The Volkswagen brand is aiming for a 30% increase in productivity worldwide by 2025 compared to 2018.
VW says the 'TRANSFORM.TOGETHER' production strategy with its eight central action areas lays down the roadmap for leveraging existing efficiency potential and achieving a sustained increase in productivity. The strategy appears to be based on simplified structures and processes, with new measures and KPIs across the sprawling manufacturing network.
"Volkswagen is currently in the midfield compared with our most important competitors when it comes to production and labour costs as well as margins, making overdue investments more difficult. Our processes and structures are too complex," said Dr. Andreas Tostmann, the Volkswagen Brand Board Member for Production.
"And there is also room for improvement in standardizing our global production network. That is why we are now introducing uniform structures at all factories along with uniform and comparable key performance indicators. In production alone, we have efficiency potential of €2.6 billion through 2025," Tostmann added.
VW said that 'production is therefore making a major contribution to achieving the profitability target of over 6 percent for the brand'.
"We want to rank among the best for productivity. We need to generate competitive returns to enable us to make key investments in the future and thus safeguard today's jobs tomorrow and beyond. Together, we are ushering in a new era in Production for the Volkswagen Passenger Cars brand. This is about nothing less than a paradigm shift: from a product-oriented company to a production-and process-oriented company. For Production, that means our department will be more important than ever going forward," Tostmann said.
How well do you really know your competitors?
Access the most comprehensive Company Profiles on the market, powered by GlobalData. Save hours of research. Gain competitive edge.
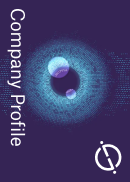
Thank you!
Your download email will arrive shortly
Not ready to buy yet? Download a free sample
We are confident about the unique quality of our Company Profiles. However, we want you to make the most beneficial decision for your business, so we offer a free sample that you can download by submitting the below form
By GlobalDataTostmann was speaking at an event held at the Berlin Motorwerk location attended by 500 managers from Volkswagen's 17 vehicle manufacturing plants.
The action areas of the production strategy
In order to realize these ambitious goals, Volkswagen Production has defined eight main action areas containing concrete measures to drive the progress of the production strategy at all Volkswagen sites:
- Productivity
- Team of the future
- Rework-free products and processes
- Sustainable structures
- Stable sales order process
- Ramp-up excellence
- Low-expenditure factories of the future
- Think Blue.Factory
VW said that process and production optimisation plays a key role in the success of the strategy in all action areas. Complexity is being significantly reduced. "Our factories must become faster, leaner and more efficient: in terms of factory costs per vehicle, investments in new resources and products, as well as hours per unit, i.e. the number of hours spent by production and non-production-related units on building a vehicle. We will be making massive reductions in factory costs and investments, for example by reusing existing resources and factory structures and through systematic standardisation. That is how we will be cutting investment by €1.5 billion compared with today's level," Tostmann said.
The brand has targeted a 45% improvement in environmental KPIs at its sites compared to the reference year of 2010. As Andreas Tostmann explained: "The improvements in resource efficiency through Think Blue.Factory have also already achieved savings of €130 million since 2010. On average, there has already been a 30 percent decrease in key environmental indicators. Our long-term goal is 'zero impact': CO2-neutral production."