To help North American automotive manufacturers develop and validate laser welding and assembly techniques, Lamb Technicon Body & Assembly today announced the dedication of a new Laser Process Validation Center.
The 2,000-sq.-foot center, located within Lamb’s Modern Prototype facilities in Troy, is believed to be the first in North America to integrate both laser processing and prototyping services at a single facility. As a result, time to market for laser-processed part concepts can be substantially improved, claims Jim Tobin, President, Lamb Technicon Body & Assembly.
“Lamb’s new center will provide the automotive and truck manufacturing communities with an important, time-saving resource to accelerate the validation process for laser-processed parts,” said Tobin. “More importantly, we can transform digital design data of body components into stamped, laser-welded assemblies in as few as eight days. Customers can quickly make manufacturing decisions based on real-life data from actual parts and actual manufacturing processes. This in-house capability gives Lamb customers a unique advantage for integrating laser technology into their body assembly operations.”
Laser welding is a relatively new alternative to conventional (electrical or resistance) welding for assembling metal auto and truck body parts. Although used by European auto companies since the mid-1980s, the practice has yet to catch on with North American-based automakers.
“We support Lamb’s leadership in this laser application center,” said Curtis R. Nichols, President, Rofin-Sinar, Inc., a manufacturer of a complete line of industrial lasers. “This full prototype facility gives North American manufacturing companies the opportunity to validate complete processing requirements before production equipment decisions are finalized.”
“European manufacturers already realize the benefits of laser-processed parts including greater part throughput, process flexibility, improved body component stiffness and lower vehicle weight,” said Andrew Dodd, North American Product Manager for GSI Lumonics, Inc., a manufacturer of industrial Nd.-YAG lasers. “We believe this center can now allow North American producers to rapidly close the gap and achieve similar benefits.”
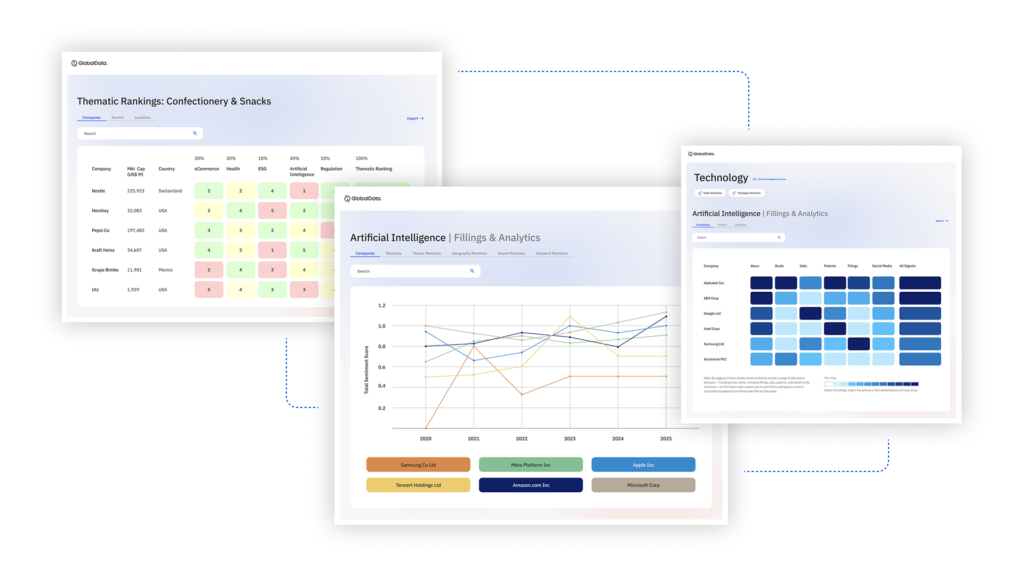
US Tariffs are shifting - will you react or anticipate?
Don’t let policy changes catch you off guard. Stay proactive with real-time data and expert analysis.
By GlobalDataLaser welding can be faster than conventional resistance welding, allowing vehicle makers to process parts more quickly, and changeover manufacturing lines more rapidly. Lasers can also produce single-sided welds in both aluminum and steel, allowing bonding of metal skins onto roll-formed or new hydroformed tubular parts, such as those used in vehicle chassis.
Finally, laser welds require less surface area to achieve the same joint strength as resistance-welded parts. This allows manufacturers to join parts together with smaller “flange” areas, reducing part weight to improve vehicle fuel economy.
Lamb’s new application center will utilize several Rofin-Sinar lasers, and a GSI Lumonics 4 kilowatt Nd.-YAG laser with fiber optic beam delivery, plus robotic handling equipment from ABB and Nachi.
Lamb Technicon Body & Assembly Systems designs, integrates and builds vehicle body and assembly equipment including robotic welding and hemming systems. It also provides complete sheet metal prototyping services for automotive and truck body components, and contract engineering services.
UNOVA is a leading $2.1 billion global supplier of manufacturing technologies and integrated production systems for the global automotive, aerospace and heavy equipment industries. It is also a leading provider of wireless networking technologies and mobile information systems solutions for supply-chain execution and e-commerce fulfillment.