
Volkswagen claims its new six-speed manual, the MQ281, saves up to 5g of CO2 per kilometre, compared with previous transmissions, depending on the engine-gearbox combination.
It went first into the Passat but will be used by most VW Group brands.
SEAT Components has started production of the new transmission and has capacity for 450,000 units a year.
“Nobody took much notice of manual gearboxes until now,” VW said in a statement, apparently referring to the huge advances of recent years in alternative automatic transmissions such as robotised manuals, dual-clutch pre-selectors (like the group’s own DSG) and CVTs.
“However, only slight modifications were sufficient to improve efficiency and consumption with a huge impact on emissions and the environment.
“Although they function unobtrusively, manual gearboxes have a significant share of the gearbox market worldwide due to a high installation rate.”
How well do you really know your competitors?
Access the most comprehensive Company Profiles on the market, powered by GlobalData. Save hours of research. Gain competitive edge.
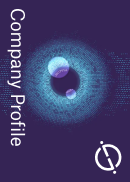
Thank you!
Your download email will arrive shortly
Not ready to buy yet? Download a free sample
We are confident about the unique quality of our Company Profiles. However, we want you to make the most beneficial decision for your business, so we offer a free sample that you can download by submitting the below form
By GlobalDataThe trend towards vehicles from the SUV segment with large-diameter wheels places high demands on the gearbox, the automaker said.
“With the MQ281, we have developed a highly efficient manual gearbox that reliably meets these demands – and is soon to be introduced into a number of vehicle classes in the volume segment,” said gearbox and 3WD development chief Helmut Goebbels.
The MQ281 has a torque range of 200Nm to 340Nm so completely or partially supersedes the current VW MQ250 and MQ350 gearboxes.
It is based on a 2.5 shaft concept and boasts a high gear spread of 7.89 maximum. This guarantees good launch performance – even for heavy vehicles with large wheels – and facilitates ‘downspeeding’ – (fuel-saving) driving in high gears with low engine speed.
Development focused primarily on improving efficiency.
“Here we employed virtual development methods,” said Goebbels.
“This enabled us to design a completely new oil conduction system. Using a variety of oil conduction measures, we are able to achieve a uniform and optimum lubrication of gear wheels and bearings, reducing the amount of lifetime oil required to just 1.5 litres.”
To further reduce friction, a bearing concept adapted to the gearbox was developed. The design used friction-minimised bearings with low-contact seals.
Material use and its distribution for the gearbox housing was also optimised. With the aid of a further virtual development tool, a strength-optimised housing structure could be designed. The new housing supports current noise requirements (avoidance of undesired secondary noises) and ensures improved driving comfort through less audible and noticeable vibrations in the vehicle.