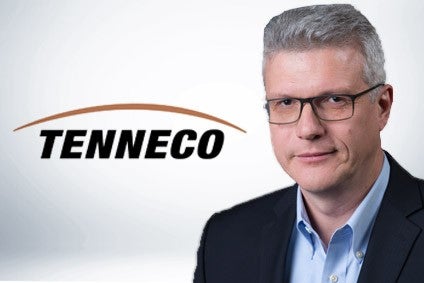
Although hybrids are becoming more popular with manufacturers – the technology being a relatively simple, cost-effective way to meet regulation and customer demand for some level of electrification in their next vehicle, plus being easier to develop than a vehicle from scratch – the engineering presents significant issues in terms of packaging, managing heat transfer to other components and addressing the changes in sound when switching between different modes/source of power. Continuing just-auto/AIC's series of interviews, we spoke to Dmitri Konson, Vice President Global Engineering of Tenneco´s Clean Air business group, about active exhaust valve technology and how its use has evolved to become a key part of hybrid exhaust architecture, rather than being a device that has been previously used on many vehicles, particularly those of high performance, to meet noise regulation.
Why do hybrid vehicles present such an engineering challenge?
Firstly, they require the packaging of both an internal combustion engine (ICE) powertrain and a complete electric powertrain, including battery pack, within the constraints of the same vehicle without considerably reducing effective passenger and luggage space. Secondly, the powertrain acoustics must be managed to minimise sound variations between the different driving modes; ideally, drivers should not notice the transition between electric and ICE operation or between different engine modes in general. Thirdly, thermally sensitive electronic components must be suitably protected, due to their close proximity to heat sources. These challenges become even harder to solve in smaller vehicles, such as city cars, and in combination with larger battery sizes required for vehicles with higher degree of hybridisation, such as plug-ins.
How can exhaust system technology help?
Exhaust technologies play a major role in enabling hybridisation. Electronically controlled valves can reduce the exhaust package space requirements, improve the acoustic control and improve engine efficiency by reducing backpressure. A smaller exhaust package frees up space for the various hybrid systems, while improved sound control reduces the change perceived by the occupants as the vehicle switches between different drive modes. Special versions of our electronic valves can withstand extra high temperatures, which permits more compact exhaust systems with greater packaging flexibility, further easing the issues related to limited space.
Conventional exhaust design is constrained by several conflicting requirements: the acoustic levels must comply with legislated limits; the sound quality must meet the vehicle maker's targets; and backpressure must be minimised to ensure maximum engine efficiency and reduced CO2 emissions.
Conventional exhaust design is constrained by several conflicting requirements: the acoustic levels must comply with legislated limits; the sound quality must meet the vehicle maker's targets; and backpressure must be minimised to ensure maximum engine efficiency and reduced CO2 emissions. Satisfying these requirements simultaneously usually means increasing the exhaust system volume e.g. by increasing the muffler volume to cut unwanted acoustic interactions that occur at particular engine operating conditions.
How well do you really know your competitors?
Access the most comprehensive Company Profiles on the market, powered by GlobalData. Save hours of research. Gain competitive edge.
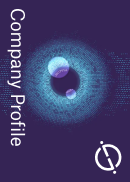
Thank you!
Your download email will arrive shortly
Not ready to buy yet? Download a free sample
We are confident about the unique quality of our Company Profiles. However, we want you to make the most beneficial decision for your business, so we offer a free sample that you can download by submitting the below form
By GlobalDataBy using electronically controlled valves it is possible to minimise unwanted noise by adjusting the pass-through area of the pipes and by providing additional acoustic damping especially in part-load operation conditions without introducing additional volume. This can satisfy both acoustic and efficiency requirements while minimising the exhaust package size.
How do Tenneco's exhaust valves work?
Our active valves offer a variety of different electronic interfaces, including status and diagnostic feedback capabilities for On-board Diagnostics (OBD). They use a pivoted flap driven by an electric actuator to vary the flow cross-section through the exhaust and can be configured in 'base' and 'smart' versions. The 'smart' actuators feature comprehensive, integrated electronics, that adjust the valve flap position independently based on commands sent from the engine control unit through the vehicle data network. The 'base' system features a less complex electronics unit and is directly operated by the engine control unit.
Special versions can withstand extra high exhaust gas temperatures, using an innovative arrangement in which the actuator is decoupled from the valve body. This is a significant step forward in actuated valve design, which greatly reduces heat conduction to the valve electronics. When combined with our latest developments in valve materials, this enables their use on vehicle architectures with extremely high exhaust temperatures.
What kinds of vehicles present the greatest exhaust temperature challenges?
High performance vehicles with mid- or rear-engine layouts are often the most challenging because they offer less space than a front-engine architecture and can generate very high heat flows. An example is the 2020 Corvette Stingray, the first-ever mid-engine Corvette. We developed and supply the complete 'cold end' exhaust system, featuring a number of electronic valves to achieve a low system back-pressure and optimised engine efficiency, while meeting regulatory requirements and preventing excessive heat transfer to surrounding components. The experience gained through such applications has been directly relevant to developing solutions for hybrids because, while the vehicle type may be quite different, the issues to be overcome are broadly the same.
Are there other ways to improve thermal management within a confined space?
A significant factor in overall exhaust system packaging is limiting the transfer of heat to surrounding components. In the case of a high-performance supercar, it may be driven by the proximity of composite body panels; in the case of a hybrid it's more about protecting the vehicle's electrical and electronic components.
Advanced, multi-layer heat shield materials can present a much slimmer profile than traditional materials for a given level of thermal insulation. This significantly reduces the overall envelope of the exhaust system and allows it to be safely routed closer to sensitive components.