TMD Friction is a major manufacturer of brake products for the automotive industry, producing one million brake friction products per day. Matthew Beecham talked with TMD Friction’s Director Strategic Planning & Marketing OE, Dirk Brieke about trends in the brake friction market, its copper-free high performance brake pads and CV-Light Plate for commercial vehicles.
TMD Friction recently relocated production from a site in Leverkusen to Essen. What has this move meant for the company?
TMD Friction will consolidate its OE passenger car production volumes for the European market by the end of 2017. It is a large investment of EUR 53m to create the most modern production facility and technology in combination with lean manufacturing processes. Customers will enjoy highest quality and increased value through a complete product portfolio. Products will fulfil latest requirements such as copper free and will be produced by the most modern manufacturing technologies. Customers will also enjoy highest quality in terms of services and will be met with a more flexible approach toward future market demands and opportunity for further growth potential.
The consolidation of the Leverkusen production site and all its employees will retain the engineering and manufacturing know-how for the benefit of the company and its customers. At the same time it will allow for a swift transition from development process to series production. Maintaining the people and skills is pivotal to ensure best practice processes, highest quality and process contingency.
In the future the new lead plant for OE passenger cars in Essen will develop, test and implement latest manufacturing technology and processes. Where applicable these will be applied to other TMD Friction OE Passenger Car plants to support our global customers in regions other than Europe. TMD Friction will thus maintain and strengthen its global competitiveness.
Could you tell us some of your latest advances in friction material and the unique features of each?
How well do you really know your competitors?
Access the most comprehensive Company Profiles on the market, powered by GlobalData. Save hours of research. Gain competitive edge.
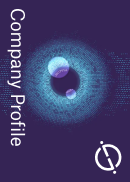
Thank you!
Your download email will arrive shortly
Not ready to buy yet? Download a free sample
We are confident about the unique quality of our Company Profiles. However, we want you to make the most beneficial decision for your business, so we offer a free sample that you can download by submitting the below form
By GlobalDataWith regards to global mega trends weight reduction in vehicles gains more and more importance. The CV-Light Plate for commercial vehicles is a ground breaking new product offering a total weight-saving potential of up to 7.5 kilograms per vehicle (combination of truck and trailer). The approximate saving for fleets can be calculated using the TMD Friction fleet calculator endorsed by the TMD Friction commercial vehicle brand Don.
Advantages are reduced component wear on the axle and brake system due to the reduced “unsprung mass” and reduced CO2 emissions. Alternatively a higher payload can be achieved. This can help fleets to achieve a competitive advantage in an industry that is operating at challenging margins.
Pioneering the development and advancement of environmentally friendly products TMD Friction can look at an extensive track record of innovations. One recent example is the first homologation for a copper-free high performance brake pad used in series production, which was developed in close cooperation with a German premium car manufacturer.
Also for commercial cehicle applications a copper reduced friction material was successfully introduced to series production in the beginning of 2014.
The challenge in copper-free materials is finding an adequate replacement for copper with its positive physical and chemical characteristics. Potential substances like gold, silver, aluminium, nickel or lead are out of question either for cost or toxicological reasons.
The copper-free OE material makes no concessions regarding comfort or safety. At the same time it is ahead of its time, as it is already complying with the new legislation requirements of the US state Washington for the year 2021.
I guess reducing stopping distances and weight reduction will always be a priority when it comes to design and development of friction parts, yet to what extent is improving the brake feel important to your customers?
Brake feel continues to gain importance, especially with regards to changing noise levels through the electrification of drivetrains. Hybrid and electric vehicles show a reduced noise level, revealing other sources of noise in the vehicle. Early on TMD Friction has anticipated that development, offering a comprehensive product portfolio. Noise, together with vibration, harshness and pedal feel does not allow any compromise from a customer perspective. Brake feel will remain a constant challenge to the industry, as vehicles will continue to get quieter.
In what ways has the use of electronic control affected braking hardware?
The remainder of this interview is available on just-auto’s QUBE Global light vehicle OE foundation braking market- forecasts to 2030