Ford on Thursday revealed is developing a new environmentally friendly anti-corrosion technology that cuts water use in automotive paint shops by almost half and reduces sludge production by 90%.
The new technology, currently being field-tested on a small fleet of Lincoln Town Cars, takes the entire pre-treatment process down to eight steps from the current 13 parts of the conventional pre-treatment process.
The new process uses a zirconium oxide vehicle bath, which is more environmentally friendly than the currently used zinc phosphate because zirconium oxide doesn’t contain heavy metals found in the phosphate bath.
As a result, Ford said, there’s a 40% savings in water usage and significantly less waste to be processed into non-hazardous sludge and taken to landfills. Additionally, it doesn’t require heated water to work, saving energy costs.
“Pre-treatment is an important anti-corrosion step in the paint process, but the conventional method is harder on the environment,” said Tim Weingartz, manager, paint materials and strategy, at the automaker. “With this new pretreatment technology, Ford continues to lead the industry in environmental solutions to manufacturing processes.”
How well do you really know your competitors?
Access the most comprehensive Company Profiles on the market, powered by GlobalData. Save hours of research. Gain competitive edge.
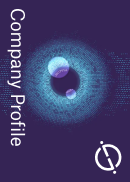
Thank you!
Your download email will arrive shortly
Not ready to buy yet? Download a free sample
We are confident about the unique quality of our Company Profiles. However, we want you to make the most beneficial decision for your business, so we offer a free sample that you can download by submitting the below form
By GlobalDataAnother benefit the automaker found is that, zirconium oxide covers the sheet metal with a uniform film compared with the crystal-like structures of the phosphate system. This has potential for more robust corrosion resistance.
Field tests will continue through 2008 when Ford will determine its roll-out to its paint shops in North America.