Continuing just-auto’s series of interviews with tier one suppliers of electronic braking systems, Matthew Beecham talked with Dan Milot, Technical Director, Customer Application & Systems Engineering North America, TRW Automotive.
What are the forces driving innovation in electric park brakes (EPB) for passenger cars? And are those drivers the same for every car segment?
Although EPB technology is about ten years old, the drivers for passenger cars are relatively the same, including packaging in the vehicle console area, vehicle assembly enhancements, and advanced stand-still features. The emergency brake lever has been replaced by a switch, we’ve removed a brake cable, and with electronic control we have the capability to drive additional autonomous features. Automakers are reducing the number of platforms while tailoring their vehicles to multiple regions, so there’s an interest in modular technologies.
Once you have an electronically controlled device – such as an EPB actuator and electronic control unit to process sensor inputs – you can add enhanced features. This is especially attractive in the premium segment of vehicles. For example, there is a handoff that occurs between slip control and EPB for hill hold events. There is also interplay between slip control providing hydraulic braking versus the EPB actuator doing the braking while the vehicle is in motion. Again, once you have a device that can be controlled electronically, many additional feature enhancements can be provided.
These benefits are driving innovation in most other car segments as well.
Where do you see the greatest potential for EPB in the next few years?
How well do you really know your competitors?
Access the most comprehensive Company Profiles on the market, powered by GlobalData. Save hours of research. Gain competitive edge.
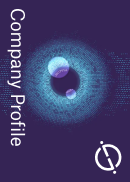
Thank you!
Your download email will arrive shortly
Not ready to buy yet? Download a free sample
We are confident about the unique quality of our Company Profiles. However, we want you to make the most beneficial decision for your business, so we offer a free sample that you can download by submitting the below form
By GlobalDataEPB is taking off in China at a greater rate than initially anticipated. They are actively working to keep pace with what we are doing in Europe and North America.
There is also great potential in North America as the light truck market is focused on weight savings and improved vehicle assembly provided by EPB. Passenger cars in North America with automatic transmission are benefiting from the packaging advantages, as well as weight and cost savings. Overall, the benefits associated with electronics integration and slip control are driving demand.
Could you update us on the stage of development TRW is at with its EPB and development aims?
Well, after ten years, we now are into our 5th generation of EPB for passenger cars. The biggest advancements involve the integration of electronics, which had previously been in a separate box and are being imported into the electronic stability control (ESC) system.
Looking ahead, we see a lot of growth opportunities in the light truck market.
As demand for powertrains with energy recovery systems increases, the electronic integration of systems that help the driver better control the vehicle is clearly desirable. As we understand it, among the strategies that TRW employs is the integration of the ESC and the EPB – referred to as EPBi. I guess we can expect to see more examples of system integration in the braking arena, possibly EPB and brake-by-wire?
TRW has integrated ESC and EPB, resulting in the new technology we’re calling EPBi – “integrated EPB” – in order to reduce electronics costs across the total braking system. The drive for integration was not associated with the powertrain enhancements with energy recovery systems.
We are still providing the same function, the same driver interface with the switch and the same actuators at the rear brakes – but there is no specific interaction with a unique powertrain. There may be certain transmissions with different types of electric shift-type mechanisms [that] may use EPB to hold a vehicle for a certain amount of time on a hill and then let it go, for example. In general we haven’t developed our system specific to a powertrain. Some energy recovery systems do create some interesting challenges at stand-still for which EPB is a device that can assist in enabling the vehicle to hold at rest better.
There are additional integrations in the braking arena through our integrated brake control (IBC) technology, which integrates actuation and ESC.
Could you update us on the stage of development TRW is at with brake-by-wire and how you will push back the technical boundaries?
Brake-by-wire in this context is going to be assumed as a “dry” system because it uses an electric actuator to push a mechanical plunger that squeezes the brakes – but there is no hydraulic fluid involved. This is in contrast to an electro-hydraulic solution, which can also be considered “brake-by-wire” to some. EPB can perform an emergency/park brake function, but it is not intended to be used as primary braking source. The technology for brake-by-wire is similar but requires higher voltage, more dynamic response and higher durability requirements.
Vehicle architectures are still primarily based on 12 volt architectures. Some electric/hybrid-electric vehicles today have much higher voltage systems as part of the overall powertrain propulsion system. This electrical architecture present on the vehicle has not been tapped to also source the brake system directly. Given the proper vehicle electrical architecture, cost effective implementation of a motor driven caliper, and measurable enhancement to end consumer, brake-by-wire will happen. Until then we continue to drive optimisation into the systems we have today, EPB and soon to be IBC.
Some say that while hydro-electric and electromechanical brake systems are potentially safer than conventional braking systems – due to the potential for greater integration with ABS and ESC – safety concerns have held them back. What’s your view?
Hydro-electric and electromechanical braking systems have moved away from traditional vacuum-based boosters to something that’s more electrified – incorporating electric motors driving plungers, and many more sensors. So technology now has to measure what the driver is doing and then electrically apply the brakes. So I think the safety concerns are based on the fact that these systems have more opportunities for failures, which means you could potentially have push-through mode more often. Is this true? Not necessarily. So it’s important to put appropriate diagnostics and reversionary modes in place to make the system work.
When any new technology replaces a convention system that has been around many years, the new system needs to mature to a level where there’s confidence in how it’s going to operate in the field. It most certainly requires a higher level of sophistication in safety analysis and software implementation, but it is definitely achievable.
Although brake reliability is clearly a concern, noisy brakes tend to be another reason consumers bring their cars to the dealership. So if brake-by-wire could virtually eliminate these complaints, improve reliability and thereby cut warranty costs then this would be a possible advantage for customer and consumer alike. What is your view?
Brake-by-wire technology is not going to eliminate noisy brakes. Brake-by-wire using an electro-mechanical device on the caliper functions using the caliper with pads to clamp to a rotor that is moving, so the opportunity for noise is always there. The only way to reduce noisy brakes is to utilise a completely different mechanism for stopping the vehicle, such as electric motors acting as generators at each of wheels. The other method is to continue to focus on the conventional caliper/rotor technology to make it robust to the generation noise.
I guess that the size and bandwidth of car platforms these days are so high that a single electronic brake system is not cost-effective. How do you set about addressing that? i.e. is it about developing a modular and scalable brake system that combines the advantages of a best fitting technical solution for the special need of the OEM in each platform cluster with the volume effects for common subsystems and small application costs for the variants?
There is not a single unit that can cover the full span of vehicles from A-segment to a light truck. The size of brakes required are so different, therefore, you cannot create a “one size fits all” arrangement. However, you can segment – for example, by small car, medium car and light truck.
So creating a modular approach is key to making it work. The further we can expand one given technology across a broader range of vehicles, the easier it will be for the OEMs. They will be able to take that one product and apply it to many vehicles all at the same time, rather than unique solutions for each vehicle segment.
Reducing stopping distances and weight reduction will always be a priority when it comes to design and development of braking systems, yet to what extent is improving the brake feel important to customers?
The remainder of this interview is available on just-auto’s QUBE research service