Volkswagen Design has completely changed its working methods over the past two years as it goes digital.
Work is now consistently carried out digitally which significantly increases the efficiency of individual work steps and facilitates collaboration across locations. The new processes also give employees much more room for personal and professional development.
"Above all, the ongoing staff training and software optimisation lead to an increase in employee satisfaction, in addition to a faster pace of development and a higher product quality", said design chief Klaus Bischoff. "Digitalisation is alive in design – and this is something that employees also benefit from: the new processes open up exciting prospects for personal development."
Investments have been made in extensive high-end presentation systems – such as an 18-metre wide high-resolution LED screen for the acceptance of virtual models. One advantage of this is that the cost- and time-intensive production of clay models during the process is drastically reduced, as these can now be virtually displayed and optimised. The results are impressive: the reduced and more targeted use of physical presentation models has led to savings in the tens of millions of euros since mid-2016.
Virtual Reality (VR) and Augmented Reality (AR) also have an important role to play. A recent development is the introduction of high-resolution data glasses; these enable new product visions to be created, jointly developed and evaluated in photorealistic quality by several people simultaneously at each of the virtually simulated sites around the world.
The new design opportunities primarily make it easier for designers to work together with other development partners. This allows engineers, such as those specialising in aerodynamics, to be integrated into the process, which ultimately benefits creativity and product maturity. The prerequisite is a powerful IT infrastructure that enables real-time collaboration across national borders.
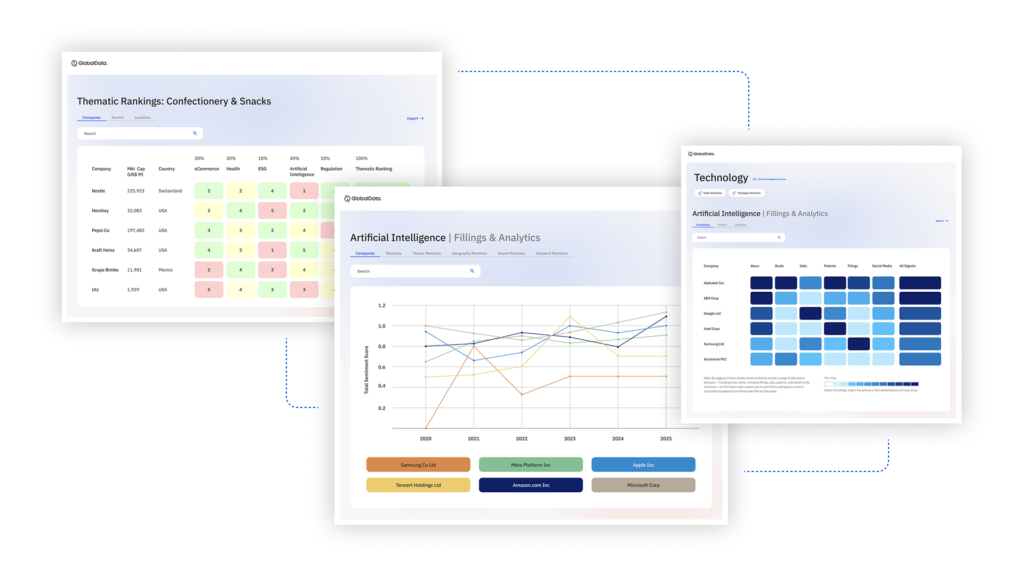
US Tariffs are shifting - will you react or anticipate?
Don’t let policy changes catch you off guard. Stay proactive with real-time data and expert analysis.
By GlobalData