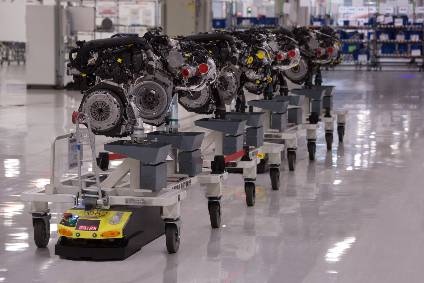
Volkswagen Group brand SEAT has released details of its intelligent robots' operations at its Martorell, Spain, manufacturing plant.
Some 125 automated guided vehicles (AGV) share the workspace every day with 7,000 employees at the SEAT factory in Martorell. The AGVs transport 23,800 parts daily and cover a distance of 436,000 km every year, equivalent to the distance between Earth and the Moon.
SEAT says robot-based transport eases and optimises factory workers' jobs and reduces production time by 25%.
An AGV will typically start work at 5am in one of the workshops at the SEAT factory and make up to 2,800 rounds of work every day.
This is how these mobile robots work:
- They scan a barcode to make sure they transport the right part, and a sensor then opens the warehouse door so they can follow their circuit. This is how some of the 125 AGVs begin their day, routinely crossing paths with each other and with the 7,000 factory workers in what 'appears to be a fully synchronised dance performance'. The automatic robots transport engines, gearboxes, shock absorbers or door windows, and their individual payload is up to 1,500 kg in weight.
- Every year, the AGVs travel over 436,000 km, which is more than the distance between Earth and the Moon. When following their pre-set paths they know when to stop at a red light or when a worker crosses their path thanks to their 360 degree perimeter vision. They coordinate with 'pedestrians' and guarantee their safety by alerting of their presence with laser scanning lights.
- The AGVs at the Martorell factory follow 40 guide paths set out with magnetic tracks embedded in the floor. Each route lasts between 1 and 7 minutes. During this time, the robots follow the steering circuits and automatically reduce their speed in curves so they do not lose stability when carrying heavy loads and are able to maintain a safety distance. In the future, these guide paths will give way to GPS navigation systems.
- Five employees (humans) configure, and if necessary, remotely modify the path settings of all the AGVs from a control room. A centralised server gathers information from the software installed in each robot, and their exact position is displayed with a numerical symbol on the screens in the room. A green light indicates their full power performance; if it turns amber it means they have stopped due to an obstacle or because they are recharging their batteries. The system also detects possible technical problems and is able to solve them immediately.
- Intelligence sharing in Industry 4.0: The 4th industrial revolution enables workers to control processes to optimise decision-making and let these collaborative robots perform the most physical and repetitive tasks. As an industry benchmark in digitisation and automation, SEAT also foresees other measures such as integrating software and hardware in production and logistics.
Martorell plant – key metrics and details
How well do you really know your competitors?
Access the most comprehensive Company Profiles on the market, powered by GlobalData. Save hours of research. Gain competitive edge.
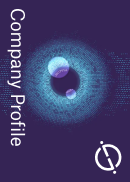
Thank you!
Your download email will arrive shortly
Not ready to buy yet? Download a free sample
We are confident about the unique quality of our Company Profiles. However, we want you to make the most beneficial decision for your business, so we offer a free sample that you can download by submitting the below form
By GlobalData- Martorell is the headquarters site of the Volkswagen brand SEAT.
- Located 30 kilometres from Barcelona. The town of Martorell is at the confluence of the Llobregat and Anoia and has around 28,000 inhabitants. The biggest employer is the car manufacturer.
- Opened in February 1993 by HM Juan Carlos I of Spain.
- Total surface area of over 2,800,000 square metres (the equivalent of 400 football fields) of which 260,000 are landscaped areas.
- Some 7,000 people work in its 15 buildings, divided into morning, afternoon and night shifts.
- Current daily production at the facility is in the region of 2,100 units (443,000 annual units), which are then shipped for sale via road, sea and rail. SEAT sells its cars in 75 countries. The plant was hit hard by the post-2008 recession and car market collapse in Spain, which explains the addition of Audi production (Q3) from 2011 to raise capacity utilisation (successfully). It is also now benefiting from the recovery to Spain's car market and higher demand in Europe.
- All SEAT range models are made at Martorell – with the exception of the Alhambra, Toledo and Mii. It also makes the Audi Q3. However, later this year, Audi production at Martorell switches to the A1 (transferred from Brussels) with Q3 production moved to Audi's Hungary (Gyor) facility.
- The production process begins at the presses, where body parts are stamped. The area has three lines where parts are transported automatically from die to die – thus making the process continuous – to shape all the car's bodywork elements.
- At the second stage are the bodywork shops. They are the most highly-automated part of the factory, and within them more than two thousand robots make almost 100% of the bodywork's spot-welds. Ultrasound-controlled laser welding is also undertaken for quality, efficiency and material saving benefits.
- Painting is carried out in two different workshops. In the first the surface priming process is carried out. In the second robots apply the various coats of paint and finishing lacquer, both inside and outside the vehicle.
- Once painted, the bodywork is transferred to the assembly workshop, where the interior parts are fitted. Virtual tools – enabling visualisation of the processes before implementation – are used in order to improve efficiency in the introduction of new processes.
- 'Just in time' supply to the assembly line is facilitated by an entire industrial estate close to its facilities. In recent years important innovations have been introduced in the system, such as the JIT supply of vehicle front-ends using low-cost automatic transport systems.
- The SEAT al Sol project has transformed the Martorell facility into the largest photovoltaic panel plant anywhere in the automotive industry world. The 53,000 solar panels on the rooftops of the workshops and the temporary vehicle holding areas generate 15 million kWh per year, entailing the elimination of 7,000 tonnes of CO2 annually.
- The Martorell facility has two rail links totalling 40 kilometres in length – the Autometro, transporting vehicles directly to the Port of Barcelona; and the Cargometro, bringing components directly from Barcelona's Zona Franca. Taken together, these rail links take some 50,000 vehicles trips off the road and eliminate the emission of 2,000 tonnes of CO2 per year. The plant also has a combined heat & power plant, generating 50% of the electricity and 90% of the thermal energy it consumes, thus eliminating as much as 12,800 tonnes of CO2 per year.
- Production speed: 1 car every 40 seconds.