Ford is putting the equivalent of 10 years and 150,000 miles of wear and tear on hybrid vehicle batteries using a new lab test that takes less than a year to complete.
The automaker developed a new ‘key life test’ specifically for lithium-ion (li-ion) batteries, drawing on 20 years of extensive data and experience.
The test allows engineers to simulate in a lab setting many factors, including location of a battery within a vehicle, the temperatures they might have to endure, and various kinds of acceleration and braking that different drivers would apply. The scope of the testing also includes the ability to put 150,000 miles (the equivalent of about 10 years of average use) on the test batteries in about 10 months.
The test aims at delivering higher quality and more reliable batteries, said Kevin Layden, director of Ford’s electrification programmes.
Battery reliability ranks as the single most important purchase consideration by potential hybrid customers – topping 17 other factors such as fuel economy and safety feature count, according to a recent survey.
“Recent studies show consumers are keeping their vehicles longer, and regulations in some regions now require batteries to carry warranties for greater distances,” said Layden. “Fortunately, our tests take into account distances and conditions that go way beyond those normal requirements.”
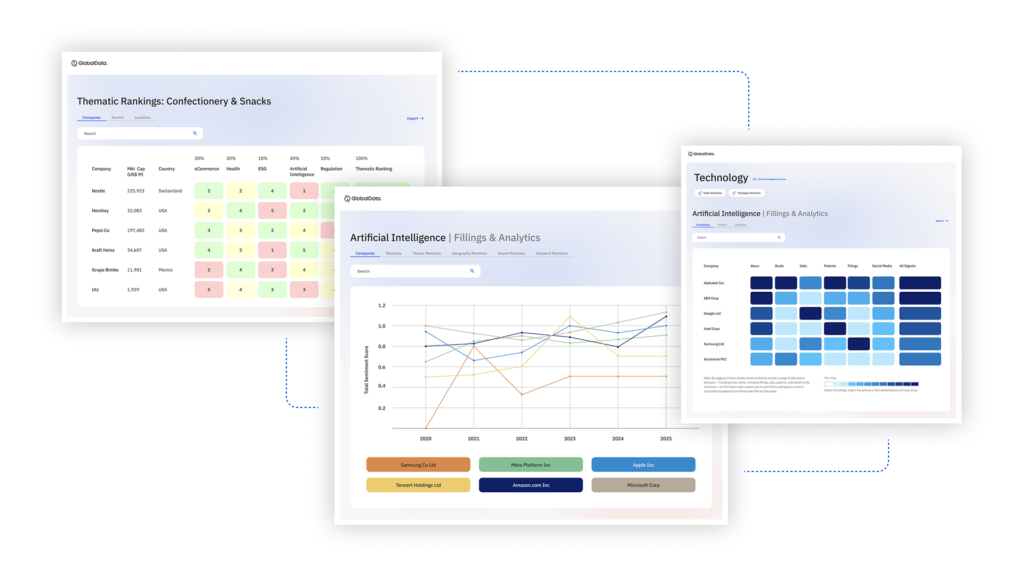
US Tariffs are shifting - will you react or anticipate?
Don’t let policy changes catch you off guard. Stay proactive with real-time data and expert analysis.
By GlobalDataFord will offer five electrified vehicles by 2013 with li-ion batteries. Previous generation vehicles have nickel metal hydride (NiMH). Li-ion batteries are 25% to 30% smaller and provide about triple the power per cell.
Other battery tests include simulating hot and sunny Phoenix weather by subjecting batteries to 140F-plus temperatures, extreme cold in Manitoba, Canada with frigid 40F tests, and by driving vehicles through ditches filled with water.
Ford’s experience with hybrids dates back to the late 1980s. The technology evolved quickly, resulting in a limited release Ranger EV in 1998, the Escape Hybrid in 2004 and the Fusion in 2009.
About 50m battery cells have been produced since 2004 for previous-generation production Ford vehicles.
Some of these have been used in taxi fleets in San Francisco and New York with some vehicles covering over 250,000 miles individually and fleets in California running nearly 100m miles.
So far, only six cells have failed.
“We can’t do an apples-to-apples comparison between the nickel-metal-hydride and lithium-ion batteries,” said Mazen Hammoud, chief engineer, electrified powertrain systems.
“But we can evaluate much of the data collected to see how hybrid vehicles are driven, the kinds of conditions they face and the demands that are placed on them. Knowing all of that helps us benchmark our tests and ensure the lithium-ion batteries are meeting or exceeding expectations.”
Ford is spending US$135m designing, engineering and making key EV and hybrid components – including doubling its battery testing capabilities – for the five current electrified vehicles due in its range by the end of the year: Fusion hybrid and Energy plug-in, C-Max hybrid and Energy plug-in and the Focus Electric.
It now has over 1,000 engineers working on electrification, based at a dedicated 285,000 sq ft centre in Dearborn, Michigan.
This investment in people and infrastructure is paying off: the automaker has reduced the cost of its current hybrid system by 30% compared with the previous generation and vehicles are going on sale 25% faster.