General Motors is doubling the size of what it claims is the largest and most technologically advanced automotive battery lab in the United States to increase the pace of development of electric vehicles.
It has announced a US$8m investment to improve on-site testing of all current and new battery cell, module and pack technologies by enlarging its Global Battery Systems Lab on the GM Technical Center campus in Warren, Michigan, by 30,000 sq ft to 63,000 sq ft
Areas previously used for engine testing will be renovated for battery development, with construction beginning this month and scheduled for completion in the summer.
GM’s executive director, global electrical systems, hybrids, electric vehicles and batteries, Micky Bly, said: “GM is building on its commitment to lead the development of electric vehicle technology – from battery cell design to the charging infrastructure. This addition will benefit consumers by helping us put cleaner, more efficient vehicles, including the Chevrolet Volt electric vehicle with extended range, on the road more quickly and affordably.”
The lab began operations in January last year and became fully operational the following May. It is used by over 1,000 GM engineers working on advanced batteries and electrically driven vehicles. More than half of the current lab is dedicated to testing the electrochemical battery cells and their enclosures, known as modules. The lab’s remaining floor space is committed to evaluating completed battery packs.
The expansion will add capability in six areas, including:
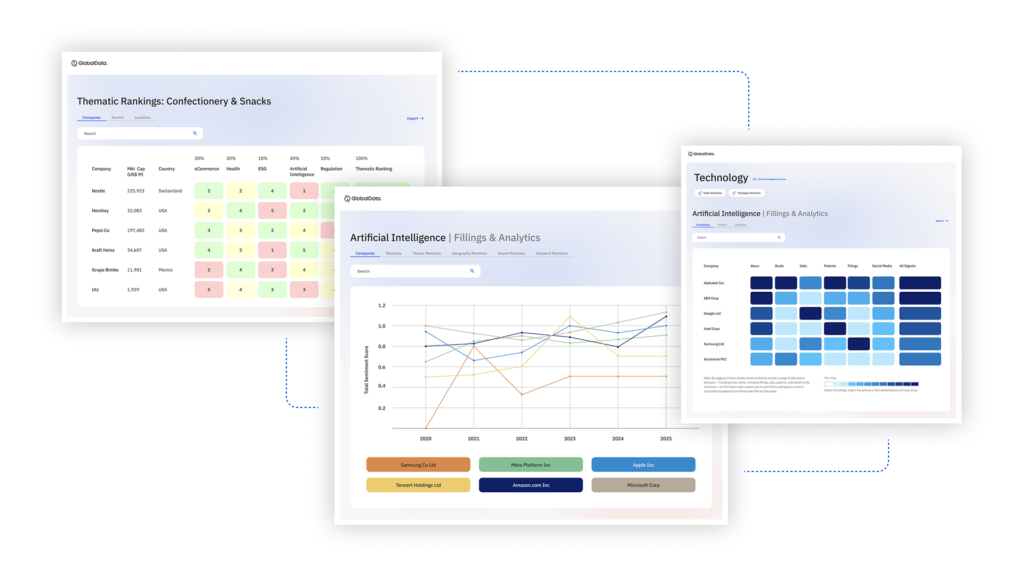
US Tariffs are shifting - will you react or anticipate?
Don’t let policy changes catch you off guard. Stay proactive with real-time data and expert analysis.
By GlobalData- Safety and Abuse Tolerance – Powertrain test cells previously used for engine altitude testing will be retrofitted for crush, penetration, water immersion, overcharge, discharge and short circuit tests.
- Buildup and Teardown – Reuse storage areas to prepare batteries before tests and provide secured rooms for supplier evaluation
- Manufacturing Engineering – Reuse space previously occupied by engine dynamometers to improve manufacturing processes, such as laser welding and cell stacking
- Charger Development and Integration
- Thermal Development. Radiant heat, thermal stability and thermal shock testing
- Battery Storage
The lab equipment and test automation systems are being integrated with GM’s global network of battery labs, including Mainz Kastel, Germany, and Shanghai, China.