Bankrupt auto supplier Delphi on Monday claimed its newly developed ‘steel hybrid cross-car beam’ is an industry first that combines components of five highly technical vehicle subsystems into one package that saves space, reduces mass, and reduces warranty and other costs by up to an estimated 15%.
“Streamlined subsystem engineering produces below-the-surface performance benefits including optimised crashworthiness [and] side impact protection, the company said in a statement.
The beam integrates the cross-car structure, heating, ventilation, and air conditioning ducting and case support, airbag system, steering column and electrical component supports into one beam made of steel over-moulded with plastic.
It is able to reduce overall part count while maintaining serviceability and integrity of the vehicle steering column support, HVAC, electrical, centre stack (console) and energy-absorbing components, Delphi said.
“Only a supplier such as Delphi, with a depth of engineering expertise in every vehicle subsystem, could develop and manufacture this product,” claimed Delphi executive Lon Offenbache.
How well do you really know your competitors?
Access the most comprehensive Company Profiles on the market, powered by GlobalData. Save hours of research. Gain competitive edge.
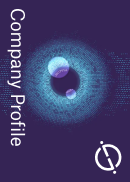
Thank you!
Your download email will arrive shortly
Not ready to buy yet? Download a free sample
We are confident about the unique quality of our Company Profiles. However, we want you to make the most beneficial decision for your business, so we offer a free sample that you can download by submitting the below form
By GlobalData“We were able to develop, prototype, test and manufacture the [beam] completely in-house. It is on-the-shelf technology we are offering to our customers and we’re confident they will see its clear value proposition.”
The process begins with proprietary welding methods that result in an engineered steel structural member which then undergoes an over-moulding process. Rather than using separate brackets for attaching subsystem components, attachment features and functional components are moulded directly into the beam.
Delphi said such an integrated design offers cost savings to vehicle makers while offering enhanced dimensional stability, reduced component part count and assembly labour, and reduced mass compared to a traditional design.
Additional subsystem efficiencies are gained from the integration, such as better performance in squeak and rattle as well as a reduction in the number of possible HVAC leak paths.
Engineering all of the individual subsystems into one part results in up to 50 millimetres (about two inches) of additional space in an area of the vehicle where ‘real estate’ is at a premium. Crashworthiness and side impact protection are optimised because the beam passes straight through the HVAC module rather than bypassing it.
The beam design helps assure cross-car structural performance, a major contributor to achieving five-star side impact ratings, Delphi added.
“It brings forth a new way of thinking about how the industry designs and develops the vehicle systems that come together in a cockpit module,” noted Offenbacher.
The company said the beam is already production-ready and targeted at 2009 model year vehicles.