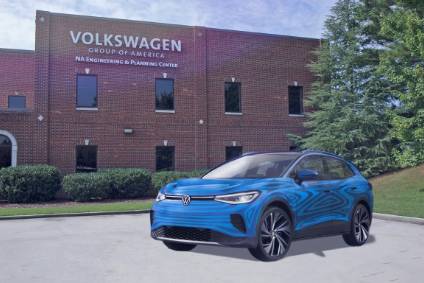
Volkswagen in the US says it has begun expanding its Chattanooga factory to build a North American centre for electric vehicles – not only for assembly, but for engineering future EVs.
Volkswagen’s Engineering and Planning Center (EPC) in Chattanooga will feature a high-voltage laboratory designed to develop and test electric vehicle cells and battery packs for upcoming models assembled in the US.
How well do you really know your competitors?
Access the most comprehensive Company Profiles on the market, powered by GlobalData. Save hours of research. Gain competitive edge.
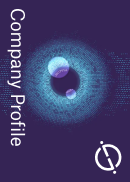
Thank you!
Your download email will arrive shortly
Not ready to buy yet? Download a free sample
We are confident about the unique quality of our Company Profiles. However, we want you to make the most beneficial decision for your business, so we offer a free sample that you can download by submitting the below form
By GlobalDataVolkswagen is planning to use battery cells manufactured by SKI in Georgia for the EVs it builds in Chattanooga.
“There are two ways that auto companies approach the development of electric vehicle batteries,” said Wolfgang Maluche, Vice President of Engineering at Volkswagen of America. “A lot of them will farm out the development and testing of batteries to another company, and some will actually do the work of developing and testing in-house. We are doing the latter.”
The EPC plans to break ground on the lab soon, with the goal of being fully operational by spring 2021. It will feature equipment including pressure testers, explosion-rated climate chambers and a custom multi-axis shaker table (MAST), which is designed to test the integrity of vehicle components in some of the roughest conditions they might face on the road.
Most automotive labs have MASTs, but almost none were designed for electric vehicle batteries, VW says. EV battery packs are the largest and heaviest component in an EV, typically weighing hundreds of pounds and running the width of the vehicle.
“The battery is not only shaking; it is going through a series of harsh conditions to test its durability in a variety of possible environments, from the South Pole to the Sahara,” said Jason Swager, the Director of Electrical Development. “We needed to build a MAST that could withstand the immense force and frequency that we need to test these batteries.”
To run a MAST at such high frequencies, Volkswagen says it had to design its own tool rather than using an outside supplier. The supports for the MAST will be buried 12 feet under the lab’s floor and buttressed with concrete to help withstand the forces in use. Volkswagen’s new lab will be only the second location in the country with a MAST of this size.
Beyond the tools, Chattanooga’s high-voltage lab will have other unique features. In line with Volkswagen’s goal to reach carbon neutrality by 2050, the lab is planned to be built to LEED standards for environmental impacts, through steps such as a battery-to-grid connection that sends unused energy back to utilities.
“This lab was planned to be as sustainable as possible,” said Maluche.
See also: VW starts converting and expanding Emden plant for EVs