Mass market automakers, to compete in a crowded arena, increasingly are turning to small “coachbuilders” or engineering firms for help with distinctive low-volume vehicles that can strengthen a brand’s image far beyond their sales numbers, according to a report.
Major car companies are geared to build upwards of 100,000 of a particular model annually. Adding a vehicle such as a sports car, which sells in much smaller numbers, to an assembly line can be costly and severely disrupt the production process, executives told a news agency.
“We have to break some manufacturing rules to get some of these cool (design) proportions to appear,” Larry Achram, vice president of virtual engineering on the Chrysler Crossfire, told Reuters. “If it’s a niche vehicle, and you don’t have to build it in your own house, it’s much less expensive.”
The news agency noted that coachbuilders – a term left over from the horse-drawn carriage makers of a century ago – are common all over Europe particularly for building a one-off show car but industry officials see an opportunity for small companies to take a greater role in building production cars in North America, despite the overcapacity in the auto industry created by underutilised plants.
Coachbuilders are able to design, engineer or build a vehicle in half the time of a mass-market company, saving hundreds of millions of dollars, and absorbing much of the risk associated with any new car or truck launch, executives reportedly said.
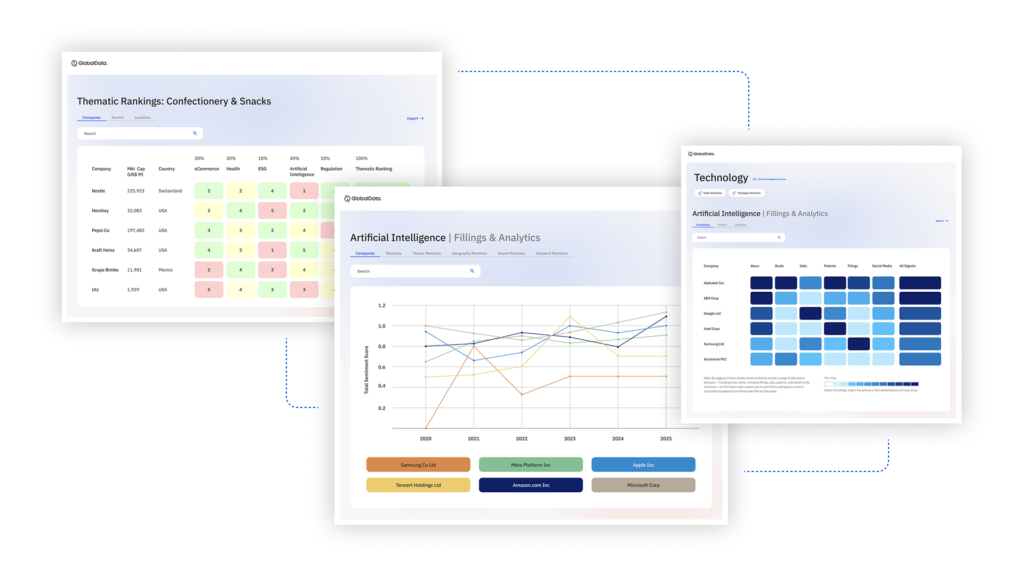
US Tariffs are shifting - will you react or anticipate?
Don’t let policy changes catch you off guard. Stay proactive with real-time data and expert analysis.
By GlobalDataCar designs, like fashion, appeal to the emotions, and automakers must strike quickly with a hit show vehicle before trends change.
“These things age. The ability to be very agile and fast is the key to success,” Mark Reuss, executive director of General Motors’ performance division told Reuters.
Investment by the niche manufacturers in assembly plants and expensive tooling machinery reportedly frees up capital for automakers to invest in future development of cars and trucks.
“It gives (car companies) opportunities to take things off the balance sheet, because all the tools are taken on by suppliers,” Tim Olind, chief operating officer of Karmann USA, a unit of Germany’s Wilhelm Karmann GmbH, told the news agency.
Karmann, which builds the Crossfire as well as the Audi A4 and Mercedes CLK convertibles in Germany, broke ground in July for a 144,000 square-foot facility in Plymouth, Michigan, to engineer and eventually build cars, Olind reportedly said.
One of the first cars the facility will work on will be GM’s Pontiac G6 convertible, Reuters said – the first mass-market retractable hardtop car to be built in North America in years, it goes into production in 2005.
With the car market fragmenting and consumers demanding more choices, the number of nameplates, or individual vehicles, in the United States has grown well past 300, from about 250 four years ago, the report said – the average sales volume per nameplate, excluding pickup trucks, has dropped to around 40,000, from more than 100,000 15 years ago.
Canadian auto parts company Magna International, which also builds the BMW X3 sport utility and DaimlerChrysler’s Jeep Grand Cherokee SUV at its Magna Steyr plant in Austria, reportedly has said it could add an assembly plant in North America.
Magna would consider building a new facility or taking over an existing assembly plant from a down-sizing automaker, a spokesman told Reuters.
The Chevrolet SSR, a pickup/roadster crossover, would be just another show car without ASC Inc., which changed its name from American Sunroof Company to American Specialty Cars earlier this year as the engineering and design company expanded the scope of its work, the report said.
The SSR was a big hit when it was unveiled as a concept at the Detroit auto show in 2000, but GM reportedly had difficulty figuring out how to build the low-volume truck profitably.
“The SSR was named dead in the water in GM internally, from a financial standpoint,” Jeff Steiner, ASC executive vice president and chief marketing officer, told Reuters.
The report said ASC’s solution was to build a plant in Lansing, Michigan, to assemble 42 major SSR subcomponents, including the instrument panel and retractable roof – ASC cut costs by using some obsolete equipment, a less-sophisticated production line, and more manual labour than an average high-tech assembly plant.
Virtually the entire SSR passes through the ASC plant before it is shipped nearly five miles to a previously underutilised GM plant for final assembly, Reuters said.
Both the SSR and the Crossfire are making profits for the carmakers, executives told the news agency.
“We wouldn’t have gotten the car if we had not done it that way,” GM’s Reuss told Reuters. “We really hadn’t done anything like that before.”
Automakers in Europe have long appreciated the value of coachbuilders when it comes to producing niche models. For example, General Motors Europe contracted Bertone to build its outgoing Astra coupe and cabriolet models and the just-launched Tigra roadster, Saab has long outsourced the building of its 9-3 convertible and Mitsubishi has its small SUV, the Shogun Pinin, built by Pininfarina.