Some 20 years ago, McDonald’s despatched a team to Britain to reconnoitre the hamburger market in Britain prior to the Big Mac invasion. Its first report pointed out that the greasy concoction currently on offer bore no resemblance to the real thing. A crash course of public re-education was essential. When the Japanese tiptoed into automobile manufacture in America back in the mid-80s they must have entertained similar thoughts. Here they were, late entries into the field, discovering that this shrine of mass production was riddled with inefficiencies, over-staffing, deplorable quality and, most of all, a smug indifference towards the consumer.
The Asian newcomers were met with a barrage of cynicism, mistrust, derision and often downright racism. Their efforts were dismissed as ‘screwdriver’ factories, the implication being that whatever they were doing it certainly was not manufacturing, rather the mere assembly of parts imported from Japan.
There had also been resentment – in this case entirely justified – at Japanese intransigence over imports into its homeland. Japan had beavered away behind a wall of specious import restrictions, giving them time to build up an impenetrable home market and huge export sales.
“Asian newcomers were met with a barrage of cynicism” |
In those early days American companies complained bitterly of being excluded from supplying the newly-established Japanese transplant car factories. For their part, the Japanese maintained that as long as quality and efficiency failed to meet their standards then they would continue to buy in from their own proven (Japanese) suppliers.
But Toyota, for one, was prepared to go further, and so the education of America’s suppliers began, principally through ‘the Gospel According to Ohno’, named after the late Toyota production guru Taiichi Ohno. In Japanese eyes, the Toyota Production System, to give it its official title, had all the elements of a crusade. Incorporated were such tenets as bare-bones inventory (if material arrives too early, it’s wasteful), easy-to-read signals to operatives (what you can’t see you can’t monitor), and a war on waste, whether it be money, materials or motion.
This rigid management philosophy has now played its part in transforming the overall efficiency of American industry. And rigid it certainly is. As an example, before Toyota agrees to retrain any supplier, it must undertake not to use increased efficiency to lay off workers. Such a commitment is usually anathema to US companies, accustomed to ruthlessly tailoring the labour force to sales volume, and many would-be suppliers have fallen by the wayside.
How well do you really know your competitors?
Access the most comprehensive Company Profiles on the market, powered by GlobalData. Save hours of research. Gain competitive edge.
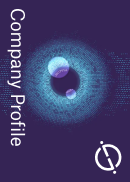
Thank you!
Your download email will arrive shortly
Not ready to buy yet? Download a free sample
We are confident about the unique quality of our Company Profiles. However, we want you to make the most beneficial decision for your business, so we offer a free sample that you can download by submitting the below form
By GlobalDataThe Big 3 and their suppliers, originally wishing the interlopers would just go home, were at first oblivious to the benefits that would flow, but the disparaging remarks from those who foretold a sinister Japanese cartel have long gone. The Japanese have not only stemmed the tide of cars flooding into North America, they have introduced a whole new culture, one eagerly copied by vehicle manufacturers throughout the world. It is now recognised that the ‘intruders’ have made America strong once more. Suspicion has changed to the highest praise of all – imitation.
The lessons have been well taken. What was a one-way brain-drain is now a busy two-way street. What Chrysler learned from Toyota about the basics of lean manufacturing, it was able to apply on minivan production. Toyota taught GM to build model mix on the same assembly line, while Toyota’s managers toured GM European operations to absorb ideas. To complete the circle, American suppliers are now firmly entrenched in Japan itself.
The globalisation of America proceeds apace. Today there are 20 foreign-owned automobile assembly plants in the US, with several more in the pipeline or under consideration. Local purchases of parts for Japanese transplant factories have increased fourfold in the past ten years, and Toyota’s vehicle imports into the US have more than halved. Suppliers to the automobile industry from all over the world today have their technical centres right in the heart of the domestic Big 3’s inner sanctum, Detroit.
GM uses Honda engines in the Saturn, Nissan prises open the US market for parent Renault, Toyota’s stock trades on Wall Street. Cross-border relationships envelop the whole world now. Mercedes and BMW, too, now know that vehicles to their exceptionally high standards can, after all, be made in America. Under the umbrella of General Motors, Opel will shortly market a mini-van, designed in Japan by Suzuki, engined by lsuzu, assembled in both an Opel factory in Poland and a Suzuki factory in Hungary. The true world vehicle.
America’s domestic Big 3 today produce cars of quality as efficiently as any factory in the world. The Ford Atlanta plant, for example, takes only 17.16 hours to assemble the Taurus, achieving the nation’s No. 1 spot for the first time ever in that category.
But there is still a long way to go. Nissan has always excelled in manufacturing efficiency, taking a mere 29.30 hours for the average car across the board, against Ford with 36.24, GM 43.03 and Chrysler 43.58. Building on their experiences in the US, the Japanese too gained confidence and now operate assembly plants in other parts of the world – truly a win-win situation.
“The globalisation of America proceeds apace” |
Instead, the American market is well-balanced, absorbing quality domestic vehicles as well as those from a variety of countries. Gone are those days when the Japanese were regarded as avaricious sandbaggers. It is easy to forget that what almost caused an irreparable schism between the United States and Japan turned out to be a boon to car buyers all over the world.
|
|
Author: Bert Wyatt