Interface Sealing Solutions, a US-based Tier One supplier, has constructed a new manufacturing facility for its Select-a-Seal (SAS) second generation gasket line.
These rubber-edged composite gaskets are claimed to provide unique adhesion advantages plus stable bolt-load retention at temperatures up to 175 degrees centigrade.
The new plant is equipped with new frame-cutting equipment that supplements existing production capabilities and includes all the steps – coating, curing and inspecting – required to produce the new SAS seals.
The new facility has three significant manufacturing upgrades: new integrated logistics that streamline cutting operations, providing more control over production timing and product quality, improve production scheduling and shorten lead times; a new coating process that enhances productivity by decreasing downtime between coating cycles so that hroughput at coating will increase by 200% to 300% while maintaining a consistent polymer edge; and an automated inspection station.
Interface said contingency planning demanded by its customers and sales growth for the SAS technology require the addition of a new manufacturing facility. The new plant addresses both volume and flexibility requirements, and provides the space required for a lean manufacturing layout using a modular system.
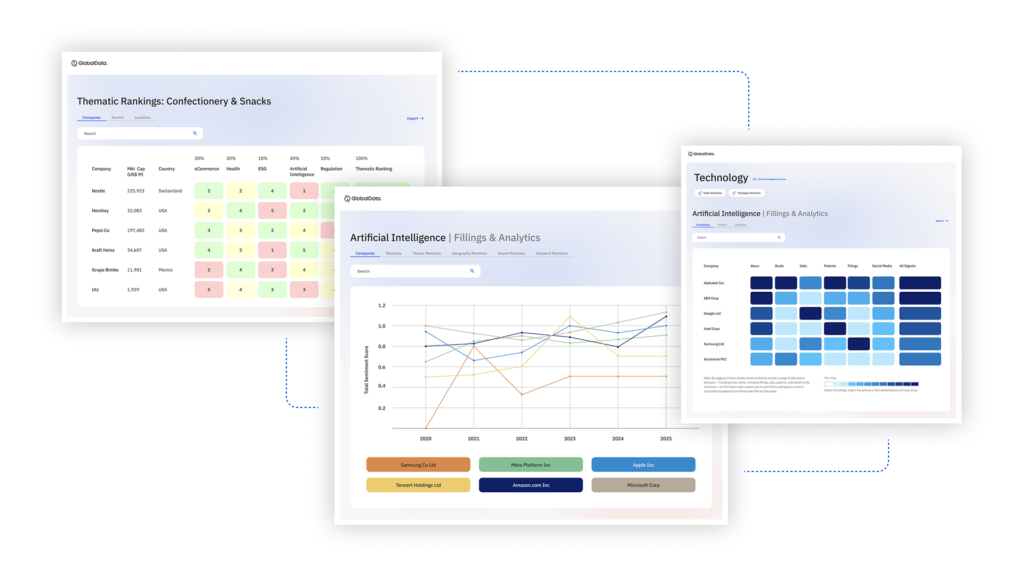
US Tariffs are shifting - will you react or anticipate?
Don’t let policy changes catch you off guard. Stay proactive with real-time data and expert analysis.
By GlobalDataTo meet anticipated future requirements, additional production modules will be added at the new plant as needed. The new site is large enough to accommodate three cells and an area for new sealing products under development. Each modular production line at the new plant will be tailored to make a specific range of products.
Modules can be moved, and a new module can be located virtually anywhere (for example, near an OEM’s plant).