
Imagine if your favourite pair of jeans could last forever, thanks to self-repairing polymer chains in the fabric. Further, imagine a vehicle interior configuring to a customised layout and shape you have specified. Star Trek style self-repairing clothes and smart materials that can change shape may be closer to reality than we think, thanks to the latest developments in materials science. Whilst 3D printing has captivated the minds of innovators and entrepreneurs for years, it is now beginning to be overshadowed by the latest buzz: 4D printing.
4D printing is the process of producing a 3D multi-material printed part that reacts to external stimuli, such as heat, moisture or sound, over time. It is an area that is beginning to capture the imagination of scientific labs, leading tech vendors and investors.
In 4D printing, material is pre-programmed to have built in sensing and actuating abilities that allow the material to self-transform over time. When exposed to energy from heat, light or moisture, the printed component can morph into the chosen 3D shape. The part can also be returned to its original shape by applying the relevant stimuli.
Skylar Tibbits, the founder of MIT’s Self-Assembly Lab, coined the phrase ‘4D printing’ in his TED Talk on the subject in 2013. Since then, the MIT lab has developed a whole host of working prototypes and dreamt how revolutionary this technique could be in the future.
Smart materials will soon become ubiquitous; they will be found everywhere, from cars that adapt to the local environment, to shoes and clothes that adapt to our bodies. Some of the most disrupted markets will be construction, wearable tech, aerospace, military, healthcare and autonomous vehicles.
Scientists are currently developing self-healing roads that will detect and fix potholes; sports clothes that allow your skin to breathe in warm weather but form a waterproof layer in the rain; and cars that change shape to suit the driving conditions.
How well do you really know your competitors?
Access the most comprehensive Company Profiles on the market, powered by GlobalData. Save hours of research. Gain competitive edge.
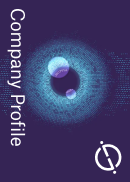
Thank you!
Your download email will arrive shortly
Not ready to buy yet? Download a free sample
We are confident about the unique quality of our Company Profiles. However, we want you to make the most beneficial decision for your business, so we offer a free sample that you can download by submitting the below form
By GlobalDataTibbits believes that 4D printing will transform many industries, as it utilises 3D printing manufacturing techniques but offers us the ability to produce parts that can’t be made in any other way.
Whilst 3D offers an alternative way of producing the same product that might have been created using Computer Number Controlled (CNC) machine or injection moulding, 4D printing allows us to create parts that traditional manufacturing methods cannot fabricate.
4D printing will allow us to access a whole range of functions that we were not able to develop before. It is possible to print non-static, highly intelligent, active parts that can sense and self-transform, without the need for heavy and expensive sensors or motors.
This ability will allow 4D printed products to thrive in the quest to form smarter, yet simultaneously more lightweight products. Removing external electrical components not only reduces cost and weight, but also reduces the potential and tendency for failure, enabling more reliable smart materials.
Using printing to rapidly design and manufacture parts also opens a whole new world of highly customisable complex parts. Smart materials are typically a niche area, and their fixed properties can make them difficult to implement. However, the highly customisable nature of 4D printed parts lends itself to a booming, consumer-focused industry.
Despite these revolutionary applications, 4D printing has many challenges to overcome before we find these products in a mainstream consumer market.
Scalability may prove to be a challenge; whilst the Self-Assembly Lab and other research facilities around the world have produced successful prototypes, no one has yet been able to replicate this on a larger scale. The 4D printing market is still in an early R&D phase, meaning that there is currently no standard process or software for 4D printing, as labs around the world are developing different processes with unique outcomes.
Furthermore, as 3D printing has found, stringent regulations in sectors such as healthcare and aerospace can restrict the progress of scientific development in an effort to protect users from harm or unintended side effects. Given these challenges, commercialisation is at least 10 years away.
Nonetheless, Tibbits believes there are no fundamental hurdles which will thwart this industry, and it is only a matter of time and resources before 4D printing revolutionises our world.
In 2019, the 4D printing market was valued at nearly $65m and is expected to grow on a CAGR (Compound Annual Growth Rate) of 33.2% over the next 6 years, according to GlobalData. This means the market will be worth over $360m by 2025. It is estimated that the military and defence sector currently occupies the majority of the market, and that carbon fibre is the most commonly 4D printed programmable material.
For those dreaming of a 4D printed future, the outlook is extremely promising, with resources, scientists, funding, research applications and academic papers flooding the scene. Tibbits believes that the evolution of 4D printing will prove the springboard for a wider topic – programmable materials.
By helping us to achieve higher functioning, smarter, safer and more productive parts, without compromising on cost or weight, it will not be long before these smart materials revolutionise every aspect of a developing market.
BMW and MIT work on ‘inflatable interiors’
There are potential automotive applications in these new materials technologies, especially in future autonomous vehicles. The BMW Design Department in collaboration with MIT’s Self-Assembly Laboratory have successfully developed printed inflatable material technologies that self-transform, adapt and morph from one state to another.
MIT’s Self-Assembly Lab create a process called “Liquid Printed Pneumatic,” a system that uses air chambers that inflate or deflate in a stretchy material. The designs would be 3D printed and programmed to respond to getting or losing air whenever needed.
The BMW Design Department and MIT’s Self-Assembly Laboratory started their cross-disciplinary study in 2016 with the mutual ambition to push the boundaries of material technologies. BMW’s forward thinking concepts of future interiors that can interact and adapt seamlessly were the starting point of an in depth exploration by MIT’s Self-Assembly Laboratory. This collaboration resulted in the first example of a fully printed inflatable that can be customized to any size or shape. The silicone printed object can change shape depending on the amount of air pressure in the system. The pneumatic controls in the system allow the printed structure to transform into a variety of shapes, functions or stiffness characteristics.
“The outcome of this collaboration manifests that a new material future is imminent,” says Martina Starke, head of BMW Brand Vision and BMW Brand Design at BMW Group. Together with the Self-Assembly Laboratory at MIT, Starke is eager to move away from our current understanding of car interiors as the forces reshaping the nature of transportation are eventually shifting toward a kind of vehicle that defies conventions like front and back seats. “There is no need to lock the car of the future into any particular shape. Interiors could even take on malleable, modular uses,” she says.
After testing various directions on how a visionary interior could take shape, the experts at the Self-Assembly Lab achieved a breakthrough when they managed to liquid print air and water-tight inflatable geometries, like customized printable balloons. With this technology they can produce complex channels and pockets that self-transform. Skylar Tibbits: “We then brought together a number of recent technologies such as Rapid Liquid Printing and techniques from soft robotics to achieve this adaptive material structure. In the past, scenarios like these have often required error-prone and complex electromechanical devices or complex moulding/tooling to produce inflatables. Now we’re able to print complex inflatable structures with custom actuation and tuneable stiffness.”
The collaboration has yielded a three dimensional object which is highly dynamic, morphing its form and function. This meter-scale object exhibits robotic-like transformation from a pneumatic system with seven independent chambers to create different movement patterns. “This adaptive material technology points towards a future of transformable surfaces for adaptive human comfort, cushioning and impact performance,” says Martina Starke.
“The ‘Liquid Printed Pneumatics’ project is a perfect example for a fruitful cross-disciplinary collaboration we’ll see more and more over the coming years, especially at BMW.”