For some time, manufacturers have been pushing back the technical boundaries of batteries used for electric vehicles. In this interview, Matthew Beecham talked with Dr Joachim Fetzer, executive vice president, SB LiMotive about a range of issues, including the development cost of battery packs and the company’s plans in increase cell production capacity by 2015.
just-auto: Last year’s stimulus package committed the US government to spending billions for batteries for electric cars. Do you think that the new manufacturing capacity could exceed demand for electric vehicles and plug-in hybrids?
Joachim Fetzer: It is not easy to foresee how the market will develop over the coming years, since many factors play a role. By 2015, SB LiMotive intends to boost its annual cell production capacity to a good four gigawatt-hours – enough for some 180,000 electric vehicles. We see that quantity as realistic for SB LiMotive. We assume that supply and demand will balance out in the medium term, allowing for market consolidation.
Some people believe that the emerging EV and PHEV markets could flatten out due to unproven technology. They reckon that the market will be initially bolstered by heavy subsidies to automakers, battery makers, and consumers, but that sustained growth will depend on yet-to-be-proven battery technology as well as on supporting government policies. Would you agree?
Market growth is influenced by many factors besides technology, such as business models, infrastructure, etc. When it comes to technology, SB LiMotive has already started manufacturing cells for pre-series projects. The cells are based on state-of-the-art technology and fulfil today’s automotive requirements. Based on our results so far at SB LiMotive, we are very optimistic that we will be able to master the technical challenges of series production, with the help of our parent companies and their long years of experience.
I guess that the stubbornly high cost of battery packs – which can account for about half the cost of an electric vehicle – is a hurdle. Presumably, the costs need to be reduced to below 400 dollars a kilowatt hour to make it commercially attractive. If the cost of battery packs can be significantly reduced, where will the cost reduction come from?
How well do you really know your competitors?
Access the most comprehensive Company Profiles on the market, powered by GlobalData. Save hours of research. Gain competitive edge.
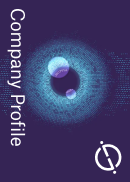
Thank you!
Your download email will arrive shortly
Not ready to buy yet? Download a free sample
We are confident about the unique quality of our Company Profiles. However, we want you to make the most beneficial decision for your business, so we offer a free sample that you can download by submitting the below form
By GlobalDataFor electric vehicles, large batteries with high energy capacity are needed. In other words, it takes many cells to achieve an adequate range: a journey of 200 kilometres in an electric vehicle weighing 1,000 kilograms requires a battery supplying some 35 kilowatt hours. Today, this kind of battery costs roughly €500 per kilowatt hour – so for 35 kilowatt hours, the battery would cost some €17,000. To reduce the price, it is necessary to decrease the number of cells. This can be done by considerably increasing the specific power or specific energy of the materials in each cell to make the battery lighter and less expensive.
More importantly, we can utilize economies of scale in manufacturing. Here we can also apply lessons learned by our parent companies to further reduce cost. As their experience in the mass production of complex products has shown, producing ten times more units reduces relative manufacturing cost by three-quarters. This principle can be applied to the batteries that we will manufacture in the future. Here too, the law of large numbers applies.
Additionally, the considerable investments made in engineering and manufacturing must also be made to stretch over the largest possible quantities. This allows development cost for each battery sold to be reduced, as shown by a comparison of two manufacturers with annual sales of 500,000 and 50,000 units respectively. Compared with the smaller manufacturer, the larger manufacturer saves some EUR500 in development cost per unit. Plus, batteries will become more affordable as production of chemical raw materials becomes cheaper, procurement volumes of raw materials become larger, and components become increasingly standardized. The general consensus is that we will be able to produce a battery pack for roughly EUR350 per kilowatt hour by 2015. This would mean that the batteries for the electric vehicle I mentioned earlier would cost roughly €12,000.
Whichever way you look at it, EVs remain expensive and give motorists range anxiety with just 100 miles between charges. What needs to happen to EV batteries to improve this situation?
Electric vehicles need batteries that have a high energy density, since a great amount of energy needs to be stored in the battery for the vehicle to travel long distances. Range, which depends in large part on the energy density of the battery cell, is a factor that is crucial to the success of electric vehicles. Currently, a state-of-the art lithium-ion battery for a vehicle with a range of 100 to 150 kilometres would be the size of the trunk of a VW Golf. In other words, a battery with 35 kilowatt-hours of capacity would have a volume of roughly 350 litre and a mass of some 350 kilograms.
Customers are demanding a range of 200 kilometres. To meet their demands, engineers are looking to increase energy density. In raising energy and power density, the focus is on improving the chemicals used in the cells. Improvements in energy density will also make it possible to reduce the weight and size of lithium-ion batteries. Both aspects, reducing battery weight and improving energy density, will help to extend the range of EVs.
NiMH batteries are said to be not an ideal energy-storage device for hybrid cars. Their limitations include moderate energy conversion efficiency, which translates to some energy loss and significant heat production in normal usage, reduced life with high depth-of-discharge cycling, and unsatisfactory performance at high and low temperatures. Given these limitations, how do you see its application for future hybrid and electric cars?
Today, hybrid vehicles still use nickel-metal hydride batteries. However, there is a general consensus that the development potential of these batteries has been exhausted. In contrast, lithium-ion technology appears much more promising in the medium to long term. This conclusion is based on a series of advantages offered by lithium-ion technology. For instance, compared with nickel-metal hydride cells, lithium-ion cells have a significantly better power density. Furthermore, due to their high nominal voltage, they also have a higher energy density.
Other advantages include their higher cycle durability and longer calendar life, as well as their significantly lower self-discharge rate. In other words, if you are away on vacation and don’t use your electric car, the battery will barely discharge. Moreover, lithium-ion technology already has a proven track record in consumer electronics: lithium-ion rechargeable batteries supply power to mobile phones, laptops, and Bosch power tools. These properties have made lithium-ion technology the technology of choice for future electric powertrains.
Of course, batteries have to satisfy far higher standards in automobiles than in consumer electronics. Hence, our engineers face tough challenges in refining lithium-ion technology.
While the lithium-ion batteries have their merits, if the plug-in battery vehicle contains a lithium-ion battery, which is to be given a full charge every night in a residential garage, is there not a more serious concern about hazardous failure than with the smaller batteries of conventional HEVs, which are always kept at an intermediate state of charge?
SB LiMotive batteries, regardless of the kind of vehicle they are integrated into, are safe under all operating conditions, including charging. We combine innovative safety features in our battery system, protecting it against internal and external damage. One crucial component is the battery management system, which prevents overcharging and deep discharging. It guarantees a safe and reliable function of cells and the battery system. Current, voltage, temperature, insulation resistance, and other variables for the cells and pack are monitored and managed by the battery management system.