Ian Henry of AutoAnalysis visited the new Opel plant at Russelsheim currently being built close to the existing factory.
Russelsheim and Opel, an industrial symbiosis?
Russelsheim has been synonymous with Opel since the company’s inception. In addition to manufacturing the current and soon to be replaced Vectra and Omega cars, Russelsheim is both the headquarters of Adam Opel AG, GM’s main European operation and the location of the ITDC (International Technical Development Centre) which leads the design and development of Opel (and Vauxhall) cars. As such, it was not entirely surprising that Russelsheim has remained a key location in GM’s European manufacturing footprint. While most other GM sites around Europe have been the subject of much debate surrounding their future, Russelsheim seems assured of its role and position in GM’s regional manufacturing footprint.
![]() |
New Rüsselsheim plant: Bird’s eye view |
An all-new plant is on the way …
After extensive union negotiation, Opel launched itself on a plan to re-shape the existing Russelsheim plant. The new factory is barely six months’ away from starting Job One on the new Epsilon programme, the basis for the new Vectra; within a year or so of this programme starting, construction of a new paint plant will begin and its completion will follow the end of production of the Omega and its replacement by a new large vehicle. By 2006, the new Russelsheim plant will have an annual capacity of 270,000 units. The decision to create the new Russelsheim was made in May 1999.
Major investment … and a reduced workforce
How well do you really know your competitors?
Access the most comprehensive Company Profiles on the market, powered by GlobalData. Save hours of research. Gain competitive edge.
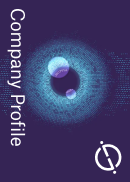
Thank you!
Your download email will arrive shortly
Not ready to buy yet? Download a free sample
We are confident about the unique quality of our Company Profiles. However, we want you to make the most beneficial decision for your business, so we offer a free sample that you can download by submitting the below form
By GlobalDataThe new plant has already consumed DM1.5 billion of investment, with more to be spent on the new paint plant. Of the total spent so far, around DM800 million was for construction related items and around DM700 millionn on manufacturing plant and equipment. Part of the new plant investment has been on a 64,500KN vacuum transfer press, producing large pressed parts, such as side panels, roofs and doors. Around 70 percent of these pressed parts are shipped out to other Opel plants around Europe. In addition to this expenditure – and indeed of more significance – is the new way in which the new plant is organised. There is the new and unusual layout, but there is also the significantly reduced workforce. The ‘old’ Russelsheim employed over 10,000 people, while the new plant – once finished – will employ just 6,000, all of whom have been completely retrained in new manufacturing and assembly techniques.
You can teach old dogs new tricks …
Assembly workers’ team leaders have all been sent to work at the Opel plant in Eisenach to learn the principles of lean production, the underlying theme of the new plant. The entire workforce, some of whom have worked at Opel for over 15 years, have been re-trained, part of which process involved making cars out of paper; origami meets the automotive industry.
![]() |
New Rüsselsheim plant: simulated assembly line |
Lean production in action …
The plant will run according to the five main themes of the Opel Production System which are: continuous improvement, standardisation, staff involvement, quality from the beginning and short processing times. As part of the re-training process, the workforce has been closely involved in defining their work tasks which they will perform in the new assembly hall. Whereas on traditional assembly lines the workforce will have been told what to do, here the workforce is closely involved in defining what they will do at each stage and they have helped to define their standardised work tasks.
Automation mainly in the body shop …
The body shop, designed by manufacturing systems integrator FFT, is almost wholly automated, with 600 robots, while the general assembly and final trim areas remain largely focused on manual assembly. The transporter mechanisms and systems in the assembly area have been designed largely by Durr. However, a number of modules – eg the exhaust and fuel rails, cockpit and HVAC system – will be pre-assembled within the Opel plant before being fitted to the car; another 15 modules – such as the wiring systems, headliner and B-pillar and seatbelt assembly amongst others – will be pre-assembled by logistics provider Ferrostaal, in what Opel calls the Business Mall at one extremity of the Russelsheim site.
Extensive use of modules …
Ferrostaal will deliver the 15 modules and 58 components on a sequenced basis directly to docking stations on the edge of the assembly hall that will hold no more than two hours’ worth of stock. A number of suppliers, of seats for example, will deliver directly to the assembly line, depositing their components at one of the 70 docking stations which are located around the outside the assembly hall. In total around 50 percent of the components needed to make the new Vectra will pass through the Business Mall. Given that the engines will be delivered directly from Opel’s various plants around Europe, as will seats, and the metal pressings will mainly come from the Russelsheim press shop, this concentration of components and systems through the Business Mall clearly represents a major advance in production efficiency and reducing stocks over the existing plant. Opel spokesmen speak of a 50 percent saving in the time required to make the new model.
![]() |
Ergonomics simulation: installation of the pedal module |
Ergonomics played a major role in the design of the assembly systems
The assembly line has been designed through the application of virtual reality techniques, with each stage of the process simulated to highlight problems, including un-ergonomic processes which have since been eliminated. One example of the concentration on ergonomics has been the decision to eliminate the need for assembly line workers to descend into pits to fit parts: instead the cars will lift on hydraulic platforms on the assembly line, so that workers can carry out their tasks at the optimal height The assembly hall itself has an unusual layout and floor plan: it covers 48,000 square metres, shaped in a half-star; this somewhat unusual shape offers a number of advantages – there is a good view of the entire assembly area, distances between stages in the assembly prices are clearly much shorter than in a conventional line and the use of 70 truck docking stations.
The assembly line itself follows four “fingers” of the star (the fifth is used to assemble the door and cockpit modules). Each of the 5 “fingers” forms a distinct, separate strand within its own buffer zone, allowing the line to be halted or de-coupled when a problem in the assembly process emerges – the assembly line utilises the “Andon” principle from Japanese lean production systems
The new plant will embody all the principles of lean production which Opel has been progressively adopting since its first acquainted itself with Japanese production techniques. In the US in the 1980s, GM started joint ventures with Toyota (NUMMI) and Suzuki (CAMI). This was followed by the lean plant in Eisenach in eastern Germany (1990), the re-building of the Antwerp plant in Belgium (1998) and the adoption of new, lean production plants in Thailand, Poland, China and Argentina, producing Opel designed models. The Antwerp site involved adopting lean production in a brownfield site, while the Eisenach plant involved adopting lean production in a greenfield site; the new Russelsheim involves establishing lean production in an all-new plant built in a quasi-brownfield environment.
To view related research reports, please follow the links below:- The world’s car manufacturers: A financial and operating review Automotive regional report: Western Europe |