Continuing just-auto’s series of interviews with major vehicle seat manufacturers, Matthew Beecham talked with Jeffrey Lindberg, Senior Product and Business Development Manager, Johnson Controls Inc and Johan Vissers, Design Manager, Johnson Controls Inc about seat designs, consumer tastes and methods to produces seats using green materials and processes.
Over the years, new materials and techniques have improved vehicle occupant comfort and wear resistance while reducing weight and cost. Yet what recent safety related developments has JCI introduced?
Jeffrey Lindberg: During our 2010 interview we mentioned our riACT portfolio of anti-whiplash active head restraints and that the European New Car Assessment Programme (Euro NCAP) had evaluated a seat with riACT as the highest performing seat in the whiplash assessment test with a score of 3.7 out of a possible 4 points. Since then Euro NCAP has evaluated dozens more seats, and that same seat with riACT still holds the top spot in the whiplash assessment. Since then, we have launched more programmes with riACT and every seat evaluated by Euro NCAP has achieved the top category of “good”.
Additionally, when we last spoke we discussed the global consumer research we conducted on head restraints and said that we would use the study findings to influence our new product development activities in order to bring consumer-accepted products to market, especially to satisfy consumer desires for adjustability, comfort, and safety. We’ve made good on that commitment and are launching a variety of head restraints worldwide with integrated adjustments especially for horizontal – i.e. forward/backward – adjustability. The new Ford B-MAX in Europe is one of the first programmes to feature this fore/aft locking adjustable head restraint. The B-MAX seat received 3.2 points in Euro NCAP’s whiplash assessment achieving the top category of “good”. Further programmes featuring head restraints with integrated adjustments will launch soon in China, Europe, and North America. To help make adjustability even easier, we are extending our portfolio to include power head restraints that have both vertical and horizontal adjustments fully integrated.
The new Ford B-MAX seat is also an example of a recent All Belts To Seat (ABTS) programme. The seat has an integrated seat belt capable of holding all crash loads. The vehicle does not have the traditional B-pillar, where seat belts are typically mounted, so having an ABTS seat was a design enabler for the OEM. When the rear sliding door and front door of the vehicle are open, one receives a very open and spacious view into the vehicle interior.
We continue to integrate restraint systems into our seats and ensure their performance in the design and test phases as well as in the manufacturing process. Examples include: integrated seat belts, side airbags, occupant detection systems, airbag control, seat belt reminder systems, and child booster seats. More recently we’ve begun to integrate supplied haptic feedback systems into our seats for various OEM’s Lane Warning Departure Systems. When a driver deviates from his or her lane, the seat vibrates to alert the driver. The new Cadillac ATS seat we supply to GM features this system.
How well do you really know your competitors?
Access the most comprehensive Company Profiles on the market, powered by GlobalData. Save hours of research. Gain competitive edge.
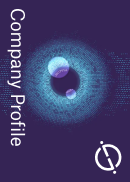
Thank you!
Your download email will arrive shortly
Not ready to buy yet? Download a free sample
We are confident about the unique quality of our Company Profiles. However, we want you to make the most beneficial decision for your business, so we offer a free sample that you can download by submitting the below form
By GlobalDataAlthough we do not make child seats, we continue to design and develop top tethers and lower ISOFIX anchors ensuring compliance to safety regulations to more easily and safely install child seats in vehicles. Recent studies have indicated that consumers are having difficulty installing child seats using the ISOFIX system, so we are working with our OEM customers to offer solutions on current and future programmes e.g. special trim solutions. Additionally, we offer a number of rear seat flexibility programmes that allow child seats in the second row of three row vehicles to remain installed while still providing easy access to the third row of seats.
People come in all shapes and sizes. Yet I guess seat designers must take their disparate concerns for comfort and somehow integrate them into the vehicle seat whether it be for a high-end or small car. How do you approach designing a seat for a certain new model? What are the considerations?
Johan Vissers: For every new model we take four key information blocks into consideration:
- Consumers: Which target groups will be the buyers of the new car? What are their characteristics and specific needs and expectations?
- Competition: What is the competition offering today in terms of features, comfort, materials and craftsmanship / perceived quality?
- The OEM client: What does the OEM client intend to achieve with the seat to differentiate themselves, in terms of features, comfort, materials, craftsmanship and of course design identity? And what is the accepted cost level?
- Technology: Which technologies (structures, foam, trim, decoration and feature elements) should be used to achieve the expectations?
The resulting seat design is a balanced harmony of the above four aspects.
In every target group, be it small car or high-end, there are people with all shapes and sizes. Therefore, in general, every seat is ergonomically a compromise between the comfort dimensions suited for small women and those suited for large men.
For the economical small car, one can take the ‘take rate’ into consideration, e.g. what percentage of the buyers of this car are women within a certain age group? That will give the development team some indication which dimensions spectrum should have the highest priority.
In higher-end vehicles there is usually more possible in terms of adjustability of the seat, e.g. seat cushion length or backrest side bolster width. These adjustments make it possible to better tailor the dimensions of the seat to the dimensions of different drivers.
I guess these days there is far more collaboration between seat engineers and vehicle designers in order to better match comfort and brand characteristics with certain new vehicle models. Is that correct? To what extent do they design in the preferences of target demographics?
Johan Vissers & Jeffrey Lindberg: Yes, it is correct that there is far more collaboration between seat engineers and vehicle designers. Johnson Controls makes use of a specific set of CAD software to keep a continuous, almost ‘real-time’ input and feedback contact with the Design and Engineering Teams of the OEM client. This results in shorter development cycles, higher production feasibility, more cost control and a seat design much closer to the original design intent by the OEM designers. With this co-operation setup, Johnson Controls is very well able to follow the directions of our OEM customer, with regard to answering to preferences of certain target demographics. Of course, the Johnson Controls team will always give feedback on these directions regarding production feasibility and craftsmanship quality.
Johnson Controls utilises close collaboration between engineering, design, advanced development, and testing in product development. Comfort testing is performed in our ComfortLab and the Human Factors (HF) Labs at global locations. In the HF Labs, all facets of comfort are investigated, starting with visual comfort (how someone perceives the comfort of a seat just by looking at it), including static pressure distributions in the seat interface as well as the effect of seat kinematics on occupants. A silver age database, which shows the effects of age on the interaction between occupant and vehicle, is available, and we are working on growing our internal test subject database including body measures, individual preferences and product experience. Test subjects of specific demographic characteristics can be selected from this database to perform comfort clinics on targeted specific seat systems. Lastly, in the product validation and evaluation stages of programme development we perform simulated crash tests in our sled lab facilities on three continents. This crash testing is performed with Anthropomorphic Test Devices (ATDs), more commonly referred to as crash test dummies, representing 5th percentile females, and 50th and 95th percentile males.
While the focus has, for some time, been on improving the front seats, to what extent are your customers turning their attention on the second and third row seats? What are the considerations there in seat design?
Jeffrey Lindberg: More and more attention is being given to second and third row seats, and we see evidence that OEMs are willing to invest in flexible, innovative seating systems. We continue to provide industry-leading rear seat flexibility solutions that provide maximum re-configurability, comfort, space, and ease of use. We deliver rear seats with comfort adjustments where the seat is capable of adjusting fore/aft and recline. We provide exceptional ingress / egress solutions for accessing the third row. Fold-and-dive flat seating is also gaining popularity, where we deliver full-flat load floors for carrying cargo without the difficulty to remove and store seats. A recent example of a new European programme is the Opel Zafira Tourer where the second row is comprised of three individual seats. When the centre seat is not being used, occupants can easily transform the three middle row seats into two captain’s chairs and a generous armrest, offering unprecedented levels of shoulder and legroom.
Over the last decade or so, we’ve seen a number of low-volume models all scrambling for market share by adding content and complexity of options to their interiors, especially seating. In this scenario, I guess standardization of seat parts such as seat mechanisms becomes critical? How have you addressed that?
Jeffrey Lindberg: Our Core Product Portfolio (CPP) offers interchangeability of components – especially for front seat structures. Through CPP we utilize standardized development and design principles to offer modular designs that fit several requirement profiles with ability to reuse several types of standard components. Our OEM customers can still specify components customized for its specific demands like installation space, functionality and strength.
The flexibility of integrating mechanisms, including components from other suppliers, is also included in our modular concept. Specific to seat mechanisms, through recent acquisitions Johnson Controls also increased its vertical integration through former externally supplied mechanisms, e.g. KEIPER and CRH. One result of this integration is our Synergy Structure which incorporates CRH tracks, KEIPER recliners, and structural components and mechanical height adjusters from Johnson Controls.
We are hearing more and more about the use of soy-based seats these days. What is JCI doing in this respect and how do you manage the supply of soy beans in seat manufacturer worldwide?
Jeffrey Lindberg: Sustainability is important to our company, our customers, and to our consumers, which is why we are continuously investigating ways to produce products with green materials and processes.
We use Natural Oil Polyols (NOPs) in the production of our polyurethane foam products, and are currently providing foam with organic content to more than one million vehicles per year across multiple customer brands. We use local NOPs close to our production locations. Soy is a good example of an NOP ingredient found in North America, whereas Castor is used in Europe, and Palm oil used in Asia. Natural Oil Polyols come from renewable sources that are by-products of animal feedstocks and therefore do not negatively impact food stocks.
In comparison to traditional foam parts, this bio-content foam:
- meets OEM specifications with equivalent product performance
- has a reduced CO2 footprint
- helps preserve oil resources
In addition to NOPs, we offer a renewable natural fibre polyurethane foam alternative called FaserTec – currently producing millions of sets per year for multiple OEMs and vehicles. FaserTec is made from coconut fibres and can also be used as a carrier for other products integrated into the seat, for example massage mats, air ducts, and cooling fans. FaserTec can also reduce seat thickness up to 15mm and has excellent air flow and moisture-absorption characteristics that optimize the thermal micro-climate between the passenger and seat thus ensuring outstanding comfort.
In terms of the appearance of vehicle seating, it appears that these days trendy fabric for a seat insert in certain vehicles is more acceptable than it was, say, a few years ago. But I guess while trendy fabric has its place on some vehicles, it doesn’t suit all. Would you agree?
The remainder of this interview is available on just-auto’s QUBE research service