General Motors’ productivity improved 4.5% last year while Ford dropped to just a 3% improvement and DaimlerChrysler was up just 2.7%, ranking last among six major car makers rated, the annual Harbour Report said.
The Harbour Report, first published in 1989 by the Troy, Michigan-based consultancy and released yesterday, measures assembly, stamping and powertrain productivity and rates North American vehicle makers on their assembly efficiency by dividing the number of vehicles produced in a factory by the number of hours worked by every worker from top executive to floor cleaner.
Foreign-owned manufacturers Nissan, Honda and Toyota continued to have the most productive assembly, stamping and powertrain manufacturing operations in North America in 2001 but the gap with domestic challengers continued to narrow, the report said.
Nissan led all 10 companies in the report in overall assembly productivity for the eighth consecutive year with an overall HPV measure of 17.92. The plant’s car line finished second overall in the car assembly rankings, and its truck lines finished 1-2 in truck productivity. However, while Nissan’s assembly performance at its operation in Smyrna, Tennessee, may have bested the other 10 participants, the plant’s overall performance degraded 3.2% in 2001, reflecting the launch work required for the new Altima.
Honda was second in assembly productivity and first in engine productivity. And Toyota finished second in engine productivity, and led several categories across stamping’s basket of measures.
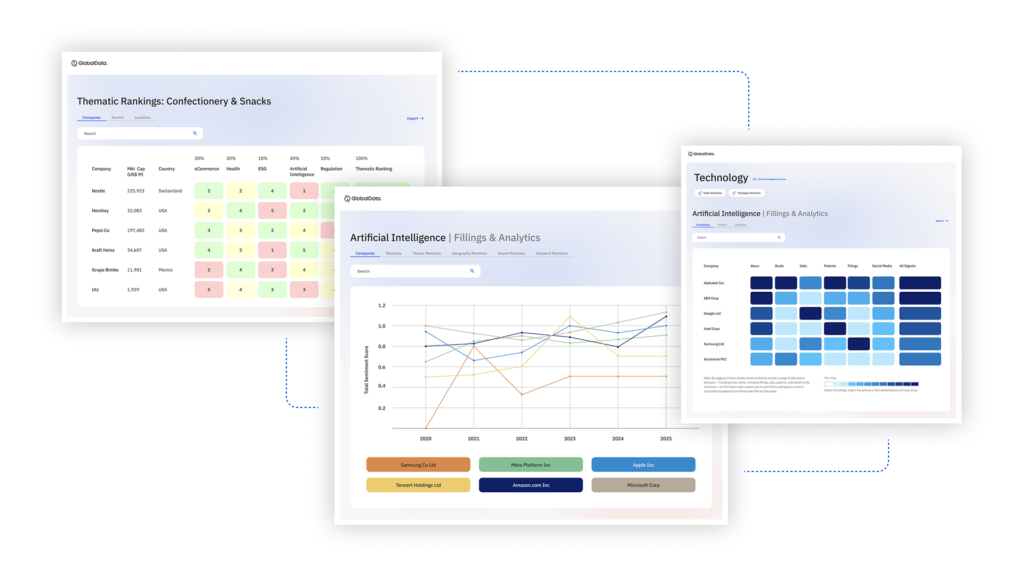
US Tariffs are shifting - will you react or anticipate?
Don’t let policy changes catch you off guard. Stay proactive with real-time data and expert analysis.
By GlobalDataGeneral Motors, with a 4.5% overall improvement, led the domestic manufacturers in assembly, engine and transmission productivity, which marked the first time in the history of the Harbour Report that GM finished ahead of Ford in the assembly and overall hours per vehicle (HPV) measures.
General Motors produced some notable achievements in assembly manufacturing. Three GM car plants – Lansing C (in the Compact segment), Oshawa #1 (Midsize) and Detroit-Hamtramck (Luxury) – led their respective segments, as did three of the company’s truck plants – Arlington (Full-Size SUV), Oshawa (Full-Size Pickup) and Doraville (Minivan).
Seven of the 10 most improved plants were GM operations, led by Flint Assembly, which was the most improved plant in the report. After moving ahead of Ford and Auto Alliance, GM finished sixth overall in the company productivity rankings. In the last two years alone, GM has improved its HPV by nearly four hours.
“Harbour has been charting GM’s progress in the development of common systems and processes, as well as the common approaches to quality, safety and continuous improvement that have been taking place at the company’s assembly operations,” said Ron Harbour, president of Harbour and Associates.
“Over the last five years, GM has seen the most improvement of any manufacturer with more than one plant. The company’s manufacturing productivity performance continues to improve even though, like other companies, its percentage of higher content vehicles continues to grow.
“GM’s performance measures is a direct result of the company’s commitment to building a strong foundation in lean manufacturing,” Harbour added. “At long last, the company’s systems and processes are paying off in improved productivity, higher quality – as shown recently in the company’s improved performance in JD Power’s initial quality scores – and lower costs.
“This year’s results further confirm the strong correlation between quality and productivity,” Harbour added. “Many of the plants producing the highest rated vehicles in the quality rankings also fared well in the Harbour Report.”
Honda – one of first Japanese ‘transplants#; to build cars in America, starting with the 1979 Accord, achieved a low 31.18 labour hours per vehicle built and a per-vehicle profit of $US1661.
The profit figure reflects Honda#;s position as one of the last companies to offer incentives in the post September 11, and then mostly on the run-out Accord due to be replaced later this year. Honda also has waiting lists for its popular Odyssey minivan and is reportedly expecting its new Pilot SUV to be a similar sell-out success.
On the other hand, bottom-ranked DaimlerChrysler took 44.28 hours – over 13 more than Honda – to build each vehicle and posted a per-vehicle loss of $1679.
Ranked by direct labour hours per vehicle (HPV), Nissan was first for the eighth year in a row on 17.92 hours per vehicle, 3.2% down on the year before (results include Smyrna but exclude the Mexican Sentra plant) while Honda was second with 19.78 HPV, a 0.6% improvement on 2000.
Toyota, whose wholly-owned plants are in Kentucky, Indiana and Ontario, was third on 22.53 HPV, 4.3% down on the previous year.
Mitsubishi’s North American operation in Normal, Illinois, continued its rise as one of the fastest improving assembly plants in the Harbour Report. The plant’s HPV measure improved 8.6%, more than any other company, and enabled Mitsubishi to pass Toyota in the assembly rankings. Mitsubishi’s HPV has improved 41% over the last four years.
Mitsubishi#;s 21.82 HPV was the biggest improvement in assembly productivity. The company’s 8.6% improvement in 2001 followed an even bigger 21.6% improvement in 2000.
“Mitsubishi’s operation deserves credit for the dramatic improvements in its assembly productivity measures over the last few years,” Harbour said.
“The plant has undergone a remarkable transformation in a very short time.”
Honda and Toyota finished 1-2 in the engine productivity rankings, and GM had the best performance among the former Big Three. Toyota led the four-cylinder segment with an hours per engine (HPE) measure of 2.71, Honda was first in six-cylinder productivity with a 3.47 HPE, and GM led the way in V8 productivity with a 4.55 HPE.
Ford and GM each had three of the 10 most improved engine plants, but DaimlerChrysler had four of the most improved plants.
DaimlerChrysler, at 6.4%, was the most improved company in engine productivity, and moved past Ford in the company HPE rankings.
GM narrowly led DaimlerChrysler and Ford in transmission productivity while DC, which passed Ford for the second spot in the hours per transmission (HPT) rankings, led all participants in front-wheel-drive productivity while GM led the rear-wheel-drive HPT rankings.
Harbour said that the Japanese vehicle makers enjoyed an average of $350 to $450 profit advantage over US rivals for each vehicle they built last year.
While acknowledging the younger and non-union workforces and favourable yen-to-dollar exchange rate, Harbour added that the flexibility and efficiency of Japanese car makers’ factories is a major contributor to their results.
Harbour estimates the per-vehicle labour cost per vehicle for the Japanese factories is $428 less than GM’s and $356 less than Ford’s.
However, Harbour and Associates named General Motors’ Ontario assembly plant in Canada – where the Chevrolet Impala and Monte Carlo are built – as the most efficient North American assembly plant.
Nissan#;s car and truck plant in Smyrna, Tennessee – the first Japanese transplant which began building small pickup trucks in the late 1970s – and Ford’s Atlanta plant – soon to become the sole source for the Taurus – ranked second and third respectively.
GM improved the most in 2001 by assembly time 6.8% to 26.10 hours per vehicle, beating Ford whose 26.87 hours per vehicle was 4.4% slower than in 2000.
The Chrysler Group managed a small improvement of 1.4% to 30.82 hours per vehicle.
According to a report in the Detroit News, Ford blamed its poor productivity on inititatives begun last year to improve vehicle quality and eliminate image-damaging recalls such as the five for the new Escape SUV and the assembly track-inflicted tyre damage to new Explorers.
Those efforts pulled resources away from productivity projects, Ford#;s group vice president of manufacturing and quality, Roman Krygier, told the newspaper.
Krygier added that Ford’s quality initiatives would result in productivity gains next year.
“We’re very close [to GM] and we’re a very competitive group of people in the manufacturing organisation,” he told the Detroit News.
The Detroit News reported that the director of the Centre for Automotive Research in Ann Arbor, David Cole, said GM’s productivity gain “shows what can be done if you get your fundamental processes under control. I think you will see ongoing significant improvements in the GM numbers for some time.”
Cole and other industry experts attribute GM’s improved productivity to its efforts over the past 10 years to get all of its plants using the same manufacturing system so plants can now quickly learn from the mistakes of other GM plants, the Detroit News added.
Harbour and Associates said the North American automotive industry felt the impact of the economic downturn and catastrophic events that occurred in the United States in 2001.
The vehicle companies were forced to take a number of dramatic steps to maintain vehicle sales, which had a profound impact on their bottom lines. As a result, many companies struggled – and sometimes failed – to turn profits despite one of the best selling years in automotive history.
“More than ever, 2001 showed the critical importance production and manufacturing systems play on a company’s profit and loss margin,” Harbour said. “Today, lean manufacturing, and emphasis on quality, safety, and product and process engineering are key elements in almost every manufacturer’s continuous improvement efforts.
“As shown by the results in the Harbour Report, some companies are making greater strides than others.”