Building on more than 20 years of automotive experience and the power of its market-leading ADAMS® functional virtual prototyping software, Mechanical Dynamics, Inc. (Nasdaq: MDII – news) has developed the Functional Digital Car(TM) concept, offering automotive manufacturers and suppliers the ability to reduce the costs, time, and risks associated with vehicle product development.
Vehicle performance
can then be simulated in a virtual test lab environment or on a virtual test
track to replicate real-world behavior. The vehicle can also be integrated with
hardware-in-the-loop simulations to investigate the real-time behavior of the
vehicle with real subsystems such as anti-lock brakes and traction control systems.
Design attributes can be evaluated and optimized, and the results shared among
engineering teams globally.
"This is the technology that will drive the improvements all vehicle manufacturers
are striving to meet — shorter development cycles, enhanced performance, innovation,
managed risk, and lower costs,” said Robert R. Ryan, president of Mechanical
Dynamics. "We see the Functional Digital Car as the common framework for
integrating various computer-aided engineering technologies across the development
process at all levels of management, within both the OEM and the supply chain.
We’ve taken Mechanical Dynamics’ expertise in automotive functional virtual
prototyping, partnered with industry leaders in other areas of computer-aided
design, and developed a technological approach that stands ready to meet the
challenges of this rapidly changing industry.”
Using the current BMW 3 series as an example, Ryan pointed out that this much-heralded
car required five-and-a-half years, 2.6 million man-hours, 130 handmade system-level
prototypes created at a cost of roughly $350,000 per vehicle, and some 2,400
new components.
"But with the pace of change in this industry, most people believe the
standard of excellence set by the BMW 3 series will be surpassed in just a few
years,” Ryan said. "Vehicles will ride smoother, handle better, operate
with less noise, and offer more comfort and safety. And yet industry experts
say that these upcoming vehicles will be produced to meet those requirements
in roughly half the time. How can this be accomplished? It can only be done
with functional virtual prototyping at the core of vehicle development.”
How well do you really know your competitors?
Access the most comprehensive Company Profiles on the market, powered by GlobalData. Save hours of research. Gain competitive edge.
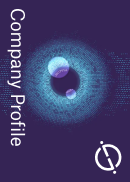
Thank you!
Your download email will arrive shortly
Not ready to buy yet? Download a free sample
We are confident about the unique quality of our Company Profiles. However, we want you to make the most beneficial decision for your business, so we offer a free sample that you can download by submitting the below form
By GlobalDataRyan noted that ADAMS is already the de facto standard for functional virtual
prototyping in the automotive industry, used by every major automotive manufacturer
and an increasing number of their suppliers. "Bringing OEMs and suppliers
together to work from a common model and shared data is a critical component
of the Functional Digital Car concept,” he said. "Integrating the technology
used by both groups is absolutely necessary to speed development while gaining
improvements in the quality of the finished product.”
At a recent "Smarter to Market” Executive Forum sponsored by Mechanical
Dynamics in Novi, Mich., representatives from OEMs and suppliers discussed the
role of functional virtual prototyping in their companies and the industry.
Glen Moore, supervisor of CAE methods at Ford Motor Company, Advanced Engineering
Center, said, "The development process needs to be retooled. It needs to
be re-outfitted and focused more toward the virtual prototype instead of a hardware-based
system. Physical prototypes must be replaced by virtual prototypes. That’s the
way the industry is headed.”
Paul Riehle, director of NVH and CAE at Roush Industries, said, "We’ve
implemented the functional virtual prototype to accelerate the development process,
ultimately trying to produce a more functional concept car. That’s helped improve
the quality of the vehicle.”
"Reducing cost is a major objective for auto manufacturers and all Tier
One companies such as Visteon,” said Rohintan Deputy, director, Advanced Manufacturing,
Engineering Tools and Process Development, Visteon Corporation. "We want
to be faster to market. We want to have fewer and fewer prototypes, but at the
same time we do not want to sacrifice quality at Job One. That’s why virtual
prototyping and computer-aided engineering comes in very handy. We want to have
better products.”