As the European front-end module market reaches maturity, suppliers are discovering blossoming markets further afield. Matthew Beecham fronts just-auto’s latest review of the FEM market.
What is a front-end module? It depends who makes it and for whom. The module is made of several components and sub-assemblies, including structural front-end carrier, headlights, radiator, engine cooling fan systems, and energy absorption beam. It may also contain wiring harnesses and related electrical functions and can include the bumper fascia.
The major functions of the front-end components are to act as a body frame, taking in and cooling air, protecting the vehicle and its occupants in the event of a collision, properly illuminating the front of the vehicle as well as improved appearance and exterior styling.
By outsourcing front-end modules, automakers are able to reduce the number of operations on their assembly lines, simplify their supply chains, reduce modular weight and improve the ergonomic aspects of the assembly process. It can also help cut tooling costs and improve working capital. The most important potential benefit of modular construction is standardisation, allowing suppliers to offer standard solutions to different manufacturers and hence bring costs down. On the global stage, the main proponents of outsourcing front-end modules include the Volkswagen Group, Chrysler, Hyundai Kia, Nissan, Mercedes, BMW and Fiat.
“Our customers select us because we bring our global experience to the table,” said Martin Schüler, president and CEO of HBPO. “In many cases HBPO is completely responsible for the design and the integration of functions in the FEM including the qualification and selection of suppliers. We reach the targets for weight and space while fulfilling the safety requirements. This leads to a better performance of the car and to better insurance classifications which then results to higher sales.” Headquartered in Lippstadt, Germany, HBPO GmbH was founded in 2004 as a joint venture between the three auto parts suppliers, Hella, Behr, and Plastic Omnium to combine their expertise to produce front-end modules. It is the successor to Hella-Behr Fahrzeugsysteme GmbH joint venture which had been established in 1999. Each partner is a leader in its respective field: Hella in lighting and electronics, Behr in air conditioning and engine cooling systems, and Plastic Omnium Auto Exterior in body parts and modules, impact absorption and pedestrian protection systems. HBPO employs 1,300 people at sites dotted around Europe, North America and Asia.
How well do you really know your competitors?
Access the most comprehensive Company Profiles on the market, powered by GlobalData. Save hours of research. Gain competitive edge.
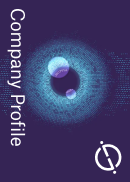
Thank you!
Your download email will arrive shortly
Not ready to buy yet? Download a free sample
We are confident about the unique quality of our Company Profiles. However, we want you to make the most beneficial decision for your business, so we offer a free sample that you can download by submitting the below form
By GlobalData“We supply front end modules at Audi, BMW, and Chrysler and front-end carriers at Renault and PSA,” said Martial Pata, vice president in charge of Faurecia’s front-end module division. “We leverage over 15 years experience in this product and expertise in module architecture to propose solutions that fulfill a wide range of customer needs.” Faurecia produces over 1 million front-end modules, 2 million engine ventilation systems, 3 million front-end carriers and 4 million bumper systems annually. The French group has designed and built front-end modules for a number of vehicles, most recently for the Audi A4, A5 and Q5, BMW 1 Series convertible, and Dodge Avenger
The other main suppliers of front-end modules include Calsonic Kansei, Decoma International (an operating group of Magna International), Denso, Hyundai Mobis, Peguform and Visteon. However, the market has consolidated over the past decade. In terms of further market consolidation, Norm Guschewski, director, business development, exterior modules, Decoma International, told us: “We believe anything can happen in this environment. Becoming a global front-end module supplier requires a significant investment in human capital, which many companies simply cannot invest in until a programme is awarded. This can be an inhibitor to many up-start module suppliers.” Decoma International’s front- and rear-end modules include front and rear fascias, cooling modules, energy absorbers, bumper beams, air dams, lighting, grille opening panels, grilles and complete module assemblies. The company globally supplies two million front end modules and 18 million fascias annually.
There are three main markets for front-end modules: Europe, North America and South Korea. In addition, there is some manufacturing in Japan and China. Until recently, the European market was seen as the mainstream for front-end modules with a number of manufacturers. Yet lately this market has shown some signs of stabilisation to the point where it is reaching maturity.
While the European market stabilises, the North American market for front-end modules continues to grow. Guschewski added: “The original North American Big Three have begun to recognise that the European and Asian OEMs have executed many of their car lines with a front-end module strategy, providing best-in-class fit and finish, with significant cost and weight savings. Our customers have completed their own internal benchmarking and are questioning their past decisions.” Over the past few years, Decoma International’s position in the North American front-end module market has strengthened due to its stronger ties with Chrysler. “Chrysler has been the most aggressive in its shift to an FEM strategy.”
In South Korea, Hyundai Kia continues to outsource front-end modules, making this region a blossoming market for suppliers. “The Korean market is running very well for us,” said Joachim Amrhein, director of sales and marketing, HBPO. “Our joint-venture, SHB, together with our partner, SL, are the leading partners for Korean OEMs. Our focus is on the local development and assembling of front-end modules for the Korean and Asian market.”
The Japanese market for front-end modules is also gaining in importance. For example, Nissan is a key player into the market while Mazda has front-end carriers in composite material.
As far as the Chinese market is concerned, manufacturers see good growth for front-end modules in the region over the next few years.
Not only is the front-end important aesthetically and functionally, it also plays a fundamental role in safety, says Faurecia. During low-speed collisions, it must protect the expensive components in the front of the vehicle, thereby reducing repair costs. During collisions at higher speeds, its absorption capacities become secondary but it plays an important role in terms of establishing compatibility between different vehicle brands and models to compensate for differences in height and direct energies towards zones of structure deformation of the car. Above all, it has taken on a whole new dimension following recently adopted standards of pedestrian protection. Indeed, the interest in front-end modules has increased partly due to the focus on vehicle safety issues and the need to comply with guidelines from the European Union for pedestrian safety. The first phase of the EU’s stringent pedestrian protection rules took effect in October 2005. This first phase considers ‘leg’ and ‘adult head’ impact and measures injury criteria. In response, some automakers have added plastic energy absorbers to their vehicle’s front bumpers. The second phase will progressively come into force starting in 2010. This will introduce criteria concerning ‘upper leg’ (hip impact) and ‘child head’ impact and will see more stringent ‘leg’ impact criteria.
For some time, engineers at SABIC Innovative Plastics have been pushing back the technical boundaries in the front-end module arena using its plastic innovations. “Pedestrian protection rules effectively require cars to be constructed with a ‘soft’ energy absorbent layer surrounding the ‘hard’ steel crash structure,” said Derek Buckmaster, global market director, automotive exteriors, SABIC Innovative Plastics. “Plastics can enable automakers to help them meet these rules through providing the energy absorption capabilities not readily obtained with steel structures. SABIC offers unique CAE [computer aid design] simulation capabilities and testing facilities dedicated to pedestrian safety protection. Our engineers work side-by-side with OEM and tier one supplier engineering to ensure performance that meets predicted results.”
Buckmaster concludes that plastics can play a substantial role in both structural and aesthetic applications. “This is one of the reasons plastics is such a desired material, because its high range of impact absorption attributes and performance.”