
Lubricants and coolants are critical in engines to minimise the friction between moving parts and ensure temperatures remain at safe levels. High-quality products can prevent mechanical failures caused by overheating, and also reduce mechanical wear and tear.
However, in-service testing for coolants and lubricants presents significant problems that must be addressed to ensure continuity, especially for heavy-duty machinery and vehicles in regular operations. It is essential to obtain accurate results as quickly as possible. Any form of in-service testing requires consistency, reliability and reproducibility, and must be performed on a routine basis.
Too many analysis programmes fall short due to delays in getting samples and results. They can also fail due to not choosing the correct tests and, more importantly, taking samples only when a problem is detected when an escalation is more likely.
In addition, a common mistake is trying to use the same lab processes to analyse both oils and coolants. All too often, a lack of training and the necessary understanding of lubricants and coolants can be a serious hurdle for labs in delivering accurate, reliable results.
“I sometimes see companies using an oil condition monitoring lab and they often do coolant analysis together. But it’s two different kinds of matrices. If you think about mixing water and oil, that doesn’t work,” explains Daan Vijfhuizen, account manager at PerkinElmer’s operations in the Netherlands. “If we want to test the element composition of a coolant, as opposed to a lubricant, we really need a different method of introducing samples into the measurement systems.
“At PerkinElmer, we provide specific automation to keep the fluid path separated. You can use that one machine, the ICP-OES, to do both types of testing. That’s a big advantage we offer,” he adds.
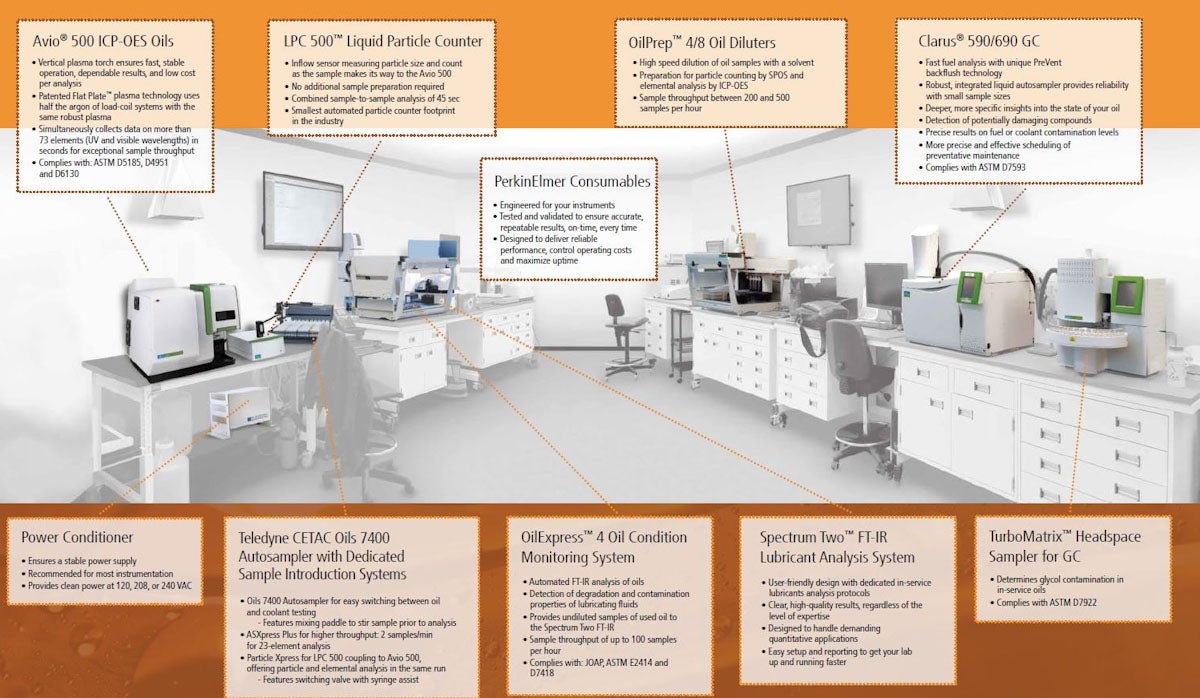
The importance of particle testing
To determine the quality of in-service lubricants, particle counting is a highly effective method.
Particle count tests are commonly used in industrial oil analysis to gauge in-service contamination. Additives to a lubricant can change its composition and viscosity or even deplete over time, reducing its efficiency when used in vehicle engines. Contaminants may come from particles in the ambient air or agents within the machine, such as soot, water, glycol, unburned fuel or chemical degradation.
Yet most automatic particle counting (APC) equipment is not automated and requires labour-intensive analysis of samples. Because of the viscosity and opaqueness of the material, some particle counters may produce irregular particle counts, such as +/-3 ISO codes. The solution is to manually dilute the samples, which is not always practical or cost-effective for a busy lab. However, there are solutions that can help to optimise these processes.
“At a big in-service lubricant laboratory, we checked their particle measurement procedures,” explains Vijfhuizen. “And they were using quite high volumes of lubricant samples. In these tasks you need reproducibility. They used a standard method of particle analysis. With our instrument, we can optimise these procedures while maintaining compliance with the ISO 4406 method thanks to the unique solutions we supply at PerkinElmer.
“Changing them to the optimised procedure of particle analysis decreased the amount of lubricants they needed. This was beneficial for the automation process, because they needed to use these high volumes with samples of thick, heavy-use engine oil. As you can imagine, if you try to pump that into a system it creates some issues, or you need some high volumes to do an effective test.
“We could reduce that sampling size. Plus, we could increase the reproducibility of that testing. That was a major advantage because if reproducibility and deviation are not that high, you can test twice and then release your results. We can do this with our LPC-500TM instrument, where you can combine particle testing with elemental testing in 45 seconds.
“Our systems compile a complete picture of all the elements that are in lubrication oil. We provide the analytical tools. But, most importantly, we also provide the correct testing methods within ASTM and ISO guidelines for directly setting that up. That’s of major importance.”
Optimising lab processes for more efficient lubricant testing
PerkinElmer is actively seeking to increase the efficiencies throughout equipment used for in-service testing of lubricants in lab processes. For example, by combining ICP-OES testing and particle counting analysis in one run, PerkinElmer equipment enables the double-running of samples to reduce the operations footprint.
“The advantage of doing two runs in one is you save time, but you also save the number of samples you use. So, it’s also running more sustainably for samples,” adds Vijfhuizen. “What these labs try to do is like mitigate risk as much as possible.”
A further challenge in testing arises with achieving the necessary high levels of throughput when dealing with the high viscosities present in certain types of lubricants, alongside delivering reproducibility and dependability.
“People in the lab think about throughput, but you need to think about sample sizing as well because there can be heavy fossil-based dilutions used,” says Vijfhuizen. “If you can reduce the size you introduce into a system, basically you’re reducing your footprint.
“We make sure that these labs can deliver the high throughput they need, but also use very reliable and robust methods.”
Download the document on this page to learn more about PerkinElmer’s innovative lubricant and coolant testing solutions.