Material’s ability to reduce weight and improve performance encourages growth
The use of bar steel in crankshafts will increase by as much as 50 percent, from 40 to 60 percent of the market share, by mid-2002 because of the material’s capability to improve engine performance and reduce weight, at economical costs, according to a recent study by American Iron and Steel Institute (AISI) Bar and Rod Market Development Group (BRMDG). This growth would be at the expense of cast iron, which currently possesses 60 percent of the crankshaft market.
The BRMDG initiated the study, “Steel’s Technical and Economic Progress in the Production of Lighter and Smaller Engine Components,” in 1998 in response to the automotive industry’s quest to increase fuel economy, reduce costs and weight, and improve customer satisfaction. The report provides an in-depth look at how crankshafts produced from bar steel forgings contribute to achieving these goals.
Additionally, the report explains that this potential increase in steel market share is due to innovative steel forming and processing technologies that have advanced the state of the art during the past decade.
“This study points to the continued realization that steel is the material of choice for the many challenges facing automakers today, including engine applications,” said David Anderson, manager Bar and Rod applications, BRMDG. “With innovative technologies and modern engineered steels, the steel industry is helping automakers produce lighter vehicles that achieve improved performance at economical costs.”
Improved Performance:
How well do you really know your competitors?
Access the most comprehensive Company Profiles on the market, powered by GlobalData. Save hours of research. Gain competitive edge.
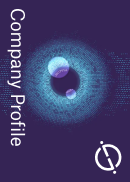
Thank you!
Your download email will arrive shortly
Not ready to buy yet? Download a free sample
We are confident about the unique quality of our Company Profiles. However, we want you to make the most beneficial decision for your business, so we offer a free sample that you can download by submitting the below form
By GlobalDataAn engine crankshaft attaches to connecting rods, which fastens to pistons, and transfers engine power to the transmission. Forged steel crankshafts offer a host of benefits compared to cast iron units including greater durability, improved Noise Vibration Harshness (NVH) characteristics and higher load-bearing capacity for torque at lower engine speeds (RPMs), resulting in fuel efficiency improvements.
These benefits are the result of steel’s unique mechanical properties, such as a high ratio of yield point to tensile strength, which determines the degree of rigidity and elasticity. Compared to cast iron units, these properties of forged steel crankshafts provide a higher level of rigidity and fatigue which provides better intrinsic dampening, enabling the engine to run more smoothly, resulting in less vibration, less noise and, thus improved customer satisfaction.
Additionally, better mechanical properties contribute to higher static and dynamic rigidity which results in a higher load-bearing capacity for torque at lower RPMs. Static and dynamic stiffness reduces distortions and lowers the excitation energies from moving engine parts, ensuring significant fuel consumption savings because the engine is producing the same output at a reduced effort.
Automakers currently using forged steel crankshafts include: Ford Motor Co., DaimlerChrysler, Honda, British Leyland, Saab, Volkswagen, Mitsubishi and Volvo.
Lightweight:
As automakers strive to reduce weight in vehicles, the powertrain continues as a key focus in helping achieve that goal. Using forged steel-in place of cast iron-reduces the mass of the crankshaft by eight percent according to Krupp Gerlach, an automotive component manufacturer that recently completed a study demonstrating the benefits of forged steel compared to cast iron crankshafts in an actual series production engine. The crankshaft’s total length is also reduced by nine percent as a result of steel’s unique mechanical properties, particularly the ratio of yield point to tensile strength.
This reduction in size and weight offers engineers greater design latitude, resulting in more efficient use of space and material. Vehicle makers correspondingly can reduce the size and mass of other powertrain components, such as bearings and pins, further reducing weight, boosting fuel economy and improving performance.
Costs:
The new generation of steels, including vanadium microalloys and Air-Cooled Forging Steels (ACFSs), features improved strength and fatigue properties, enhanced machinability and greater consistency due to specific, controlled testing processes (sensitive to defects) performed during each production phase. These improvements enable forgers to produce crankshafts that are near-net shape, reducing production cycle and try-out times and, in turn, costs as there is less need for machining and rework.
Additionally, the development of ACFSs has eliminated the need for heat treating, further reducing the forged component costs. Using highly controlled heat processes, ACFSs eliminate hot and cold spots on the steel bars, providing greater product consistency, with more uniform grain size and microstructure. As a result, these steels have increasingly replaced heat-treated steels in crankshafts and other powertrain applications.
Benefits vs. costs:
Modern engineered steels, coupled with innovative processing and forming technologies, have significantly decreased the manufacturing costs associated with producing forged steel crankshafts. The strides made to reduce these costs continue to boost steel’s position as an economical material for use in engine crankshaft applications. In addition to reduction in costs, steel is a viable material for engine crankshaft applications because of the multitude of benefits it offers, including:
Light weight
High performance
Greater torsional stiffness
Improved NVH characteristics
Greater durability
Net or near-net shape
Less machining
Less or no rework
Lower rejection rates
Greater consistency and product repeatability
Inspection simplicity
Fewer warranty claims
Improved customer satisfaction
“As the steel industry continues to make technological advancements, forged steel crankshafts will improve in quality, performance and cost making them even more viable for engine applications,” said Jürgen Kneller, author of the study.
To obtain a copy of this study, contact Dr.-Ing Jürgen Kneller, at J.Kneller@gmx.de or David Anderson, manager Bar and Rod Applications, AISI at (248) 945-4764. To learn more about the BRMDG, visit steel.org.
Under the auspices of the American Iron and Steel Institute, the Bar and Rod Market Development Group strives to grow the market for value-added steel bar and rod products. The Group pursues this goal through two task forces committed to developing innovative solutions to the challenges facing their clients and the steel industry. These task forces include:
Automotive/Heavy Equipment
Construction/Infrastructure
Learn more about the Bar and Rod Market Development Group at www.steel.org.
Bar and Rod Market Development Group member companies:
Chaparral Steel
Charter Manufacturing
CSC, Ltd.
GS Industries
Keystone Consolidated
Ispat Inland Bar Company
Ispat Sidbec, Inc.
MACSTEEL
North Star Steel Company
Republic Technologies International
Slater Steels, Inc.
Stelco Inc.
The Timken Company
To link to a related feature article, please click here.