The first, new 2001 Chrysler Sebring Convertible rolled off the production line at DaimlerChrysler Corporation’s (DCC) Sterling Heights Assembly Plant (SHAP) today, and thanks to manufacturing synergies with Mercedes-Benz the company was able to avoid $100 million in production costs during the launch.
By installing the same flexible conveyor system at SHAP that is used in some Mercedes-Benz manufacturing facilities, DCC was able to assemble the new convertible on the same line as the Chrysler Sebring and Dodge Stratus sedans, rather than having to expand the plant and adding a new, separate assembly line.
“This is only the beginning of more manufacturing synergies yet to come,” said Gary Henson, DCC Executive Vice President – Manufacturing. “As we move forward and introduce more products, we will continue reaping tremendous synergies in manufacturing, while maintaining the distinct attributes of our specific brands.
We continue to benchmark our facilities worldwide for best practices and have saved millions of dollars in increased purchasing power, shared technologies and efficiencies throughout our global manufacturing network.”
The initiative came from one of many benchmarking visits after the merger between Daimler-Benz and Chrysler Corp. German team members who assemble the Mercedes-Benz SLK and SL convertibles at the company’s Bremen Assembly Plant in North Germany have supported the development and production launch of the new Chrysler Sebring Convertible at SHAP.
Earlier this month DCC announced it would produce a Mercedes-Benz developed transmission at its Indiana Transmission Plant (ITP) in Kokomo, Indiana — the first example of component sharing between Mercedes-Benz and Chrysler products since the merger. DCC will expand ITP by 600,000 square- feet where it will build the Mercedes-Benz “W5A580” transmission for use in future Chrysler, Dodge and Jeep products. The five-speed, automatic, rear- wheel drive transmission, currently built in the company’s Hedelfingen plant just outside Stuttgart, is used in the current Mercedes-Benz S, E, C and M-Class vehicles.
Skillet Conveyor At SHAP
How well do you really know your competitors?
Access the most comprehensive Company Profiles on the market, powered by GlobalData. Save hours of research. Gain competitive edge.
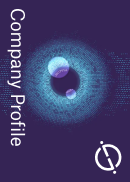
Thank you!
Your download email will arrive shortly
Not ready to buy yet? Download a free sample
We are confident about the unique quality of our Company Profiles. However, we want you to make the most beneficial decision for your business, so we offer a free sample that you can download by submitting the below form
By GlobalDataPrior to the convertible launch at SHAP, the overhead vehicle carrier in the assembly area could not accommodate the convertible, as there was not enough room for roof installation. Part of the ongoing benchmarking with the Mercedes-Benz plants yielded a best practice that works particularly well with convertibles — the use of an adjustable skillet conveyor in final assembly.
A skillet conveyor is a closed-loop, friction-drive conveyance system with a floor-level palette carrying each vehicle. The height of each palette is adjustable, and can be programmed to a particular height, throughout the process. Not only does this free the space to assemble the convertible, more importantly, this kind of conveyor is more ergonomically sound for operators. Each palette can be customized for each product, each station, and operation. SHAP installed the skillet conveyor for this launch, and to increase its flexibility for future launches. It is the first Chrysler group plant to use a skillet conveyor.
DaimlerChrysler has been preparing SHAP for the arrival of the Sebring Convertible from the Toluca, Mexico plant, which is now exclusively devoted to the Chrysler PT Cruiser. Rather than assemble the convertible in a separate area, as it was done in Toluca, the company optimized each station and process in order to accommodate the complexity of both the sedan and convertible. This had to be done using the same amount of space and the same manpower.
The launch team worked with colleagues from Mercedes-Benz and the local union to optimize each process, re-assign and train the workforce, and re-configure material flow, resulting in about 50 percent more work accomplished in the same space.
SHAP employs about 3,000 team members and at full capacity will be able to produce 300,000 units annually on a two-shift operation. The plant has the ability to adjust the model mix produced based on demand.
Quality at SHAP
Through continuous improvement processes, and its experience in using the Operating Principles, SHAP and its workforce have a reputation for producing high quality vehicles at low cost. In fact, the former Plymouth Breeze, which was on the same platform as the 2000 MY Dodge Stratus and Chrysler Cirrus, was the only domestic brand to win a first place JD Power IQS 2000 award. These vehicles were three of the top four vehicles ranked in the JD Power midsize segment. SHAP was one of many plants benchmarked by the worldwide DaimlerChrysler manufacturing group in developing best practices for the companies Operating Principles, the comprehensive system it uses to produce vehicles. To ensure quality, the SHAP verifies parts, processes and fit and finish every step of the way — from stamping and body, to paint and final assembly.