Global Engine Manufacturing Alliance (GEMA) president Bruce Coventry claims a non-traditional approach will save DaimlerChrysler $US100 million a year and make his operation competitive with the world’s best.
GEMA’s “World Engine” is a family of small four cylinder petrol engines co-developed by DaimlerChrysler’s Chrysler Group, Hyundai Motor Company and Mitsubishi Motors Corporation.
“The Global Engine Manufacturing Alliance engages the full capability of our international alliances,” said Coventry. “Engine development costs were minimised. We’re focused on manufacturing flexibility and implementing the principles of lean manufacturing.”
Total world engine production – which includes output from two plants in Dundee, Michigan; one in Asan, South Korea; Hwasung, South Korea; and Shiga, Japan – is expected to be more than 1.8 million units per year.
Volumes of those kinds allow bundled parts purchasing to maximise cost savings. Purchased components like pistons, valves, connecting rods, fuel injectors, oil pumps, valve springs and camshafts have all been sourced from a broader base of suppliers, in greater quantities, at significant savings and with more performance features than the current family of Chrysler four cylinder engines.
How well do you really know your competitors?
Access the most comprehensive Company Profiles on the market, powered by GlobalData. Save hours of research. Gain competitive edge.
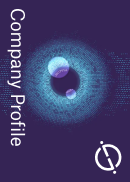
Thank you!
Your download email will arrive shortly
Not ready to buy yet? Download a free sample
We are confident about the unique quality of our Company Profiles. However, we want you to make the most beneficial decision for your business, so we offer a free sample that you can download by submitting the below form
By GlobalDataCoventry said three philosophies make the alliance different.
The first is a mission to target value. One example includes standardized machining centres with commonly available machines to reduce capital investment requirements and programme lead times.
The second is a goal to mitigate risk. An example is to use suppliers with proven engine manufacturing and support experience in all three markets – the United States, South Korea and Japan. Other examples include introducing procedural “speed bumps” to slow down potentially costly design changes; maintaining a common base engine; ensuring that changes enhance the product for all partners; and limiting unilateral changes in order to maximise volume bundling strategies.
The third philosophy is optimisation.
“We’re focused exclusively on the manufacturing and assembly of the engines,” said Coventry. “We rely on service providers for everything else. We’ve also minimised development costs by optimising – matching needs to expertise. DaimlerChrysler, for example, took the lead in development of the dual variable valve timing (VVT) system and validation. We’ve utilised the development and manufacturing knowledge and experience of each team to enhance the final product while reducing or containing cost.”
Design and manufacturing efficiencies have also allowed the alliance to build high-performance features into the engine without giving it a “premium” price tag. Those features include variable valve timing, high-pressure die-cast aluminium engine block, forged-steel crankshaft and select-fit pistons, tappets and bearings. Engines of three different sizes will be manufactured, with 1.8-, 2.0- and 2.4-liter displacements, with horsepower and torque targets that rival today’s V6 engines.
“This is not your father’s factory,” said Coventry. “We’ve adopted ‘enablers’ to enhance our productivity and efficiency.”
The “enablers” include a proposed four-day / 10-hour work schedule that would increase equipment availability while providing employees with more family time. The plant is expected to run 294 days a year, without overtime, giving GEMA more productivity per year at less investment than typical plant schedules.
A rigorous hiring process targets highly qualified team members, who are organised in to a single “technician” classification. Candidates must possess a two-year technical degree, a skilled-trades journeyman’s card or have significant computer numerical control (CNC) experience. Candidates are then put through a five-step selection process to test technical aptitude and team skills. The goal, according to Coventry, is to create the most qualified and productive engine building team in the industry.
The alliance also adopted new machining processes to maximise productivity.
“Flexible machining centres in a hospital-clean manufacturing environment are the basis to the GEMA business model,” said Coventry. “Compared to the traditional transfer line process, this model incorporates part recognition and automatic changeover features to allow different products to flow down the line seamlessly; even allowing for a batch size of one. An even greater benefit that machining centres give us over transfer lines is uninterrupted flow, even if there is machine downtime.
“In the end, we’re creating a final product with higher precision, better performance and durability that greatly exceeds each partner company’s previous standards.”