In the global automotive seating market, suppliers must offer seats that are more comfortable, durable and safer than last year’s designs but also lighter and cheaper too.
Developments in vehicle seating have been taking place much faster than may be apparent on the surface. OEMs are demanding greater differentiation in their seat designs while motorists look for greater functionality and luxury.
Back in the 1970s, a car seat was a functional component with few or no added value features. Nowadays, with drivers spending more time in their car on longer commutes, they expect a comfortable ride. Consequently, the seat has become an integral part of the car’s overall design and appeal in the showroom. More power content in the front and, more recently, rear seats is becoming common.
Meanwhile, seat manufacturers must develop seats that are lighter, offer more space for occupants and incorporate environmentally friendly materials. These market drivers have led manufacturers to use alternative and advanced materials in designing seats. Space creation inside the vehicle has become critical with the explosion of added content and features. Discerning consumer tastes also means consumer want more flexible living space within their cars.
Safety first
Over the years, new materials and techniques have improved vehicle occupant comfort and wear resistance while reducing weight and cost. Yet manufacturers have developed a number of safety-related seat innovations, too. For example, Lear launched ProTec PLuS, the latest version of its active head restraint products that help reduce whiplash injuries in rear impacts, in the 2009 Honda Accord Coupe.
How well do you really know your competitors?
Access the most comprehensive Company Profiles on the market, powered by GlobalData. Save hours of research. Gain competitive edge.
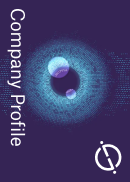
Thank you!
Your download email will arrive shortly
Not ready to buy yet? Download a free sample
We are confident about the unique quality of our Company Profiles. However, we want you to make the most beneficial decision for your business, so we offer a free sample that you can download by submitting the below form
By GlobalData“ProTec PLuS utilises the occupant’s penetration into the seat to move the head restraint forward thus minimising head rotation in turn minimising whiplash,” said Jeff Frelich, Lear Corp’s director of research and design, seating systems. “Lear was first-to-market with its family of active head restraints in 1998 and continues its technical leadership position today.”
Imtiyaz Syed, vice president, engineering, Magna Seating, believes that progressively increasing safety standards, not only from government, but also from non-governmental agencies such as IIHS (Insurance Institute for Highway Safety), continue to impact seating. He told us: “Typically, these are vehicle level requirements, e.g. rear or side impact. The impact on the seat is usually vehicle dependant, i.e. the vehicle level safety engineering team determines what, if anything, may be required of the seat to achieve their target performance at a vehicle level. Our seat structure and mechanism designs continue to evolve to meet the ever rising structural requirements for seat systems.
“Beyond the normal requirements for strength, the seat may need to accommodate a variety of features such as side airbags, seat track position sensors, occupant classification systems, seatbelt pre-tensioners and so on. The biggest challenge is integrating and packaging the increasing safety content.”
Not only are seats becoming safer but more supportive, versatile and pleasant to sit in with a multitude of hidden creature comforts such as adjustable lumbar supports, massage systems, climate control systems, memory mechanisms, height and rake adjustments, self-positioning headrests, built-in seatbelts and, of course, airbags.
Rear seat comfort
As consumers demand more flexibility from their vehicles, suppliers must find yet more novel ways to reconfigure the rear seat rows, often using power.
While the focus has, for some time, been on improving the front seats, automakers have paid more and more attention on the second and third row seats. “Rear seat design is getting more attention specifically in the areas of safety, mass, and flexibility,” said Frelich. “Lear just recently launched our DECS technology on the Ford Fusion Hybrid that significantly lowered mass of the seat system while aiding in the cooling of the battery system. In the area of safety, FMVSS 202a will impact rear seat head restraint systems in September 2010 and Lear has several patented technologies to aid in this mandated law.”
Syed agrees that second and third row comfort has become increasingly important over the past decade. “Examples include seatback recline features, fore/aft adjusters, entertainment systems and deploying bolsters. We’re starting to see more features trickle into the rear rows that are traditionally front seat territory. Examples include seat heat, ventilation and power articulation features.”
Collaboration in design
Nowadays, there is far more collaboration between seat engineers and vehicle designers in order to better match comfort and brand characteristics with certain new vehicle models. Frelich told us: “The recognition of the vehicle interior environment impact on consumer comfort perception is common knowledge and limits of compliance to consumer comfort expectations due to space restrictions can be compliance limiting. We have seen an improvement in this understanding within the OE design and engineering community and have frequent instances where we are asked for our input in early design stages where additional occupant room, foot clearance, etc. are possible. At a minimum there is a new respect for these issues as comfort performance continues to grow as a competitive differentiator and means of improving the necessary interior environment are openly discussed and considered in vehicle interior package design.”
Syed believes that brand characteristics are developed for target demographics and comfort is one of the areas that is tailored to those demographics. For example, luxury brands will often include more comfort features such as additional soft foam, heated and cooled seats, vertically and horizontally adjustable lumbar, massage systems, adjustable cushion length, and adjustable bolsters. “Sporty or performance brands will often use firmer seat foam, and more aggressive bolsters.”
Meanwhile, BMW designers have been working with engineers from JSP and other specialists to archive weight savings of 15% and cost savings of 10% in the construction of rear seatbacks for the BMW 5 Series. The partners began working on the design project in 2005 and series development of the new Sandwich Seatback started in July 2007. The team’s idea was to use a three-part structure to create a lighter seatback, capable of passing statutory impact tests and BMW’s own test schedule.
At its centre is a section of energy-absorbing ‘ARPRO’, with an injection-moulded carrier facing the passengers and a layer of carpet facing the luggage compartment. All three components contribute to impact resistance. ARPRO is an Expanded Polypropylene (EPP) used extensively for automotive parts as well as for packaging and other applications requiring great lightness and strength (it is made by JSP).
BMW says it has integrated the new seatback manufacture into its cockpit production facility. The vehicle maker calculates that the weight saving totals 1.2 kg on an already ‘weight-reduced’ component. Other claimed benefits include a reduced number of components, the elimination of numerous process steps, and improved recyclability.
Environmentally-friendly seating
Manufacturers are also using alternative “green” materials in their vehicle seats. For example, Lear is using bio-based materials for replacement of petroleum based products for the 2008 Ford Mustang.
“Utilising soy-based product posed its unique set of challenges,” said Frelich, “but Lear and Ford worked together at root causing and solving all the technical hurdles we had to overcome. Today we are developing higher concentrations of soy based foams while looking at introduction into other regions of the world.”
Meanwhile, Magna Seating and The Woodbridge Group are supplying a bio-based polyurethane foam to Ford for the seats in the 2009 Ford Escape.
Syed told us: “We have been in production with soy-based seat foam for a couple of years now. However, we believe that seating foam competing for resources in the food supply chain is not the most efficient means of “going green.” That’s why we’ve developed a polyurethane formulation which can accept renewable polyol from a number of non-food natural oil sources. Ultimately, the more sustainable solution is to develop seating foam based on recycled product, which has the potential to reduce or eliminate PU foam ending up in a landfill at the end of life. We think this would contribute far more to true sustainability than having a fraction of the virgin foam come from a renewable resource.”
In terms of recycling seat materials, Paul Compton, president and CEO – Europe, JSP explained that the latest problem to be addressed by his company is the challenge that vehicle makers are facing with tough new European targets for the use of recycled materials. He said: “This has led not only to the development of a new ARPRO grade with recyclate content, but also to a new network of recycling stations across Europe, where JSP will manage the end-of-life processes for components made with our materials. Part of this process has been to analyse the true environmental impact of our material and to compare that with the traditional alternatives.
“We’ve looked at everything from the cost of processing and transporting the materials to the energy used to recover them. The analysis has shown that simply changing a seat core to ARPRO can provide a lifetime CO2 saving equivalent to 2.65g/km. In three out of the nine areas of environmental impact analysed, the wire frame is responsible for the majority of the environmental cost because of its high content of energy-intensive steel. Reducing the steel content therefore brings a disproportionate environmental benefit. The big picture is often complex.”