The Chrysler group will reduce initial capital expenditures by 30% preparing for the launch of the redesigned 2004 Dodge Durango due to flexible manufacturing strategies and re-use of existing tooling, the unit’s head of assembly, stamping and component operations said during the 2003 Management Briefing Seminars in Traverse City, Michigan, on Monday.
Chrysler group vice president – assembly, stamping and component operations, Craig Corrington, discussed pre-launch activities at Newark Assembly as an example of the company’s flexible manufacturing strategy.
“The conversion of Newark Assembly Plant for the Durango is indicative of the company’s new direction for manufacturing,” said Corrington. “By applying flexible manufacturing principles in an existing facility with tooling from current Durango production, we are able to reduce our initial capital expenditures by 30%.”
According to Corrington, efforts at Newark demonstrate the group’s ongoing changes to further improve productivity and flexibility in its manufacturing operations. The facility recently underwent a conversion to re-tool existing equipment and processes, enabling both the current and new Durango to be built simultaneously on the same production lines during the model change over.
Corrington also said the plant was awarded the Clean Air Excellence Award from the Environmental Protection Agency for using a clear coat process developed by DuPont. While improving scratch and mar resistance on vehicles, the new paint reduces clear coat emissions by 25%. In addition, Newark Assembly has adopted a zero-waste landfill process, whereby waste is either recycled or sent to an incinerator, where it is converted into electricity.
How well do you really know your competitors?
Access the most comprehensive Company Profiles on the market, powered by GlobalData. Save hours of research. Gain competitive edge.
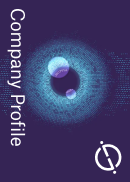
Thank you!
Your download email will arrive shortly
Not ready to buy yet? Download a free sample
We are confident about the unique quality of our Company Profiles. However, we want you to make the most beneficial decision for your business, so we offer a free sample that you can download by submitting the below form
By GlobalData“We are proving… that a brown field site can be transformed into a flexible operation,” Corrington said. “For our facilities, this belief goes beyond just assembly operations. It is being applied in our stamping plants and will continue to be rolled out, where appropriate, with each new vehicle we launch.”
As an example, unconventional applications of flexibility have helped Chrysler’s stamping facility in Twinsburg, Ohio, prepare for the Durango launch – the plant will produce major body components for the vehicle.
The Twinsburg facility is implementing a flexible system called Common Systems Architecture (CSA) – – a new model for the company’s stamping and body panel assembly operations. CSA significantly reduces the limitations of tooling changes that may be required over the manufacturing life of a vehicle. Under this concept, robotics and other equipment can be reprogrammed for model year changes, thereby eliminating or reducing production downtime.
CSA also provides a higher degree of precision in component production, ensuring that parts are produced according to specification the first time and at the quality levels that customers expect.
Corrington said that the benefits of a flexible system at Twinsburg stamping and Newark assembly will be reaped in a number of ways, including: cost savings due to future reduction in capital spending as well as lower scrap rates; the conservation of valuable manufacturing space during changeover; and the professional development of the plant workforce as a result of training on state-of-the-art equipment and robotic technology.
CSA is currently only being used for Durango production; however, Corrington said the applications will be far reaching. “We plan to apply this best-practice experience in flexibility across our manufacturing organisation.”