly
Not ready to buy yet? Download a free sample
We are confident about the unique quality of our Company Profiles. However, we want you to make the most beneficial decision for your business, so we offer a free sample that you can download by submitting the below form
By GlobalDataThe design has to satisfy crash requirements and pass the UNCE Reg 100.03 fuel fire test. Protected only by a thin carbon sheet integrated into the test as a body part, the Ultramid B3EG7 grade passed the fire test without damage to the housing, making it ideal for this application, BASF said.
The Ultramid A3EG6 EQ product was used as the material for the individual battery cell holders within the battery housing. The EQ grades (Electronic Quality) are extremely pure grade and contain hardly any electrically active or corrosion promoting contents and still deliver claimed “outstanding” heat aging resistance.
In contact with dielectric fluid, the material minimises any kind of diffusion out of the material. Since dielectric fluids are used for electrical insulation and as coolants in high voltage applications, contamination by contact materials must be avoided.
RML engineers luxury and racing cars and is also a pioneer of electrification of the automotive fleet through its development, design and production of novel and innovative battery systems.
BASF and RML collaborated from the development stage and had early involvement as a materials supplier in decision making processes.
“RML needed to explore state of the art materials for battery systems to meet the mass and structural targets set by customers for high performance applications. We worked closely in collaboration with BASF to achieve the desired properties,” said powertrain chief James Arkell.
BASF said it was able to “significantly accelerate” the development of the overall battery unit due to its extensive expertise in the new battery sector and in the field of electrical and electronic (E/E) materials.
The rapid recommendation of suitable materials as well as the timely, global delivery of sample quantities were instrumental in ensuring that RML was able to meet its ambitious schedule for this project.
BASF also provides services such as component simulation. Ultrasim can be used to develop components for specific requirements, to create heavy duty, efficient and lightweight customised components.