A new $US16 million safety-testing facility will help get vehicles on the road eight to 10 months faster as part of a broader, $US65 million endeavour by Ford to trim expenses and adapt more quickly to the fast-changing market, the Associated Press (AP) reported.
Ford now takes about 28 months to get a vehicle to market once the design is complete but the automaker wants to cut that to 18 months by mid-2007, putting it on par with competitors like Toyota, Ford vice president for product creation Phil Martens told AP.
The news agency noted that, earlier this summer, General Motors announced a similar effort to streamline and improve safety testing – it is investing $33 million in its crash-testing facilities, including $10 million for a rollover lab expected to be complete by late 2006.
Chrysler spokesman Max Gates told the Associated Press each of the Big Three wants to get development time down to 18 months – he added that Chrysler now takes less than 25 months.
“We’re working real hard on that because we have an increasingly demanding customer base that wants to see new stuff all the time,” Gates reportedly said.
How well do you really know your competitors?
Access the most comprehensive Company Profiles on the market, powered by GlobalData. Save hours of research. Gain competitive edge.
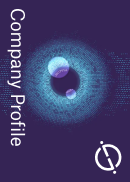
Thank you!
Your download email will arrive shortly
Not ready to buy yet? Download a free sample
We are confident about the unique quality of our Company Profiles. However, we want you to make the most beneficial decision for your business, so we offer a free sample that you can download by submitting the below form
By GlobalDataMartens told AP that Ford is spending $65 million to upgrade vehicle-testing facilities – it’s revamping test tracks and has equipped 8,000 engineers with new mobile phones and wireless laptops so they can move more freely between labs and test tracks.
Martens reportedly wouldn’t reveal how much money Ford will save because of the upgrades but said they will shave up to 60% off the cost of vehicle production.
According to the Associated Press, Ford says the new safety-testing lab near its Dearborn headquarters has one of the most advanced crash simulators in the world – the simulator consists of a vehicle interior set inside a rigid frame and attached to a fast-moving hydraulic sled.
The simulator allows Ford to see what would happen to the interior of a vehicle in five different types of crashes – including frontal and side impact – without actually having to destroy an expensive prototype vehicle, AP added.
Ford reportedly said the new sled will allow it to conduct 10 tests each day, compared to two each day with its current machines. It tests finished vehicles at a separate location.
Ford’s new facility has a separate lab where engineers can test how well vehicles prevent head injuries. In that lab, a mechanical arm slams the heads of crash test dummies into the side of the vehicle at different speeds and angles, AP said.
Ford also has a lab that simulates what happens when occupants aren’t wearing safety belts or are sitting very close to the steering wheel, the report added.
Martens said Ford began testing its new development process with the 2006 Ford Fusion sedan, which will be in showrooms this autumn. The company took about 25 months to develop the base model of the Fusion, he told the Associated Press.