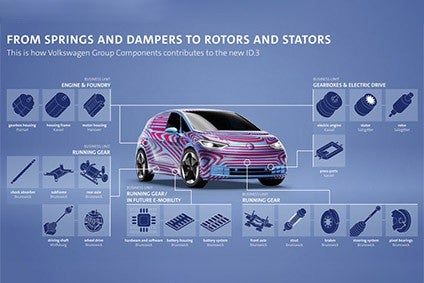
In an unusual move, given that the model is not yet on sale, Volkswagen Group Components (VGC) has detailed some of the “numerous components and parts” it is making for the production ID.3 electric car. Key takeaway: as much as possible is being made in-house for this key new designed-as-electric model built on the MEB platform destined to underpin numerous future VW Group models.
Though VW last May opened customer pre-ordering for 30,000 ‘first edition’ models, series production of the cars at Zwickau has yet to start and vehicle and component output is still at pre-series stage. Group factory-made parts include front and rear axles, steering system, brakes, battery system and the complete electric driveline.
Core electric car components are developed and produced at various VGC plants: electric drive from Kassel, Salzgitter supplies Hessen with rotors and stators, Brunswick develops and produces the battery system, other sites ships castings and other parts.
“We are concentrating on modifying our plants to manufacture new products for electric vehicles. Certain plants are being specialised and we are making use of the synergies through the manufacturing of components within the group,” said VGC chairman Thomas Schmall.
Electric drive key for Kassel
Kassel supplies electric drives and platform parts for the ID.3 and has produced dual clutch automatic gearboxes (DSG) for 16 years.
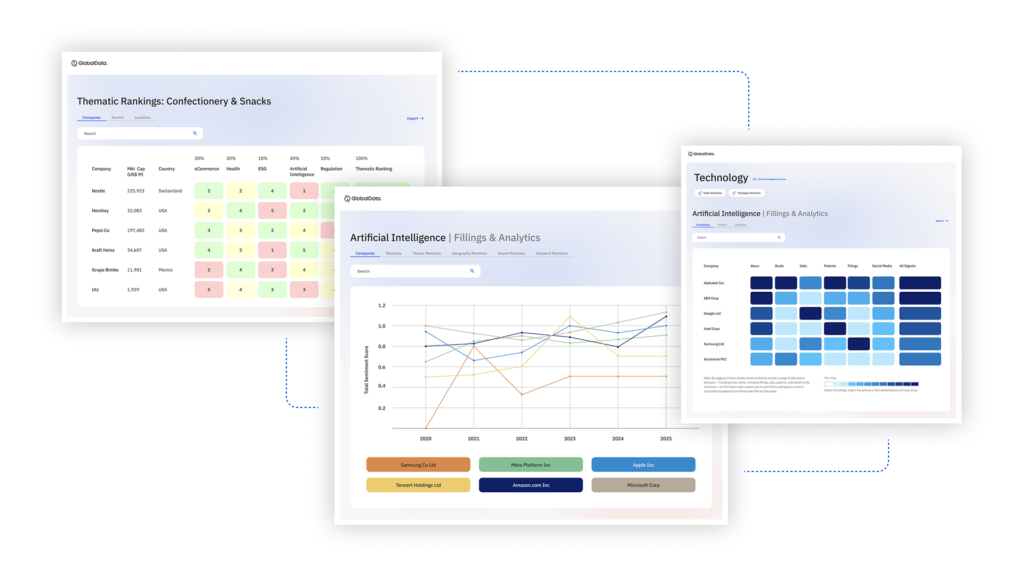
US Tariffs are shifting - will you react or anticipate?
Don’t let policy changes catch you off guard. Stay proactive with real-time data and expert analysis.
By GlobalDataNow the plant will mostly produce electric drives for the MEB platform. All parts are assembled there using parts from Salzgitter, Poznan and Hanover.
Kassel produces electric drives for all MEB vehicles built in Europe and North America (VW has plants in the US and Mexico). After the pre-series stage, up to 500,000 units will be made each year. Kassel works closely with the Chinese plant in Tianjin where the electric drive is produced in parallel for the local market cars built by the various FAW and SAIC joint venture assembly plants.
The two supplier plants will produce up to 1.4m electric drives a year from 2023.
This means, VW noted, VGC will become one of the largest global manufacturers of electric vehicle drives.
Kassel also makes load-bearing components and body parts for the ID.3: parts of the durable frame for the battery box, damper mounts, crossmembers and the tunnel. These parts are delivered to Zwickau for body assembly.
Salzgitter rotor and stator
Salzgitter now specialises in rotors and stators, the two fundamental parts of an electric drive, in addition to conventional ICE engine production. It will eventually make up to 2,000 rotors and stators each day, along with petrol, diesel and CNG drivelines. New ‘hairpin’ technology is used to manufacture stators, a process VW developed to shorten production times.
VGC has taken on group end-to-end responsibility for EV batteries, starting with research and ending with recycling. Salzgitter has a battery expertise ‘centre of excellence’ (CoE) and will open a pilot battery plant by the end of 2019. This will be followed by a pilot recycling plant in 2020.
Brunswick batteries
The ID.3 battery system will be made at Brunswick. A new hall the size of nine football pitches will be built specially built especially for manufacturing the battery system, which VW says “looks rather like a chocolate bar”. It is scheduled to open in Q4 2019. Around 2,000 units will be produced a day and delivered to vehicle assembly at Zwickau. Brunswick site has been developing battery expertise since 2013 and currently makes systems for current VW brand electric and hybrid vehicles plus Scania and MAN trucks.
MEB battery systems that have already been manufactured are currently undergoing several weeks of hardness testing, and are being put through trials with results to be incorporated into the further development.
Brunswick also makes running gear components and assembles front and rear axles. This includes welding groups and steering systems plus drive shafts from the running gear production site in Wolfsburg.