General Motors says it will save around $US100 million on each new vehicle introduced by using new technology, called C-Flex, to improve assembly plant flexibility along with other improvements to manufacturing processes.
C-Flex is a programmable body shop tooling system that is replacing body style-specific tooling, allowing multiple body panels to be welded with the same set of programmable tools and robots. Model-specific tooling is not required.
“The benefits of C-Flex are plants that can build a higher variety of differentiated products at much lower costs, “said GM North America president Gary Cowger in a statement.
“By linking our technology, product development and manufacturing plans, GM is able to deliver products to the market at a faster pace.”
According to Reuters, Cowger told reporters attending a press briefing at the C-Flex-equipped Lansing Grand River assembly plant: “Five years ago, we spent at least $150 million on a new body shop that was not very flexible.”
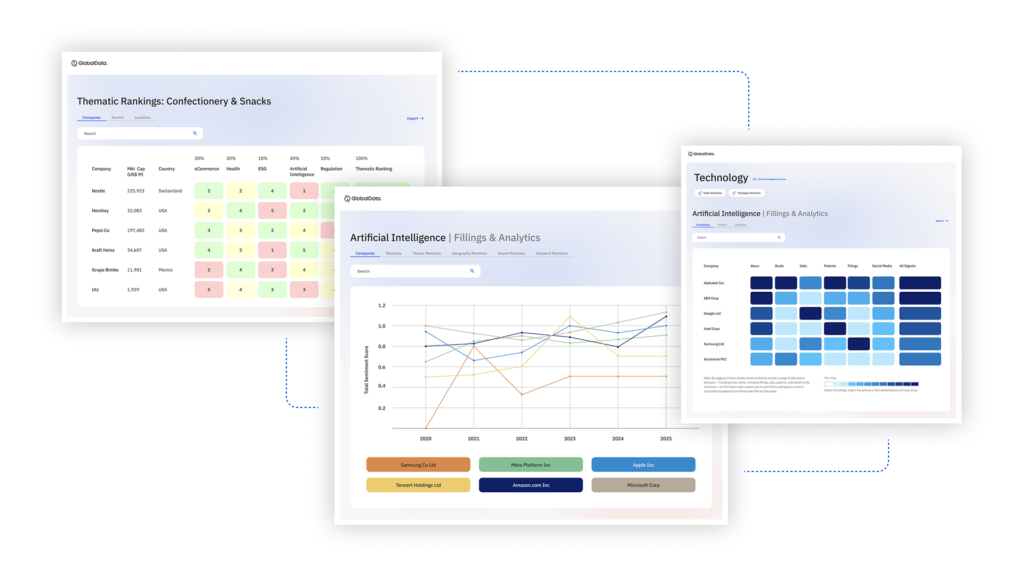
US Tariffs are shifting - will you react or anticipate?
Don’t let policy changes catch you off guard. Stay proactive with real-time data and expert analysis.
By GlobalDataWith the new system, GM is able to introduce a new model into a plant for as little as $30 million to $50 million, Cowger added.
“The less capital that is required to do a programme, the lower that break-even point,” Cowger said, according to Reuters.
GM initially launched C-Flex in its Moraine, Ohio, and Oklahoma City, mid-size sport utility vehicle assembly plants. The next application is at the Lansing Grand River plant, which is preparing to launch the Cadillac SRX luxury utility next summer. The plant is already building the CTS sedan.
C-Flex technology also will be installed in other GM assembly plants including the Lordstown, Ohio facility, which will build the Cavalier replacement, and the Orion, Michigan, that will make the next-generation Pontiac Grand Am.
Improvements in manufacturing flexibility are also driving increases in GM’s manufacturing capacity utilisation.
The company says current North American capacity utilisation is approximately 90% but it has publicly committed to increase this to 100% by mid-decade.
Assembly plants that are flexible generally have higher capacity utilisation and GM sees this higher utilisation as a critical element of generating higher earnings and reducing structural costs.
GM’s flexible manufacturing plans and its Global Manufacturing System are directly linked to its product development strategy.
The company is moving towards flexible, global vehicle architectures, which help reduce assembly plant complexity, increase plant efficiencies and enhance the company’s ability to quickly adjust product mix to better match market fluctuations. These will also help GM build lower volume ‘niche’ vehicles more efficiently and cheaply.
Common global manufacturing processes allow GM to build flexible vehicle architectures. While allowing for a variety of subsystems, interiors and exterior designs, the system requires that all vehicles in the same portfolio must “fit” any assembly line designated to build that architecture.