Advanced High-Strength Steels (AHSS) combined with sheet hydroforming show
potential for further mass reduction in steel vehicle body outer panels, the
UltraLight Steel Auto Closures (ULSAC) consortium said this week.
To explore the benefits of such steels, the consortium successfully manufactured
door outer panels using 0.6 mm dual phase (DP) 600 steel sheet.
The consortium specified sheet hydroforming to increase work hardening in the
centre of the panel, which hydroforming does more effectively than stamping.
The AHSS approach resulted in an additional 0.7 kg of mass savings over the
already significant amount achieved in the original study, which produced lightweight
frameless doors (with stamped outer panels) weighing 10.47 kg.
The additional saving of 0.7 kg boosted the mass improvement from 42 percent
to 46 percent over the average benchmarked frameless door.
"These doors are lightweight, efficient structures that offer superb crash
performance, and they are affordable to manufacture in large quantities,"
said the American Iron and Steel Institute’s senior director of automotive
applications, Darryl Martin.
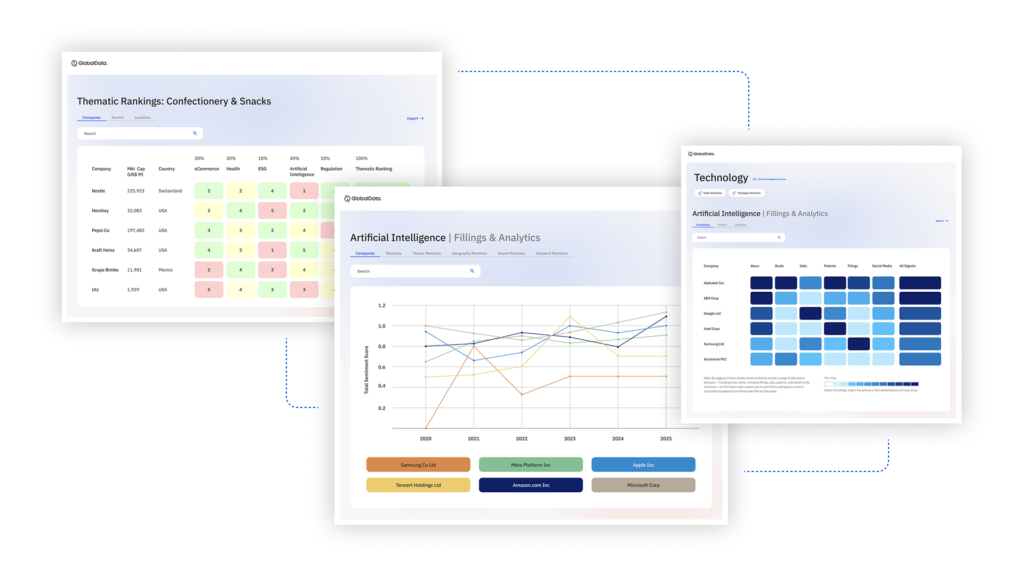
US Tariffs are shifting - will you react or anticipate?
Don’t let policy changes catch you off guard. Stay proactive with real-time data and expert analysis.
By GlobalData
PWC
– |
"The use of advanced high-strength steels demonstrates ongoing potential
for reducing mass in automotive body panels, while maintaining dent resistance
and eliminating ‘oil canning’ tendency.
“The results show that the unique work hardening qualities of dual phase steels
yield excellent performance when a sufficient amount of stretch is achieved
in the centre area of the panel."
While advanced high-strength steels are being used with other processes, like
tube hydroforming or stamping, the consortium conducted research on the sheet
hydroforming process, gaining valuable documentation about this developing technology.
The ULSAC program, which began in 1998, included a concept phase that produced
designs for lightweight doors, bonnets, boot lids and rear hatches.
A validation phase followed with the manufacture of a frameless door to demonstrate
the feasibility of the lightweight closure concepts.
The first doors produced weighed just 10.47 kg, which included a stamped outer
panel of 0.7 mm thickness bake hardenable (BH) 260 steel.
The ULSAC consortium reported on these results in May 2000.
The auto closures (ULSAC) programme is a study undertaken by the global steel
industry to demonstrate the effective use of steel in producing lightweight,
structurally sound steel automotive closure panels that can be affordably manufactured
in production volume.
The ULSAC Consortium consists of leading steel companies around the world.
To view related research reports, please follow the links |