Ford needed the most amount of help of all the Detroit Three automakers and, judging from the results of the contract just agreed with the United Auto Workers (UAW), it would appear that it received it, Global Insight auto analyst Aaron Bragman said in a research note on Friday.
“From a financial standpoint, the company has been able to significantly reduce the gap seen between the profitability of Asian brand vehicles assembled in the United States and that of the domestic brand vehicles,” he wrote.
Ford CEO Alan Mulally this week outlined the financial specifics of the company’s new contract, now ratified by the UAW rank and file.
The new plan will trim labour costs by nearly $US1,000 per vehicle, according to the CEO, and is directly responsible for the company’s decision to kill a proposed low-cost assembly plant that it had announced last year. That plant was slated to help the company bring its manufacturing costs in line with the benchmark Asian transplants, but had drawn the ire of the UAW, which was announcing new concessions just as news of the low-cost plant broke.
According to Bragman, Mulally and fellow executives gave two reasons for the decision to scrap the plant: the new UAW contract’s two-tier wage provision, and the newfound flexible manufacturing ability that has been enabled.
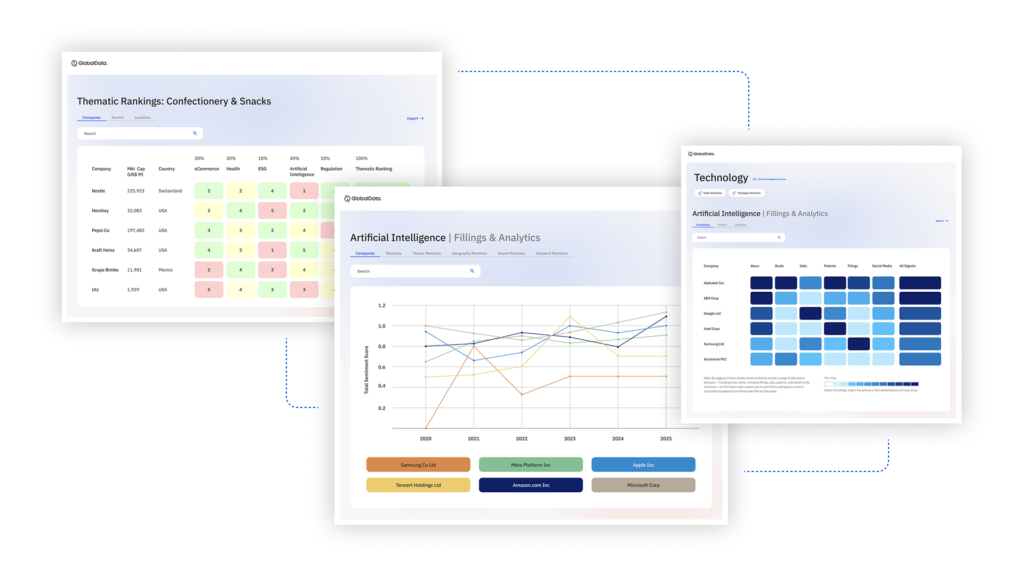
US Tariffs are shifting - will you react or anticipate?
Don’t let policy changes catch you off guard. Stay proactive with real-time data and expert analysis.
By GlobalDataUnder the two-tier wage system, Ford will be able to pay all new hourly workers hired after 1 January 2008 a base wage of just $14.20/hour. With healthcare benefits and a retirement contribution, the company figures that total cost would come to US$26.00/hour, less than half of what it pays its current hourly UAW staff.
Unlike GM and Chrysler, Ford will be able to pay this amount to all of its hourly employees, regardless of role – there is no ‘core vs non-core’ role definition as seen in the Chrysler and GM contracts agreed earlier, potentially enabling Ford to employ many more people by%age at the lower tier wages than the other two.
But unlike the other two contracts, Ford faces a cap of 20% of all UAW employees paid at the lower wage rate. Cost savings to Ford could amount to as much as US$2.4bn, money which Mulally says will be pumped into vehicle product development.
Ford will also be installing flexible body shops in its plants that do not already have them, according to manufacturing chief Joe Hinrichs. This will enable Ford to change the model it produces based on customer demand, and allow the company to better respond to changing consumer trends and tastes.
The ability to shift production to different models eliminates the need for the new plant, according to the company. “Our fundamental plan is to match our capacity to demand and increase efficiency year over year,” said Mulally, aping the kind of strategy that has been so successful for the highly flexible Asian transplant automakers since their arrival in the United States.
Bragman said Ford also detailed the new VEBA trust that will be set up under the new contract, a deal that is expected to reduce the company’s annual healthcare costs by $2.0bn.
“The company will eliminate $23bn in liabilities to the union, but will only be required to fund $13.2bn of those liabilities,” he noted.
“That funding will comprise $2.7bn in cash, $3.3bn in proceeds from the company’s issuance of a convertible note, $3bn from a second-lien note, deferred payments of $400m, and up to $3.8bn from an existing trust. The new fund would not take effect until 2010.”
Bragman said most of that cost comes from the elimination of the constant payments for healthcare, but the ability to reduce the wage rate for 20% of the company’s workers is also key.
“But this may prove to be challenging for the company,” he wrote. “[Ford] now has the ability to reduce their labour costs by 10%, once the full 20% of their hourly workforce is at the lower-tier wage.
“But Ford has a significantly younger workforce than GM or Chrysler (especially GM), which means that Ford is going to have to entice its hourly workers to leave the company, if it is going to hire in as many new workers as possible to get to that 20% cap as quickly as possible.
“Early retirement is unlikely to net everyone they need, meaning that announcement of additional buyouts is almost certainly going to occur. Ford will need to spend considerably to get younger employees to leave the company; what is not clear is whether or not those employees would be welcomed back at the lower wage rates, after having already taken the significant buyout packages.”
He added that the $2.4bn in savings is something that the company is going to need desperately in future to fund vehicle product development.
Bragman said Mulally was not specific in where the money would be spent, but the company has no shortage of projects which could benefit from an infusion of cash.
New marketing guru Jim Farley, recently arrived from Toyota, will also need cash for the new programmes and directives that he wants to initiate in improving Ford’s marketing.
“But despite the apparent win of the new contract for Ford, concerns still abound about the progress of the company’s turnaround plan,” Bragman said. “Some of the new products are not finding success (such as the new Taurus), while others are selling rather well (Edge CUV). With next year still looking like a very down year for vehicle sales (Ford is predicting another 18 months of soft sales in the United States before a rebound in 2009), fresh product and strong marketing efforts are going to be key for success in a highly competitive market.
“Ford has a couple of new vehicles coming in 2008, but the need is for a strong line-up across the board, and to create such a line-up requires a lot of cash. Ford’s revenues have improved due mainly to model mix, but the company has shrunk itself about as far as can be done without cutting muscle along with fat.”