
Range anxiety is one of the biggest issues facing electric vehicles (EVs), with uncertainty surrounding the distance that can be travelled before recharging is required.
Another concern is the possibility that the battery will combust in the event of a collision. This is because lithium, a highly reactive element most commonly used in the manufacturing of EV batteries, is prone to catching fire in certain conditions.
Every material and component – including anodes, cathodes, binders, electrolytes, and separators – must undergo rigorous testing to ensure they are safe to use and long-lasting. Any flaws can be identified and rectified before being installed on a vehicle.
Analysis tests for Li-ion batteries
Multiple issues need to be taken into consideration when testing battery components. Figure 1 outlines the root cause of potential failures in these components, including the presence of impurities on the cathode or corrosion on the anode, and the types of testing required.
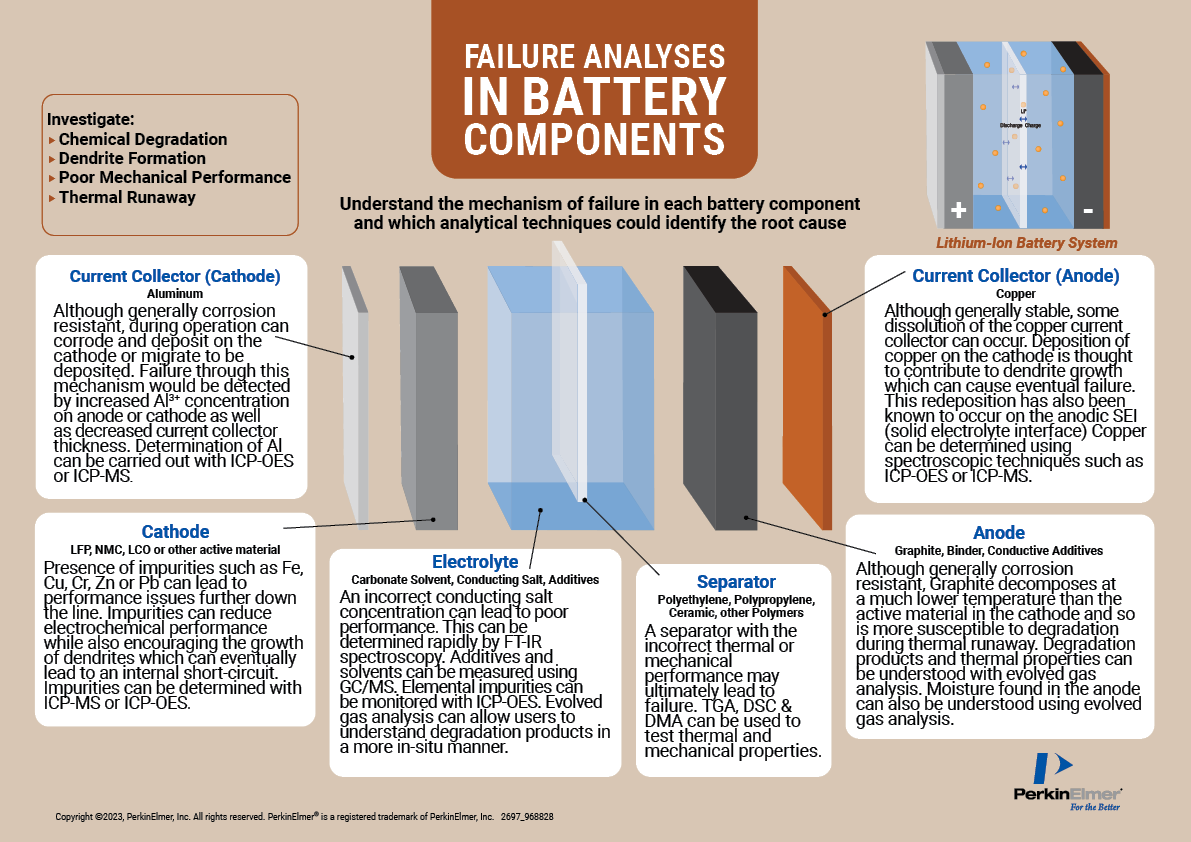
One method of testing is repeatedly cycling the battery to see how it reacts over time. Any issues can then be isolated and identified, and testers can gain an understanding of how the battery operates under different conditions, including the ways these factors affect the battery life.
“Other tests include the nail penetration test. The battery is put into a chamber and penetrated with the nail to see how it would react to being punctured, or in the context of an EV, what would happen if that car crashed,” explains Kieran Evans, senior applications scientist for PerkinElmer.
Battery tests are performed not only on batteries as a whole, but also on the individual components. Differential scanning calorimetry (DSC), for example, allows testers to determine essential thermal properties, such as melting point, glass transition temperature, and other properties that include crystallinity.
Crucially, verifying the quality of materials at an earlier stage is a key factor in determining the performance of components in later operations.
“We have tests that make sure you have the best materials to start with,” adds Evans. “With pure materials, you don’t have impurities that are going to cause problems further down the line. You can use techniques such as inductively coupled plasma-optical emission spectroscopy (ICP-OES), which allow us to find very low-level impurities.
“Using techniques such as inductively coupled plasma-mass spectrometry (ICP-MS), ICP-OES, and DSC, we can really understand the component from the get-go, rather than get to the point where you finished making the battery and find out then that there’s a problem. It’s often useful to check that the materials are of the best quality at the start. And then that way, you can save time, money, and effort.”
Electrolytes in most batteries are a liquid that is often based on organic carbonate solvents. To check that those solvents are pure, testing techniques such as gas chromatography-mass spectrometry (GC-MS) are performed.
Other testing methods include TG-IR-GC/MS, which is a thermogravimetric analysis that involves heating a sample and weighing it to understand weight losses. Coupled with infrared spectroscopy and GC-MS, this allows testers to understand the evolved gases. These tests achieve two things. Firstly, testers can understand what materials are present because different components will evolve at varying times. This is particularly useful when dealing with complex mixtures in batteries. Secondly, it enables testers to establish what happens to these components at high temperatures, which is especially important from a safety perspective.
The future of EV batteries
Lithium-ion batteries are already very efficient. So, what will it take to improve this? In the context of an EV, this may include a longer range, faster charging times, and an extended lifespan.
“There are plenty of factors going into improving efficiency. Different additives in the electrolyte and cathode chemistries, for example, are all being studied,” Evans explains.
“One of the most important tests is to understand how many cycles a battery could go through. This includes cycling it in different ways. Such as if you charge it very quickly, the battery life will be shorter compared to slow charging.”
In addition to developing lithium-ion batteries for improved performance, R&D teams are under pressure to find more efficient ways to manufacture batteries to keep up with high demand. And global demand for EV batteries is widely expected to soar over the coming decade as sales of petrol and diesel vehicles are phased out in several countries, and the supply chain is not yet prepared to meet this surge. Consequently, other battery technologies are being researched and developed.
Alternatives to lithium-ion batteries include sodium-ion – with sodium being far easier to source than lithium at a lower cost; and solid-state batteries, which use a solid electrolyte that might be more expensive than lithium but offers improved safety and performance.
Further down the line, we could see lithium-air batteries in vehicles that use lithium and oxygen from the air to produce a current. While such batteries have been produced on a lab scale, they are not yet a scalable solution to meet global demand.
Ongoing research for new solutions also includes zero-cobalt or low-cobalt batteries, which are increasing in appeal to address the unethical practices that have been exposed at certain cobalt mining sites. In addition, there is a significant focus on recycling batteries to minimise the quantities of raw materials required for production.
With all these new battery technologies in the pipeline, safety testing will be vital to ensure their future success. And PerkinElmer is strongly positioned to provide the necessary testing capabilities.
To learn more about overcoming lithium-ion battery obstacles for the energy transition, download the whitepaper from PerkinElmer below.