Major vehicle makers in the United States are increasingly moving operations into energy-efficient buildings if news this week from Ford and Toyota is any guide.
Ford is claiming to have installed the world’s largest “living roof” on a new truck plant in Dearborn, Michigan. The roof is 10.4 acres of sedum, a drought-resistant perennial groundcover, planted into a specially layered bed.
The roof material absorbs rain water and carbon dioxide and reduces energy costs by helping to insulate the final assembly building.
As a bonus, Ford claims it will last twice as long as a traditionally constructed roof.
The living roof is part of Ford’s ongoing redevelopment of its famous Rouge Centre, which includes a number of other environmental initiatives. The roof can absorb up to four million gallons of rain water annually and is part of a broader storm water management system installed at the Rouge.
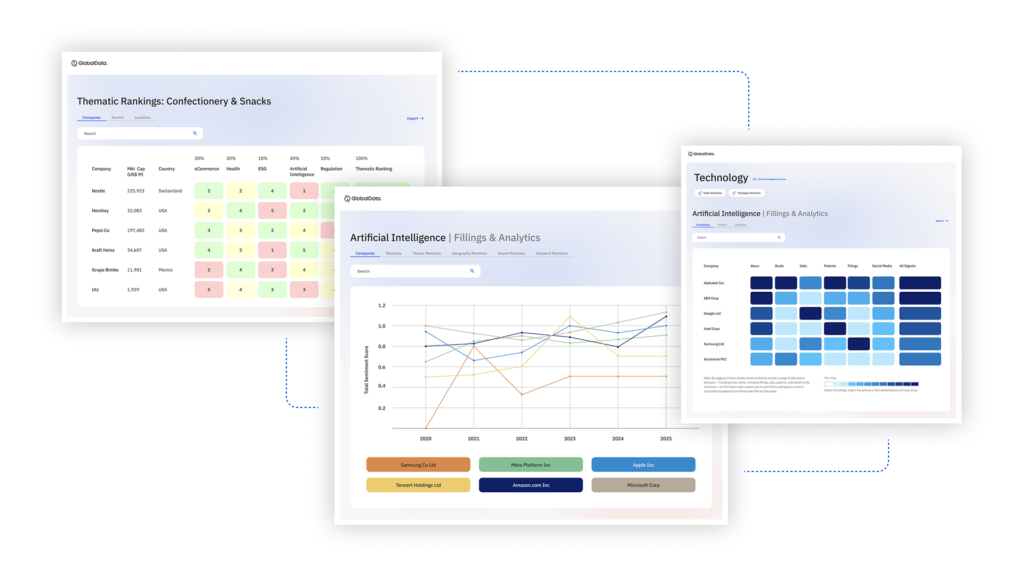
US Tariffs are shifting - will you react or anticipate?
Don’t let policy changes catch you off guard. Stay proactive with real-time data and expert analysis.
By GlobalDataOther than the watering required during its early growth stage, the living roof is maintenance free, requiring no mowing or trimming. On average, the sedum plants grow only six inches (about 15cm) tall and spread horizontally, crowding out weeds and other undesirable plants. When fully developed, the roof will resemble a meadow with varying lengths of growth and small red, white, yellow and purple flowers.
Rather than being planted in loose soil, sedum on the living roof grows on a four-layer, mat-like system that is only three inches thick. The bottom layer is a root-resistant membrane, followed by a drainage layer, a fleece mat, a vegetation blanket of semi-organic material and finally sedum plants.
When rain falls on the living roof, it is absorbed or filtered through the plant roots and soil bed. Excess run-off then is directed into an intricate storm-water management system composed of filtering rock beds and ground-level plantings; ditches filled with greenery, called swales; porous pavement installations; retention ponds; and underground storage basins.
Meanwhile, in Torrance, California, about 16 miles from downtown Los Angeles, Toyota employees are gradually moving into a new 624,000-square-foot Toyota Motor Sales campus that was designed to demonstrate that energy-efficient buildings made with a significant percentage of recyclable materials do not necessarily have to cost more than ordinary office developments, the New York Times (NYT) reported.
The paper noted that, while Toyota spent heavily on rooftop photovoltaic cells for its “green” South Campus complex — a cost officials said will take the company seven years to recoup — the company also saved money with a simple type of tilt-up construction that is commonly used to build warehouses. The steel-reinforced concrete exterior panels for the two three-story buildings were formed on the ground and lifted into place by large cranes.
What results is a “very mainstream” campus that could be emulated by just about any company, not just trendy design firms and environmental organisations, Toyota’s manager of real estate and facilities, Sanford Smith, told the NYT during a recent tour of the $US87 million complex.
The newspaper said the new complex, situated on 40 acres, will eventually house about 2,500 employees of Toyota’s financial services and customer service divisions.
The vice president and regional manager for Turner Construction Company, the general contractor for the Toyota project, David Seastrom, told the New York Times that the buildings themselves were built for about $US63 a square foot — within the range of $54 to $76 of most Southern California office parks – and calculated the cost of the interiors at about $26 a square foot, compared with $22 to $40 for other complexes.
The newspaper noted that Toyota is not the first car manufacturer to develop a green building. Both the American Honda Motor Company, with an 186,000-square-foot complex in the Portland, Oregon, suburb of Gresham, and Ford, with 300,000 square feet in Irvine, California, have been certified through a US Green Building Council programme that seeks to encourage environmentally-aware construction.
The New York Times report said the new Toyota building has grey-green carpet tiles throughout from a supplier whose contract requires it to reclaim the carpeting from the South Campus when it becomes worn, which is expected to be in 10 to 12 years. “We have to take it back and keep it out of the landfills,” a spokesman told the paper.
In addition to the solar power, which will meet 20% of the energy needs, company officials told the New York Times that the building had an array of energy-saving features – nearly all employees will work under natural daylight and motion sensors allow indirect lighting to be turned on in dark areas only as needed.
Toyota’s facilities operation manager, Mark Yamauchi, told the newspaper that the complex exceeded tough California energy standards by 20%.
Other green aspects include low-maintenance landscaping, with drought-tolerant plants and native grasses that are irrigated with recycled water. Steps were taken to protect indoor air quality, including housing copier machines in separate small rooms with their own exhaust systems and ductwork was capped at both ends before it was delivered so that it would not collect dirt while it was awaiting installation, the New York Times added.