Intier Automotive Seating is a business unit of Magna International. This business develops and manufactures complete seating systems and sealing mechanisms for the automotive industry. Matthew Beecham talked with Imtiyaz Syed, vice president, engineering and Randy Koenigsknecht, vice president, sales and marketing, Intier Automotive Seating.
just-auto: In what ways have seating designs changed over the past ten years?
Imtiyaz Syed: There have been a number of influences, including changes in demographics, impact of globalization, fuel prices, raw material prices, environmental issues and ever more stringent vehicle safety regulations. At the same time, consumer tastes have changed significantly over the past decade. Consumers want greater comfort and convenience. That means, for example, more power content in the front and rear seats. Weight minimisation driven by efficiency has led to use of alternative and advanced materials in designing seats. Space creation inside the vehicle interiors has become very critical with the explosion of added content and features. Discerning consumer tastes also means consumer want more flexible living space within their cars.
There is, of course, a lot of segmentation that has taken place over the last few years in the automotive industry. Beyond that, within each segment there is a lot of fragmentation that has occurred. We are seeing multiple models in the same market segment resulting in a number of low-volume models. Each model tries to compete by adding content and complexity of optional equipment. In these circumstances, standardization of components — such as seat structures — has become a critical issue. Given that the internal guts of the vehicle seat are invisible to the consumer, we use standard, modular and flexible seat designs allowing us to leverage the seat design and yet use the same parts. That helps bring costs down.
Randy Koenigsknecht: Those seat designs are modular to allow our customer to easily add or delete a variety of comfort and convenience features. In addition, it is scaleable from a manufacturing standpoint so that in high volume production, you can laser weld the construction — and for low volume, it can be spot welded — to help keep costs down. In terms of the evolution of safety in seating, we went from seat belts to pyrotechnic pretensioners, load limiters, integrated side airbags, occupant detection systems and now active head restraints. So our modular design has to be able to adapt and accommodate all of those features from a number of different suppliers. So from a comfort feature standpoint, we are accommodating manual systems, power systems, lumbar and massage systems, heated and cooled systems, etc. When Imtiyaz and his team set out in the task of designing a core structure, not only did they have to look at all of those variables and the global mandates for safety and regulation but also the cost- and weight-competitiveness.
Imtiyaz Syed: When developing the structure for the front seats, we do not have a particular OEM or market in mind. That means we have to look at all the technical specifications of all OEMs that we think will be our customer and the government regulations of each of the countries so that when we design our core structure then it really is a family of core structures that are also scaleable from a performance standpoint. That process results in a design scheme covering all global specifications and manufacturing locations. Our designs are also flexible in terms of dimensions so that you can fit the same structure in a range of vehicles by using overlapping parts. We are starting to develop similar concepts for the rear seats. That is even more challenging considering the sheer complexity of articulations that are inherent in rear seats.
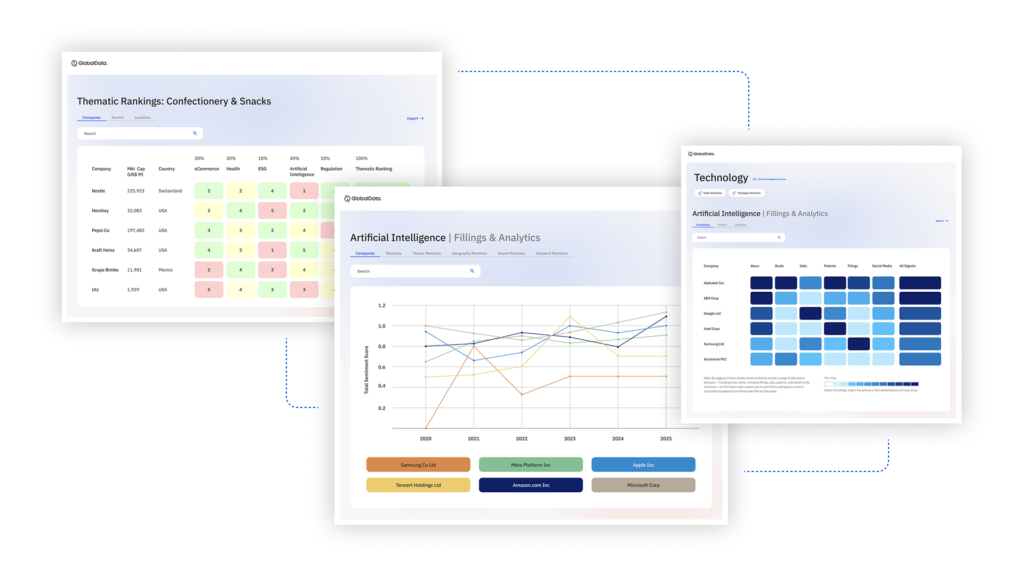
US Tariffs are shifting - will you react or anticipate?
Don’t let policy changes catch you off guard. Stay proactive with real-time data and expert analysis.
By GlobalDatajust-auto: How does your approach to design front seats differ for rear seats?
Imtiyaz Syed: Rear seats have been mostly impacted by the desire to have seat flexibility as well as ingress and egress considerations. Consumers also want their rear seats to be as comfortable as the front seats. That is particularly appealing to Chinese consumers since they tend to use rear seats more than their Western counterparts. So from a complexity perspective, rear seats are far more of a challenge to design. In a complex situation like that, the best approach is a common component strategy rather than a common system strategy which gives modularity, flexibility and scalability of the structure. That approach would then become very important because you could convert one type of seat into another by simply adding and deleting components and mechanisms. So that is the next frontier in terms of standardization and communization. We are already well down the line in terms of developing an approach that is best in class for the rear seats. However, we are not alone in this arena. A lot of seat manufacturers are looking at rear seat structure standardization.
just-auto: Could you contrast the specification for seats in China and Europe?
Imtiyaz Syed: European specifications have generally been more stringent in the past. However, North America has mostly caught up with those specifications. In terms of the emerging markets, they are following either the US or European standards. For example, India and China are currently leaning toward European standards. So I think that in the future there will eventually be consistency [in terms of specifications] but today, there are different levels of specification. Those are, however, government regulations that deal with safety only. But in terms of durability and other specifications then those depend on individual customer requirements. So we have to look at all those specifications and come up with a structure that meets all of them and yet offer a cost-effective solution.
just-auto: You mentioned back then about powered rear as well as front seats…
Imtiyaz Syed: Power is definitely coming to the rear seats as well. For example, rear seat heating systems are fairly common in premium cars. There is also powered stow systems in the third row whereby just pressing a button, the whole articulation takes places so that the seat folds and stows into the floor automatically. We have also developed the ability to power removable seats. With our design, the seat is automatically connected and powered when installed in the vehicle and disconnected when removed without the consumer having to [physically] disconnect the seat before removing it.
Randy Koenigsknecht: That is in production on the Chrysler minivan Swivel Seats. We had to make it very robust and almost invisible to the customer so that they do not even realize that the connection/disconnection is being made and, of course, they do not experience any error in that connection.
Imtiyaz Syed: But it doesn’t stop there. The Lincoln MKX and Ford Edge feature powered seat back fold down on their rear seats. I think that the power growth trend for the rear seat will continue for some time to come.
just-auto: Intier and the Woodbridge Group are set to supply a bio-based polyurethane foam to Ford for the seats in the 2009 model year Ford Escape. Could you talk us through that partnership and your reasons for using BioFoam?
Imtiyaz Syed: The typical foam [used in seating] is polyurethane foam and the polyols are derived from petrochemical products. So we are trying to replace the petrol-based polyols with soy-based polyols. These are natural polyols that can be used in cushion pads and back pads which give the same mechanical properties as a polyurethane. So it is transparent to the consumer. Although we only use a small percentage of soy-based polyols to petrochemical polyols, as the industry evolves then that will increase the content of the natural oil polyols. Also, with fuel prices increasing, it is becoming more and more affordable to have a higher percentage of soy-based polyols in the seat back. We have only just scratched the surface. The soy-based polyols and other natural polyols could end up enhancing the properties of the solution, not degrading it.
just-auto: What is new in seating materials and fabrics?
Imtiyaz Syed: From a metals perspective, we started using an extruded aluminum frame (e.g. Chrysler Pacifica seats). From there we evolved to using die-cast magnesium frames (e.g. second row swivel and third row power seats of the Chrysler minivan). We are now developing seat frames using injection-molded magnesium. We have a Magna company (G-Mag) that specializes in making injection molded magnesium parts. This process is very different from the die cast process. A typical die cast magnesium part has a lot of porosity and brittleness and as a result, you tend to over-design die cast magnesium parts. The molded magnesium parts are less porous and more ductile. Also, it allows for tight tolerances and insert molding of other metallic parts which is a great advantage. You can insert mold steel bushings and other metal parts the same way you would insert mold plastics.
On the other hand, the steels themselves have evolved from typical high-strength steels to what we now call advanced high strength steels or ultra high strength steels that are twice the strength of conventional steel. These advanced steels have evolved in the sense that there are multiple suppliers producing it. Of course, you still have to work with the steel and your specific product to come up with the optimization of the steels.
As far as fabrics are concerned, we have focused more on the process side in terms of how we integrate the trim cover with foam. We were the leaders in pour-in-place technology. We have used this process for many years. It has received great acceptance from the market. We have now advanced that process further which allows us to use multiple materials. By using a single tool, it gives us the ability to produce vastly different seat moulds.
Randy Koenigsknecht: We also have membrane seats which further allow us to be ‘green’ by using less polyurethane foam. It also provides some natural ventilation for added comfort.
just-auto: Where does Intier sit today regarding technologies to meet the occupant head restraints (FMVS 202A) requirement?
Imtiyaz Syed: In terms of the market place, active head restraints are becoming very popular. Intier has its own, cost-effective active head restraint design. However, active head restraints are not necessary to create a seat that meets FMVS 202A or to achieve the good results for the IIHS testing. Fundamentally, seat structures can be designed in a manner that has controlled deformation. In other words, you can achieve the FMVS 202A as well as IIHS good rating without having to put in active head restraints.
One of the issues for the industry is that both regulations require the head rest to be placed closer to the occupant. But when you do that, there may be a real or perceived problem of discomfort for the occupant. This is really an issue for small occupants such as 5th percentile females. That is because a typical small occupant tries to keep the seat back in the erect position so that they adjust the seatback to a full forward position or as far forward as possible. But when you do that, for every degree of recliner moment forward, they are losing about 5 – 6mm in terms of the distance between their head and the surface of the headrest. So this is a real issue. However, we have developed a way to avoid that discomfort and meet the government regulation. We should be able to share with you our solutions for that next time.
See also: RESEARCH ANALYSIS: Review of seating technology