
Car seats are becoming lighter by as much as 50 percent. This paradox is achieved through novel designs’ using new materials, foams and assembly mechanisms writes Matthew Beecham.
Weightwatchers
Weight minimisation driven by efficiency has led to the use of alternative and advanced materials in designing seats. Space creation inside the vehicle interiors has become very critical with the explosion of added content and features. Discerning tastes also means consumers want more flexible living space within their cars.
Seats will continue to be lighter and thinner partly thanks to the increasing use of high strength low alloy steels and new joining methods for both steel-to-steel and steel to other materials. For example, Johnson Controls Incorporated (JCI) claims that the all-steel version of its so-called Synergy Seat structure is 32 percent lighter than conventional systems while the aluminium-steel version – targeting hybrid vehicles – is up to 40 percent lighter. The seat’s comfort shell, side shields and back panels are made of recyclable polypropylene.
In a separate development, JCI recently revealed how it s reducing the use of metals in vehicle seat structures by replacing them with multi-material systems in its so-called CAMISMA (which stands for ‘carbon-amide-metal-based interior structure using a multi-material system approach’) research project. The supplier claims that these seats are more than 40 percent lighter than conventionally manufactured seat structures and equally as safe.
‘Green’ seats
How well do you really know your competitors?
Access the most comprehensive Company Profiles on the market, powered by GlobalData. Save hours of research. Gain competitive edge.
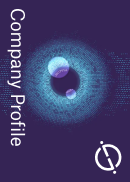
Thank you!
Your download email will arrive shortly
Not ready to buy yet? Download a free sample
We are confident about the unique quality of our Company Profiles. However, we want you to make the most beneficial decision for your business, so we offer a free sample that you can download by submitting the below form
By GlobalDataOther seat makers are also using alternative ‘green’ materials in their vehicle seats. For example, Lear is using bio-based materials for the replacement of petroleum-based products for the Ford Mustang. Magna Seating and the Woodbridge Group are also supplying bio-based polyurethane foam to Ford for seats in the Ford Escape.
Ford has claimed that its Fusion (known as Mondeo in Europe and Asia Pacific) is the first global vehicle programme from any automaker to use seat fabric made from recycled material, with the potential to recycle enough plastic bottles and post-industrial waste to make 1.5m yards of fabric annually.
Aside from green materials, a great deal of work is being focused on different seat fabrics, creating more breathable or more waterproof surfaces, and even adding built-in fragrances designed to increase feelings of well-being.
Flexible seating
Meanwhile, the ability to transform the cabin to suit different needs remains a hot topic in the sport utility and minivans segments. As consumers demand more flexibility from their vehicles, suppliers are coming up with yet more novel ways to collapse the rear seat rows. For its part, Faurecia used last year’s Paris motor show to reveal its ‘one touch’ technology which can be used to automatically fold down a car’s rear seats. The new Renault Espace crossover is the first Renault production model to feature this innovation. The ‘one touch’ function can be used to fold down any seat in the second and third rows using a control unit in the boot (trunk) or using the multi-function display on the instrument panel. The seats and headrests automatically fold into the floor to create a surface that is almost entirely flat. The electronic system also locks the system when the seat is occupied or the vehicle is moving.
An innovation that caught our eye at the 2015 Detroit motor show featured on JCI’s so-called SD15 (which stands for ‘seating demonstrator 2015′). With a focus on first- and second-row seating in a simulated vehicle environment, the concept addresses global industry trends of urban mobility, comfort and autonomous driving. The SD15’s front row features a power driver seat mounted to a curved track, eliminating the need for separate and complex mechanisms found in conventional seat arrangements. The seat offers a console mounted directly to the seat structure that moves conveniently with the occupant, instead of being fixed between the seats. In addition, the SD15 showcases the company’s new slim tilting head restraint. This latest generation of slim head restraints can be combined with a tilting mechanism. Both the front and rear seats showcase new ink jet printing fabric technology, which allows for a wide variety of customer customisation of colours and patterns to help automakers distinguish their brands. The SD15 design allows for the packaging of a 48-volt battery under the seat, highlighting the latest battery technology from Johnson Controls’ Power Solutions business.
JCI also used this year’s Detroit motor show to unveil its so-called Loft seat, a second-row seating solution for mid-sized luxury vehicles. Its features include a ‘Connectivity Console’ that provides a multi-level comfort and storage solution with wireless charging USB ports and unique telescoping cup holders.
JCI also offers an automatic pre-seat adjustment or ‘smart seat’ control. It uses an algorithm that determines the ergonomically correct and safe seat position using body size. Once the body size has been input using an app, the vehicle seat automatically moves to a near perfect position for a comfortable and safe drive. For example, the seat is pre-adjusted to a forward, high position and the head restraint is set low for a 5’3″ driver.
Tomorrow’s seats
As for tomorrow’s car seats, Ford has a vision. The automaker says its Escape is the first Ford vehicle with a global seat architecture specifically designed to conform to the “Ford seat DNA”. The DNA is a set of quantifiable measurements for each system in a new vehicle designed to provide a consistent feel across all Ford vehicles worldwide. Many of the changes to the new seats aren’t readily apparent to casual observers, says Ford. One of the elements of the Ford seat DNA covers the contour of the seat back. When viewed from above, other seat backs typically have a U-shape, where the main central portion of the cushion is flat, with side bolsters emerging from the outer edges. A driver with a torso that is the same width as the seat would be properly restrained during cornering manoeuvres. However, a thinner driver could find him or herself sliding toward the outer bolster when going around a curve or just positioned too far to one side or the other. The driver’s seat of the Escape offers a ten-way power adjustment and rear seat passengers will benefit from an available reclining seat back.
We can also expect to see more fibre-reinforced composite back frames that provide a low mass design and improved packaging efficiency.
Finally, it’s clear that developments in vehicle seating have been taking place much faster than may be apparent on the surface. OEMs are demanding greater differentiation in their seat designs, customers want more and more luxury such as cooling and heating, and ergonomists are understanding more about what the human frame needs in order to be comfortable. In explaining some differences in the use of vehicle seats across regions, an auto executive of a major seating manufacturer told us: “What is expected from the rear seats is completely different from the front seats. That is because, according to the car segments, the rear seats can be either greatly used or seldom used. In China, for instance, the rear seats are most important because it is where the owner of the car will be sitting as he will be chauffeured. So there are a lot of features packed into the rear right seat of the car. The front seat should be comfortable but not especially packed with functions. So there is not one rule for all vehicle segments and all countries. They are all different.”