This week, Nissan will ramp up US assembly of the 2013 LEAF EV at its manufacturing plant in Smyrna, Tennessee, where it will be made alongside some of the automaker’s petrol-powered models.
The assembly start in Smyrna follows the opening of an adjacent battery plant. Nissan said it is the only automaker to make its own electric vehicle batteries, at the largest lithium-ion automotive battery plant in the US.
It has plans to start similar battery and EV making at its plant in Sunderland, north east England, later this year.
Nissan said LEAF assembly requirements are much more similar to those of traditional petrol models like the Altima and Maxima with which it shares a manufacturing line. Adding the electric vehicle required only a few process changes such as the addition of quality checks specifically for electric vehicles and special training for technicians.
Toyota’s factory near Derby, England, made much the same changes when it started making Auris hybrids – using nickel metal hydride rather than lithium ion batteries – on the same line as petrol models in 2010.
“Process efficiency is a never-ending activity for us. We strive to create new internal benchmarks in efficiency with each new model. By assembling the LEAF on our current Altima and Maxima line, we are able to reduce costs by using existing equipment,” Nissan Smyrna manufacturing chief Susan Brennan said.
How well do you really know your competitors?
Access the most comprehensive Company Profiles on the market, powered by GlobalData. Save hours of research. Gain competitive edge.
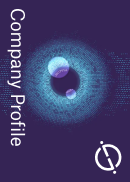
Thank you!
Your download email will arrive shortly
Not ready to buy yet? Download a free sample
We are confident about the unique quality of our Company Profiles. However, we want you to make the most beneficial decision for your business, so we offer a free sample that you can download by submitting the below form
By GlobalData“For example, while gas-powered vehicles receive fuel tanks and internal combustion engines when they come down the line, the LEAF gets a lithium-ion battery pack made at our battery plant next door and an electric motor produced at the powertrain plant in Decherd, also in Tennessee.
“We truly have localised US manufacturing of the major components across the board,” she said.
EV assembly in Smyrna will contribute to Nissan’s goal to manufacture 85% of its US sales volume in North America by 2015 and having more local content will reduce exposure to fluctuations in foreign currency. Adding LEAF and battery assembly has created over 300 manufacturing jobs, a number that could increase with demand.
“The LEAF has expanded beyond early adopters and is now appealing to a broad spectrum of consumers,” claimed Nissan’s US sales and marketing head Brian Carolin.
“Since we launched the LEAF in 2010, we’ve learned that people are very attracted to the advanced technology and other amenities but they are also looking for a more affordable price point.”
The 2013 model year changes include 240 volt charging (US standard household voltage is only 120V) which is nearly twice as fast as the previous model, as well as a broader range of trim levels starting with a more affordable S grade, moving up through the SV to a top SL, plus two new paint colours.
Many critics have disliked the Japanese-made LEAF’s ‘hearing aid beige’ light interior colour so US buyers are now offered optional black leather and a top Bose audio system. just-auto expects the upcoming UK-built versions for Europe will also have a dark interior and other updates similar to the US model line.
After two years’ sales, Nissan claims global leadership in electric vehicle sales with about 50,000 LEAFs sold to date, of which 19,500 alone are on the road in the US.