Continuing just-auto’s series of interviews with tier one suppliers of electronic braking systems, Matthew Beecham talked with Dr Sören Kirchner, Head of Segment Electronic Parking Brakes within the Hydraulic Brake Systems Business Unit of Continental‘s Chassis & Safety Division and Dr Hans-Jörg Feigel, Head of Future Brake Systems Development within the Vehicle Dynamics Business Unit of Continental’s Chassis & Safety Division.
Could you update us on the stage of development Continental is at with brake-by-wire and how you will push back the technical boundaries?
Dr Hans-Jörg Feigel: Less is more – in keeping with this motto, the innovative MK C1 reduces the number of individual components in the braking system while simultaneously increasing its performance. In the MK C1, the brake actuation, brake booster and control systems (ABS, ESC) are combined into a compact, weight-saving braking unit (up to 4 kg less than a conventional braking system). The electro-hydraulic MK C1 can build up braking pressure significantly faster than conventional hydraulic systems, thereby fulfilling the increased pressure dynamics requirements for new advanced driver assistance systems in order to prevent accidents and protect pedestrians. In addition, the system can fulfil the requirements for a regenerative braking system without any additional measures, while providing a high level of comfort.
Our main reasons for developing the new brake were the reduction in weight and installation effort, as well as in fuel consumption and CO2 emissions. At the same time, system dynamics (reduction in stopping distances with brake assist systems) and comfort (low-noise brake actuation is important for quiet electric vehicles) are enhanced. With the MK C1, we have developed a brake system that can fully cover ‘mixed platforms’ (standard, hybrid and electric vehicles) without compromising on recuperation ability. The start of production is planned for 2016.
Some say that while hydro-electric and electromechanical brake systems are potentially safer than conventional braking systems – due to the potential for greater integration with ABS and ESC – safety concerns have held them back. What’s your view?
Dr Hans-Jörg Feigel: Indeed, such systems like electromechanical calipers are still a highly promising technology, but unfortunately, it cannot be realised commercially at this time.
How well do you really know your competitors?
Access the most comprehensive Company Profiles on the market, powered by GlobalData. Save hours of research. Gain competitive edge.
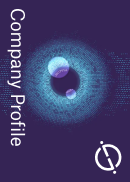
Thank you!
Your download email will arrive shortly
Not ready to buy yet? Download a free sample
We are confident about the unique quality of our Company Profiles. However, we want you to make the most beneficial decision for your business, so we offer a free sample that you can download by submitting the below form
By GlobalDataAlthough brake reliability is clearly a concern, noisy brakes tends to be another reason consumers bring their cars to the dealership. So if brake-by-wire could virtually eliminate these complaints, improve reliability and thereby cut warranty costs then this would be a possible advantage for customer and consumer alike. What’s your view?
Dr Hans-Jörg Feigel: A hydraulic-by-wire system like the MK C1 has many possible advantages for customers and provides the ideal conditions for determining every conceivable contribution to driving safety provided by the braking system, in a sustainable and calculable way. The “power on demand” principle of braking reduces energy requirements for the braking system, and a pulsation-free linear pump means a much lower noise emission level than in conventional solutions with ESC multi-piston pumps and the electric vacuum pumps that are often required. Drivers will also appreciate the quiet braking system because of the virtually silent operations.
I guess that the size and bandwidth of car platforms these days are so high that a single electronic brake system is not cost-effective. How do you set about addressing that? i.e. is it about developing a modular and scalable brake system that combines the advantages of a best fitting technical solution for the special need of the OEM in each platform cluster with the volume effects for common subsystems and small application costs for the variants?
Dr Hans-Jörg Feigel: The process of innovation in electronic brake systems is far from over. Our systems undergo continuous further development with regard to safety, comfort, and costs. We can serve a wide range of different customer requirements with a broad product portfolio, and we offer solutions tailored to the requirements of the various vehicle segments and markets. The MK 100 is our latest generation of electronic brakes – it is based on a modular product family and can be scaled as desired: from a motorcycle ABS, with or without an integral brake function, to high-end solutions with extremely powerful, low-pulsation pump variants with a high level of running smoothness. Two examples:
MK 100 ABS Entry: Low in its project application efforts, the MK 100 ABS Entry has been designed for the vehicle segments A, B and C in the growing markets, and with the XT version can be extended to cover the D vehicle segment as well. The packaging is compact and extremely light. Furthermore, throughout the MK 100 product family, the hydraulic and electrical interfaces are compatible with each other, which makes the MK 100 easily applicable for platform concepts of car manufacturers wanting to benefit from a truly scalable product range. The MK 100 ABS Entry will be produced locally in the markets of China, India and Brazil.
MK 100 XT: The most recent addition to the MK 100 brake family is the MK 100 XT which has been designed for heavy vehicles or vehicles with heavy loads, such as E segments, SUVs and pickups. It is an extension of the MK 100 set up with larger valves and higher pump dynamics in order to meet the respective requirements.
With two model types available, the MK 100 XT Base offers all standard ESC functions up to Adaptive Cruise Control functionality, whereas the MK 100 XT Premium offers additional Full Speed Range Adaptive Cruise Control, as well as best NVH and brake comfort. Furthermore, it can be used in hybrid vehicles with a simple software adaptation with an efficiency of 98 percent.
As part of the MK 100 family of brakes, the MK 100 XT can offer all possible functional options, since it is based on the same proven technology (including PYA, IPB, EIP (ESC Integration Platform), etc.). The application process is easily implemented through parameterisation and is therefore ideal for the implementation together with MK 100 systems. Third-party actuators can also be controlled and electric interfaces US CAR and EuCon are also offered. A special focus is on the hydraulic flow rate, thus improving active safety through high brake dynamics.
But also in regards to our integrated brake system MK C1 we can expect a scalable family approach. With increasing volumes the requests but also the possibilities will rise to optimise cost, weight, functionality with variants.
I guess reducing stopping distances and weight reduction will always be a priority when it comes to design and development of braking systems, yet to what extent is improving the brake feel important to consumers?
Dr Hans-Jörg Feigel: Ongoing weight optimisation for a contribution to CO2 reduction and reducing the stopping distance are indeed important topics. But also the brake feel plays a major role. The MK C1 is a good example: The pressure in the simulator chamber is hydraulically independent of the level of force on the wheel brakes, adjusted by a highly dynamic electric motor. The driver does not notice any difference in pedal pressure if the ESC or the ABS intervenes because they are uncoupled from the pedal. In contrast to existing systems that work with either an active booster or a vacuum reservoir, it produces better control over the pedal feel. The characteristics of the pedal feel (curve) of the MK C1 are not just adaptable to a specific make or model with regard to pedal effort/travel. The driver or the situation can also influence vehicle deceleration through software parameters. Uncoupling also provides ideal conditions for recuperation in regenerative brake systems. For example, highly dynamic changes are also possible without the driver noticing any lapses in braking.
Turning to electric park brakes (EPB), what are the forces driving innovation for passenger cars? And are those drivers the same for every car segment?
Dr Sören Kirchner: EPB innovations are driven by interior reasons. The EPB differs from the traditional parking brake in that it is not operated by a mechanical handbrake or footbrake lever. It is activated either by the driver pressing a switch or automatically by means of special add-on functions. This opens up new possibilities when designing the vehicle interior; better use could, for example, be made of the space between the front seats, for stowage compartments and, in particular, for controls which drivers need to have within easy reach. If the navigation and driver information systems were placed there, for example, drivers would not be tempted to take their eyes off the road. In addition to more space, EPB also offer a variety of convenience and assistance functions, making a driver’s life not just more comfortable but safer, too. There is an emergency-brake function for the unlikely event that the service brake should fail.
We expect that the conventional hand brake lever will disappear from increasing numbers of vehicles within the next decade. By 2015, something like one in four cars produced in Europe will be fitted with an EPB; that’s more than five times the number compared with 2008. EPB are rapidly making inroads in every category of car are becoming ever more commonplace.
Where do you see the greatest growth potential for EPB in the next few years?
Dr Sören Kirchner: In the next few years the EPB will be fitted to an increasing range of vehicle models in all classes. The ‘Caliper-Integrated’ design is gaining significant ground against ‘Cable Puller’ systems. The EPB offers drivers greater convenience and interior design opportunities for vehicle manufacturers. The take rate of EPB in global passenger car market will increase in Europe, NAFTA and Asia. The most growing markets are North America and China. The request for EPB in China is heavily increasing and will reach the same level as Europe is today within next 5-7 years. In all other BRIC countries the demand is on a much lower level – only in Brazil we can see a slight increase driven by global vehicle manufacturers.
Could you update us on the stage of development Continental is at with its EPB and your development aims?
Dr Sören Kirchner: Continental, by exploring the advantages of EPB, offers different function solutions according to customer’s requirement. The EPB embodies many functions such as Apply & Released via button, Automatic Apply, Drive Away Release, Hill Hold and dynamic brake function. Compared with the conventional mechanical system which is hand operated, it provides many more comfort and convenience features to drivers.
To cover the huge variety of vehicle types, Continental offers different EPB system solutions for different rear axle brake configurations. This refers in particular to the service brake on the rear axle, into which the EPB is integrated.
EPB-CI: The “caliper integrated” electronic parking brake (EPB-CI) is a solution for floating caliper disc brakes. A floating caliper is combined with the components of an electric parking brake. The electrical operation takes place via an electronic system integrated into the ESC (Electronic Stability Control) system. The system also consists of two electrical combined calipers as well as the EPB-specific operation software.
EPB-DS: The EPB-DS (“duo-servo”) is a solution for duo-servo brakes. This is a highly efficient self-boosting drum brake, fitted in the brake disc hat. The EPB-DS is used especially in premium-class vehicles, sports cars, and SUVs in whose case separating the service brake and the parking brake is particularly important. The electrical operation takes place via an electronic system integrated into the ESC system or a separate control unit. The system consists of two electrical actuators and an electronic system that is either separate or integrated into the ESC and has the EPB-specific operation software.
EPB-DB: The drum brake electronic parking brake (EPB-DB) is a solution for vehicles with purely drum brakes on the rear axle. The way a drum brake works is via the “simplex” principle. The electrical operation takes place via an electronic system integrated into the ESC system. The EPB-DB is tailored especially to lower vehicle segments, which to date have been equipped only with a mechanical parking brake that is integrated into the existing drum brake on the rear axle. The system consists of two drum brakes with integrated electrical actuators and an electronic system that is integrated into the ESC and has the EPB-specific operation software.
As demand for powertrains with energy recovery systems increases, the electronic integration of systems that help the driver better control the vehicle is clearly desirable. So I guess we can expect to see more examples of system integration in the braking arena, possibly EPB and brake-by-wire?
The remainder of this interview is available on just-auto’s QUBE research service