
How did the work with ZKW come about?
Many of their OEM customers were requesting increasingly complex products, with new features and specifications. As safety-critical parts, developing these new lighting systems required extensive testing and validation. At the same time, their customers were also compressing lead times, so their rate of development needed to increase to maintain a competitive edge. On top of this, headlights are becoming increasingly integrated with ADAS systems, necessitating more complex control systems than ever before. It quickly become clear that leveraging virtual simulation could play an important role in accelerating their development capabilities – simultaneously improving their ability to innovate and deliver to reduced timescales.
What are some of the challenges with lighting development? How is simulation helping to address these?
Currently, it can take millions of euros and up to 18 months to develop a new headlight for automotive applications. A large chunk of this time is spent with engineers testing and evaluating the effectiveness and reliability of the lighting system. This on-road testing is often conducted on public roads at unsociable hours, presenting increased risk to drivers and other road users. It is then further complicated by the fact that headlight technology, and therefore complexity, is advancing rapidly, increasing the development and validation workload accordingly.
That is where simulation can offer enormous benefits in terms of removing the constraints of conventional on-road activities. Through simulation, it is possible to optimise both the hardware design and control software strategy before a prototype vehicle exists, or even before a prototype headlight exists. We are working with the ZKW team by using dynamic, real-time headlight simulation to reduce the requirement for real-world test-driving time by more than fifty per cent. This will provide substantial time, cost and risk benefits to headlight system development, and enable engineers to take a few nights off.
The idea of being able to do this testing in a simulation is impressive, but how realistic can it be? How can such a high level of correlation be achieved with the real world?
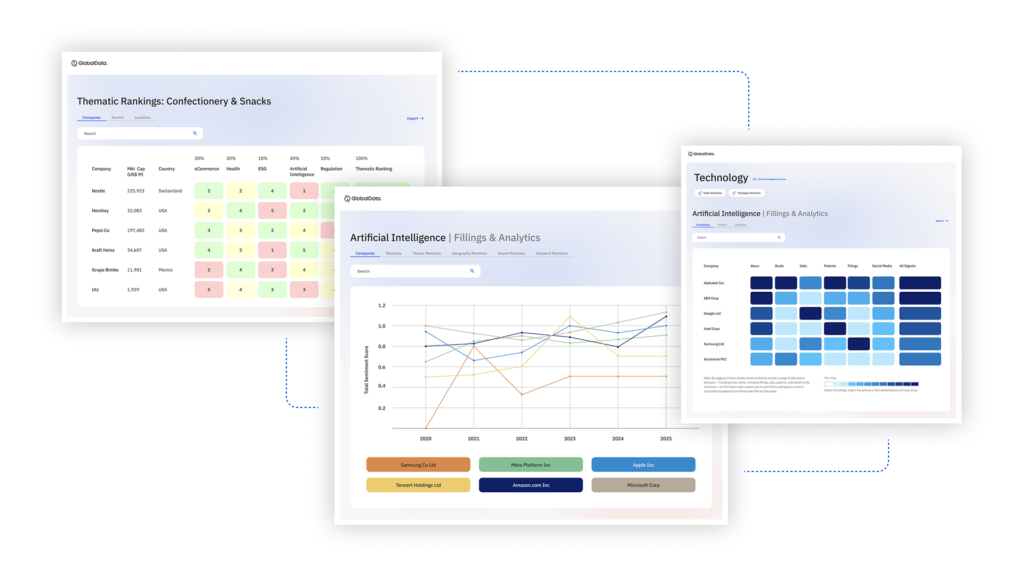
US Tariffs are shifting - will you react or anticipate?
Don’t let policy changes catch you off guard. Stay proactive with real-time data and expert analysis.
By GlobalDataIn a word, extremely – it all comes down to the level of detail. Thanks to high-fidelity road surface modelling, and lighting defined by industry-standard IES and RGB profiles, we have created a uniquely accurate virtual environment. Even things like the dynamic motions of the vehicle in pitch, roll and yaw create a faithful representation of the headlight’s output in the virtual environment. Combine this with vehicle dynamics-grade road surfaces and the customer’s digital vehicle model, and it is possible to accurately replicate the real-world sufficiently enough to carry out meaningful headlight development. This can enable manufacturers to gather actionable and informative data and feedback in the virtual world, long before the first prototype exists.
This is another critical point of how simulation is helping streamline the development process. Tier 1 suppliers have very limited access to the vehicle manufacturer’s prototypes but do have 24/7 access to the virtual vehicle model. So not only can more development be done in advance of gaining access to the vehicle but when the vehicle is available, the work being carried out is much more valuable. For example, multiple headlight profile shapes can be changed and reviewed at the click of a button during a test drive.
Headlights are becoming more complex as they become heavily integrated with ADAS systems, can simulation be used to develop these technologies in tandem?
We are certainly seeing a substantial increase in the popularity of ‘smart’ headlights with more complex functions than traditional units. Indeed, these require integration with other vehicle systems, including ADAS. As simulation advances too, it is now possible to integrate and simulate the variety of vehicle ADAS sensors at the same time. That means that vehicle sensors scanning the road ahead can feed their inputs directly into the smart headlight control system and we can replicate the full-system feedback cycle.
However, to ensure the simulation is effective, the sensors must be fed highly-accurate data. Our simulation is physically accurate and visually detailed, ensuring that engineers can analyse the raw light values and colour banding that the headlights produce to make appropriate design decisions.
Simulation is extensively used by OEMs and Tier 1 suppliers now. Do you think we are approaching the peak of development via simulation?
While simulation has evolved substantially over the past decade and has found extensive use within the automotive industry, I do not think we have reached the peak of virtual development. We are not even close. Working alongside our customers, we are constantly refining or adding features, and finding new applications or areas where we can improve – it is a continuous process.
That being said, we have certainly reached the point where vast quantities of driving time can be substituted with equivalent virtual activity. Not only is it easier, safer and cheaper, but it is also significantly faster as it avoids the constraints of things like prototype availability, weather, road conditions and traffic volume. When we reflect on the advances of the past decade, it highlights the incredible progress that has been made and the scope of exciting possibilities in the decade ahead.